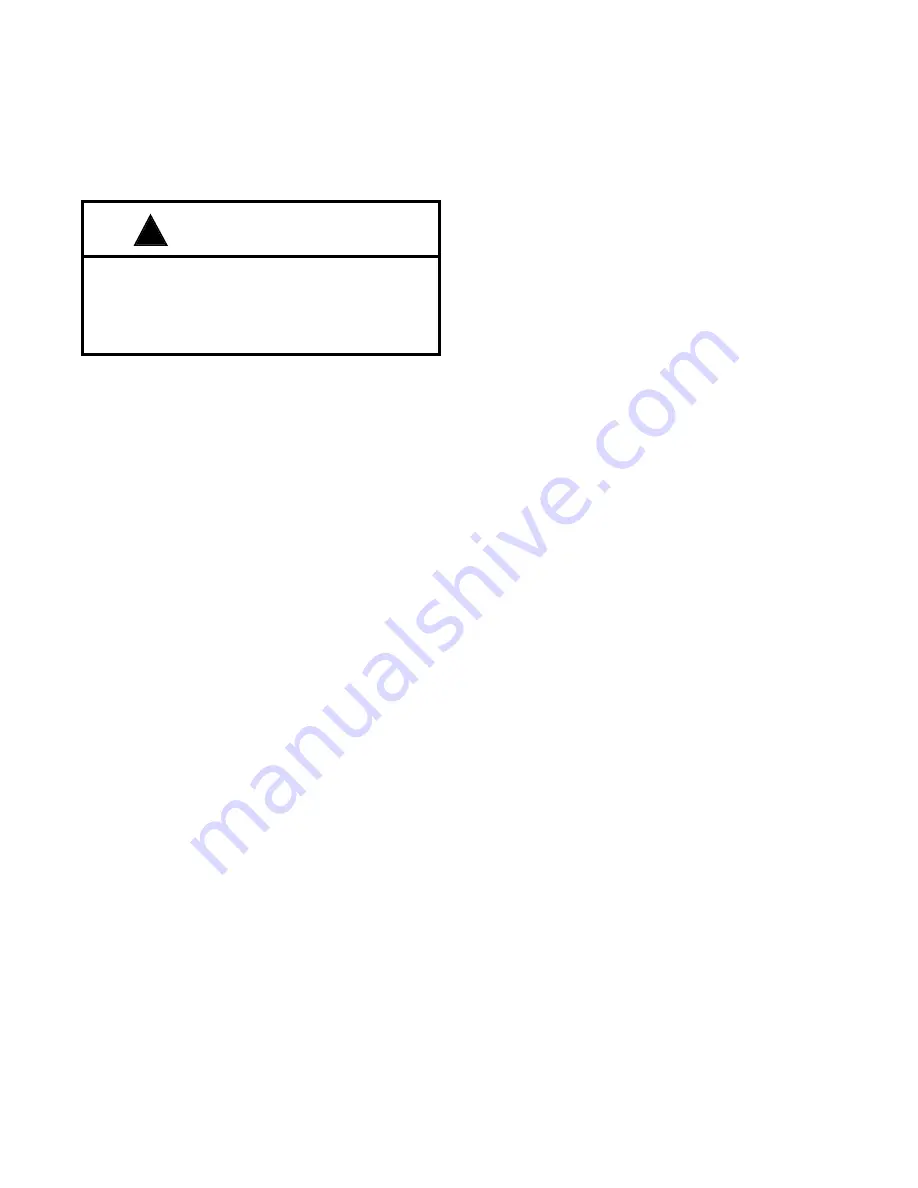
5. Discharge all air pressure from counterbalance
surge tanks and cylinders at the air regulator or
the remote drain cock. To be certain all pressure is
released from the cylinders, disconnect the air
supply lines that feed, and are directly attached to,
the cylinder unit.
WARNING
NEVER ATTEMPT TO DISMANTLE ANY PART OF
THE COUNTERBALANCE ASSEMBLY (CYLIN-
DERS, RODS, OR BRACKETS) UNTIL ALL PRES-
SURE WITHIN THE CYLINDERS HAS BEEN
COMPLETELY DISCHARGED.
6. Remove the two (2) 1.00” - 8 Hex. Nuts that secure
the counterbalance plate to the counterbalance
rods. Remove the counterbalance plate. (See Fig-
ure 6E.)
7. While an assistant holds the counterbalance pis-
ton rod from above, remove the .187” x 2.00” long
cotter pins from the air cylinder head pins.
Remove the air cylinder head pins, and lift the
counterbalance cylinder from the press. Move the
cylinder to a clean area for further disassembly.
8. Remove four (4) .375”- 16 Hex. Nuts that secure
the air cylinder cover to the cylinder. Remove the
air cylinder cover.
9. Remove piston and rod assembly by pulling it out
through the top of the cylinder.
10. Remove bushing from the air cylinder cover and
inspect for scoring. If bushing is scored, replace
with a new one. Cross-drilled hole must be drilled
after new bushing is in place in cylinder head.
11. Remove the cylinder air cylinder head. Inspect
cylinder for scoring. If cylinder is scored, ream
cylinder.
12. Remove the .750” - 10 x 1.00” long Hex. Head Cap
Screw and flat washer which secures the piston,
seal, and piston plate to the piston rod.
13. Remove seal from piston and discard.
14. Apply a liberal coat of grease lubricant to the new
seal and install on piston.
15. Apply a liberal coat of grease lubricant to inside of
cylinder.
16. Apply a liberal coat of grease lubricant to the cylin-
der rod. Then carefully insert rod and piston
assembly through bottom of cylinder, being care-
ful not to damage seal in piston.
17. Clean the mating surfaces of the air cylinder head
and the air cylinder to remove any RTV Sealant
adhering to the mating surfaces. Apply a new coat-
ing of RTV Sealant to the air cylinder head mating
surface and install the cylinder on the air cylinder
head. Wipe away any excess sealant.
18. Reinstall the air cylinder cover on cylinder and
secure with four (4) .375”- 16 Hex. Nuts. Apply
Loctite Adhesive Grade 242 (Blue Liquid) to the
threads of the studs, install the nuts, and torque
them to the value shown in the chart on page C-3.
19. With the aid of an assistant, lower the counterbal-
ance cylinder into place. Secure the counterbal-
ance cylinder to the press frame with two (2) air
cylinder head pins. Secure each pin with a .187” x
2.00” long cotter pin.
20. Place the counterbalance plate over the two (2)
counterbalance rods and the counterbalance pis-
ton rod. Secure the counterbalance plate to the
counterbalance rods with two (2) 1.00” - 8 Hex.
Nuts and torque the nuts to the value shown in the
chart on page C-3.
21. Reconnect the air supply lines that feed, and are
directly attached to, each cylinder unit. Apply Loc-
tite Hydraulic Sealant (H/S) No. 569 (Brown Liq-
uid) to the threads of the fittings.
FLYWHEEL BRAKE
(Ref. Figure 8E)
The function of the flywheel brake is to quickly stop the
flywheel from free-wheeling after the main drive motor
is turned OFF. As an option, additional control compo-
nents can be included that will allow the brake to be
applied, thereby slowing the flywheel, whenever press
speed is reduced — a condition that occurs regularly
when the operating mode of the press is changed from
CONTINUOUS to INCH.
NOTE: The flywheel brake is not a primary brake and
should not be confused with the pneumatically
released/spring applied brake portion of the
clutch/brake unit used to stop slide motion.
The flywheel brake consists of a brake anchor plate
and a cylinder housing that contains an air-actuated
piston. The brake anchor plate is bolted on the upper
right-hand side of the press on flywheel presses, and to
middle left-hand side of the press on geared presses.
(See Figure 8E.) Brake friction material, attached to the
piston, contacts the flywheel when air pressure is
applied to the cylinder. Air pressure is supplied to the
brake through a solenoid air valve. A pressure switch in
the pneumatic circuit of the brake prevents starting of
the main drive motor until air pressure is released from
the cylinder.
E - 10
!
Summary of Contents for IOI
Page 1: ...Manual No 1010C MINSTER 8952 399 15 00 Service Manual OBI OBS SERIES PRESS MODEL...
Page 2: ...Manual No 1010C MINSTER 8952 399 15 00 Service Manual OBI OBS SERIES PRESS MODEL...
Page 9: ......
Page 25: ......
Page 51: ......
Page 63: ......
Page 90: ...ADDITIONAL COMMENTS I 13...