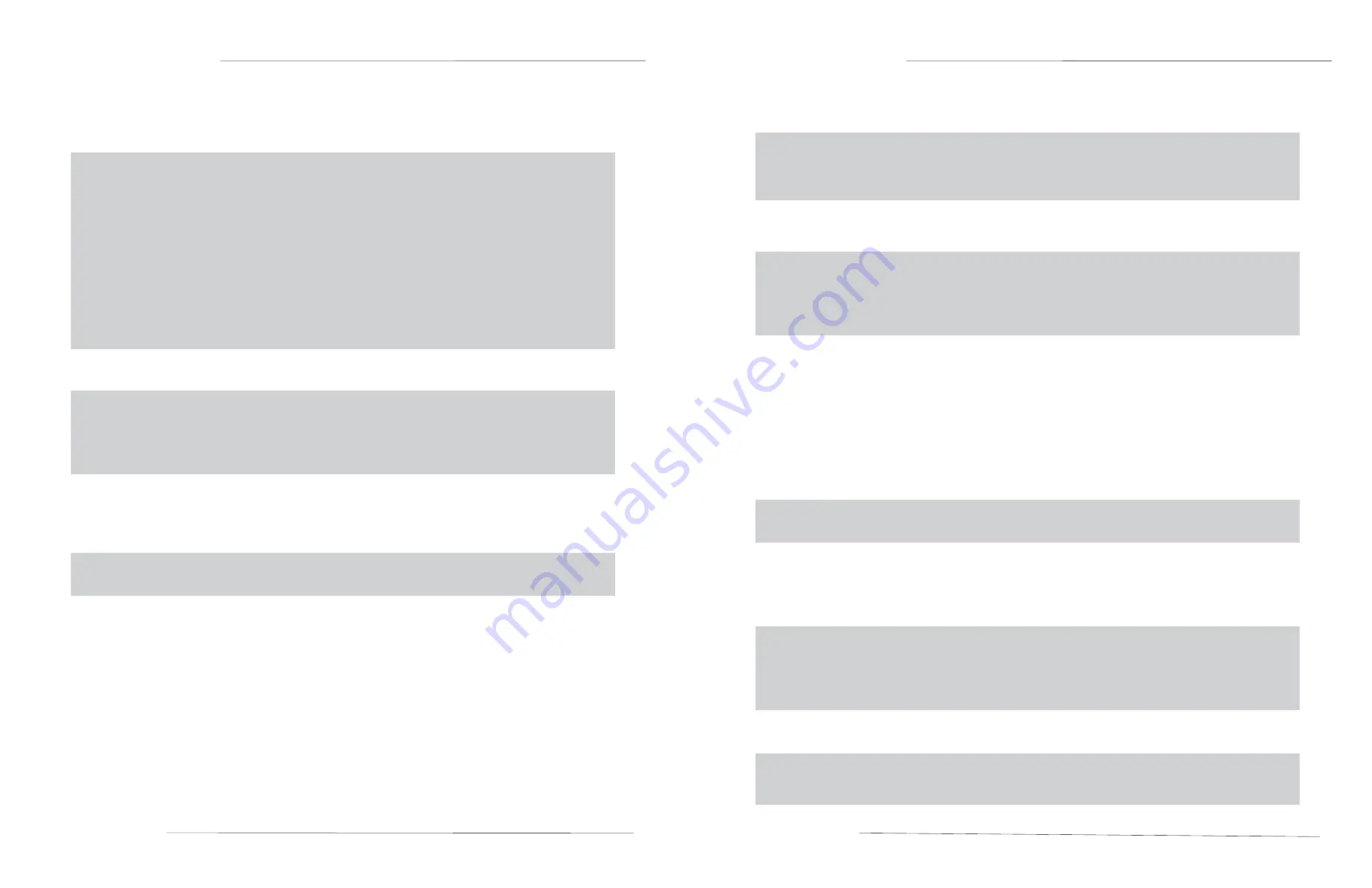
Dowel Drill
Manual
14
15
Dowel Drill
Manual
Troubleshooting
Air Drill
Cause
Remedy
DRILL NOT GETTING AIR
1. On Multi Drill units, switch airline with drill
that is working properly. If drill now runs
check the air control valve. If the valve works,
check the drill.
2. Check clave on air compressor and drill unit
to be certain they are completely open
3. Check compressor. It should have 100SCFM
(47.20m^3/sec.) per drill and 110PSI (7.6 BAR)
at drill manifold when drilling with large drills.
4. Make certain all fittings are connected prop-
erly and not leaking.
COUPLING OR HOSE OBSTRUCTION Remove Obstruction
FAILURE IN THE ELECTRICAL CIRCUIT Check switches, connections, coils, ground &
voltage. If the power unit (backhoes, grader,
ETC.) is being jump started, check the AMPS &
voltage being jump supplied to coils from the
battery, it may be too low.
FAILURE OF DRILL SOLENOID VALUE
(MULTI DRILL UNITS WITH REMOTE
ELECTRICAL CONTROLS)
Check valve - you should be able to feel the so-
lenoid move when it is actuated. Make sure you
have current to the solenoid coil. Replace the
dolenoid if there is no movement.
MECHANICAL FAILURE OF DRILL
Disassemble the drill & inspect for damaged
parts.
PROBLEM:
DRILL DOES NOT RUN
Troubleshooting
Air Drill
Cause
Remedy
NOT ENOUGH AIR REACHING
DRILL. IT SHOULD HAVE 100SCFM
(47.2DM^3/
sec
.
) PER DRILL AND 110
PSI (7.6
bar
)
On Multi Drill units. Turn off one or two drills. If
the remaining drills pick up speed, check the air
compressor.
RESTRICTION IN AIR LINE
A foreign object in the air line or possibly a
reduction in the air line caused by a reducer
fitting.
TOO SMALL AIR LINE
Following are supply line sizes for drilling:
A-1 Single Drill 3/4” (19mm)
A-2 Two Drills 1-1/4” (38.75mm)
A-3& A-4 Three & four drills 1-1/2” (38.1mm)
A-5 Five Drills 2” (50.8mm)
AIR PRESSURE TO CYLINDER “FEED-
ING” DRILL INTO CONCRETE NOT
ADJUSTED PROPERLY
Excessive pressure can cause drill to “bind up”
in the hole. Pressure that is too low will not
“feed” the drill into the concrete. The air pres-
sure required varies with the drill model.
Horizontal- all units with large drills use 22-26
PSI (1.5-1.8 bar). Drill units using the 15LB (6.8kg)
class drill will use 16-20 PSI (1.1-1.4 Bar).
Vertical - all drill units use 5-6 PSI (0.34-0.41
Bar). With the correct air pressure, the drill steel
should have a slight rattle.
INSUFFICIENT AIR FLOW TO KEEP
HOLE BLOWN CLEAN
Check for obstruction in the blow tube in the
drill.
LUBRICATOR PUTTING OUT TOO
MUCH OIL TO DRILL
If you notice more than a light film of oil on the
air deflector on the bottom of the drill adjust the
lubricator, make certain you are using the type of
oil called for in the operation and maintenance
manual.
MECHANICAL BLINDING OF DRILL
CARRIER
Make sure the eight bearing pads are adjusted
correctly. The square tube that the drill carrier
slides on must be free of rust so that the carrier
slides freely, drill steel must not be binding in
the guide bearing.
BENT DRILL STEEL, WORN DRILL BIT
OR DRILLING INTO REBAR
Replace the drill steel or bit. If drilling into rebar,
move the drill.
USING 3 1/4” (8.25
cm
)
SHANK DRILL
STEEL IN 4 1/4”
(10.8
cm
)
SHANK
CHUCK DRILL
The drill steel will rotate but it will not allow the
drill piston to hammer properly, replace it with
the correct 4 1/4” (10.8cm) drill steel.
PROBLEM:
DRILL RUNS SLOW OR DOES NOT DRILL EFFECTIVELY