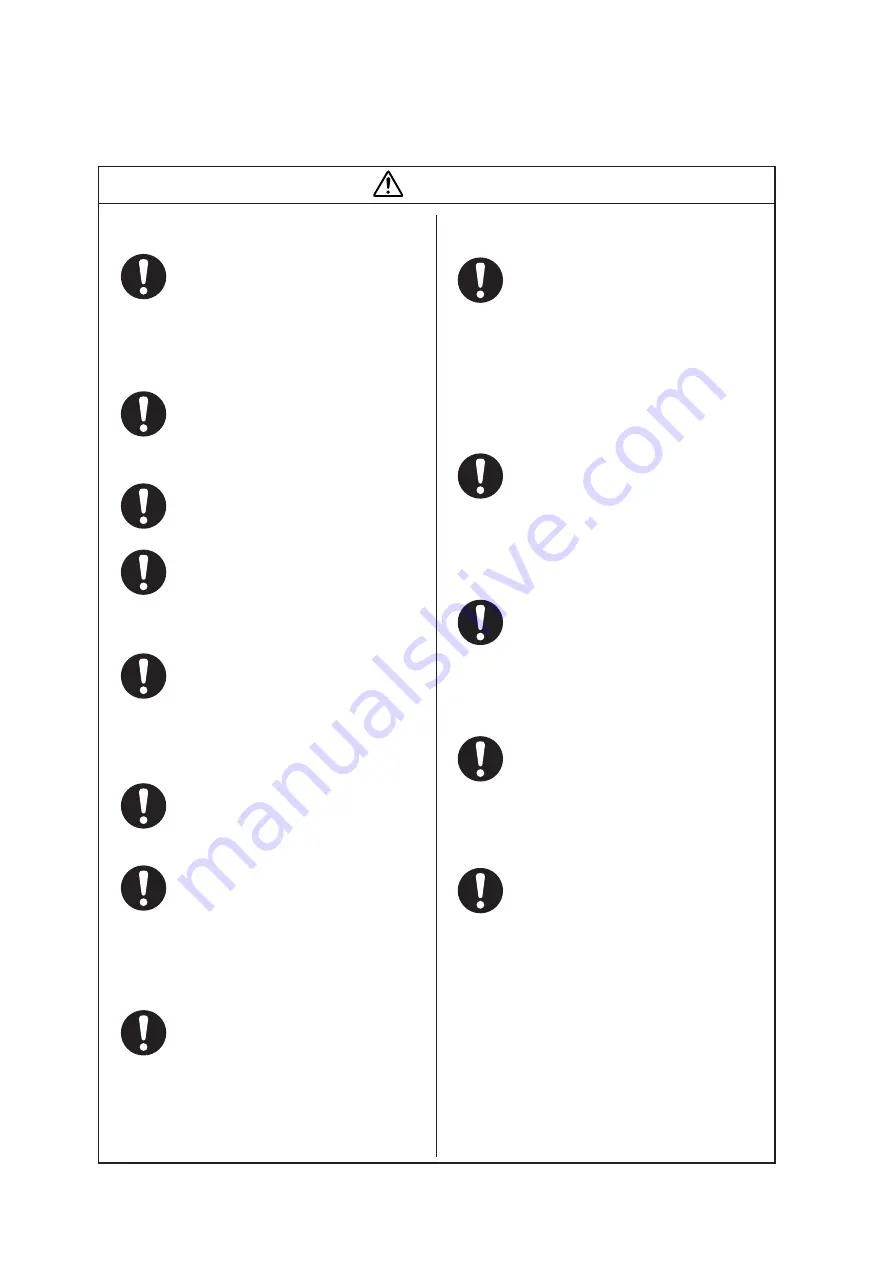
- vi -
PRECAUTIONS IN USE
CAUTION
Locking the adjuster foot
•
Be sure to lock the adjuster foot
before starting printing. If the
device performs printing without
the casters locked, the device can
move out of position.
Front cover and lever
•
Never open the front cover and/or
lever during printing. Opening the
cover or lever will abort printing.
Protection against dust
•
It is strongly recommended to use
the device in a room that is not
dusty.
•
Keep the front cover held closed
also when the device is not
engaged in printing. If not, dust
can accumulate on the head
nozzle.
•
When leaving the workshop after
the working hours, be sure to
remove any medium from the roll
hanger. If any medium is left on
the roll hanger, dust can gather
on it.
•
Store medium in a bag. Wiping off
dust accumulated on a medium
will adversely affect the medium
due to static electricity.
•
Frequently wipe the capping
station clean to eliminate dust
and paper chips. Wiping with a
fluffy wiper only rubs dust over
the capping station. Replace the
fluffy wiper immediately with a
new one.
•
Dust in the head will also cause
drops of ink to fall abruptly down
on the medium during printing. If
this phenomenon takes place, be
sure to clean up the head. (See
“Chapter 4 Maintenance functions.”)
Periodic exchange parts
•
There are some parts which
must be replaced by service
men after JV4 series are in use
for 5000 hours from 3000 hours.
Therefore, we would like to
suggest that you make a
contract with distributors or
dealers for after-sale service.
Medium
•
Use specific cloth designated
medium exclusive to JV4 series.
Mimaki assumes no
responsibility for any damage
caused by the use of any
medium other than the
aforementioned one.
•
If medium that is likely to tightly
curl, flatten first the paper
before using it for printing.
Heavily-curled medium affect
the plotted picture quality.
Locking the casters
•
Be sure to lock the casters
before starting plotting. If the
device performs plotting without
the casters locked, the device
can move out of position.
Warning labels
•
This device is adhered with a
warning label at two locations.
Be sure to fully understand the
warnings given on the labels. In
the case where any of the
warning label has become so
soiled that the warning message
is illegible or has come off,
purchase a new one from your
local distributor or our office.
Refer to Appendix for the label
adhering locations.
Summary of Contents for JV4 Series
Page 2: ......
Page 149: ......
Page 150: ...D200571 2 60 16022006...
Page 151: ......
Page 152: ...PrintedinJapan MIMAKI ENGINEERING Co Ltd 2006...