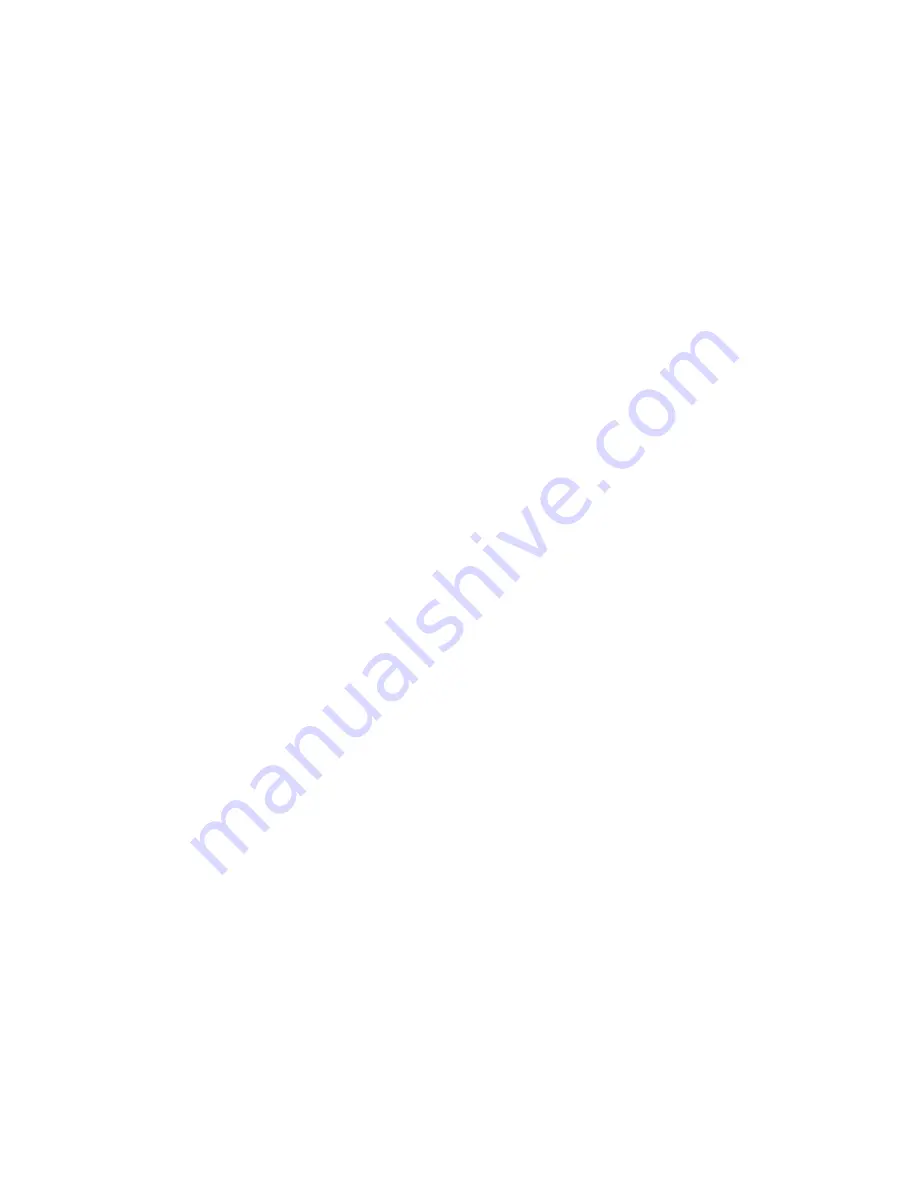
OM-236 891 Page 52
.
During the software update, the displays on both the power source and feeder front panels may display H99 or H98 as well as the UPd or go blank
for a period of time. This is normal during a software update. Do not remove the memory card until the software update has completed. Do not
turn off the power source until the software update has completed.
d.
Remove memory card.
E. Memory Locations
1.
Memory Location Buttons 1-4
These are locations for storing weld process settings for easy access. Press and release these buttons to recall stored unit configuration settings. Only
one memory location can be active during unit operation. The number next to the button illuminates to indicate the active memory location. Unit configu-
ration settings are automatically saved to the active memory location one second after any change is made to any of the front panel controls. This
feature allows the unit to remember an operator’s preferred settings. These settings can be recalled at any time by selecting the appropriate memory
location and process/feeder side. By selecting a process such as STICK, TIG, MIG LEFT side of feeder, or MIG RIGHT side of feeder there will be four
Memory Locations available for each, providing a total of 16 Memory Locations for a dual feeder. There will only be 12 Memory Locations available for a
single feeder.
2.
Memory Location Reset
Pressing and holding a memory location button for more than two seconds will restore factory default settings for the current weld process to that
particular memory location. The memory location number light will go out and back on when the reset is complete.
F. Stick And TIG Welding Process Controls
1.
Stick Process Select Button
Press and release this button to activate the stick welding process controls. The STICK text below the button illuminates as well as the active stick
electrode type text and the swoosh above the amperage adjust knob. The operator must select the desired stick electrode type and adjust the
amperage knob to the appropriate setting within a range from 40 to 400 amps.
2.
Stick Electrode Type Select Button
Press and release this button to select the desired stick electrode type (EXX10 or EXX18). The text above or below the button will illuminate for the
active electrode type. This button is only active with the stick welding process selection and only then will text for the electrode type selection illuminate.
3.
Adjustable DIG And Hot Start
Adjustable DIG and Hot Start features are provided when in the STICK process. Setting for both DIG and Hot Start on EXX10 and EXX18 electrode are
independent (each has their own settings). To access the adjustable DIG and adjustable Hot Start functions, proceed as follows:
a.
When in the STICK mode, press and hold the STICK button for two seconds. The Amperage display will show the DIG setting with the right
most decimal point illuminated. The default value for DIG is 40.
b.
Rotate the Amperage knob to adjust the DIG setting. Adjustable range is 0 to 99.
c.
When in the adjustable DIG function, press the STICK button to access the adjustable Hot Start function. The Amperage display will show the
Hot Start setting with the middle decimal point illuminated. The default setting is 1.3.
d.
Rotate the Amperage knob to adjust the Hot Start setting. Adjustable range is 0.0 to 2.0.
e.
Press the STICK button or any other button on the interface to exit the adjustable DIG and adjustable Hot Start function.
4.
Ammeter Display
The display illuminates and shows amperage setting when either a stick or TIG welding process is selected. Dashes are displayed when any MIG
welding process is selected indicating the display is inactive; however, actual amperage is displayed while welding regardless of the selected welding
process. Measured amperage just prior to the end of a welding operation will appear on the display for 10 seconds after the welding operation.
5.
Amperage Adjust Knob
Use this knob to set a desired amperage setting for either a stick or TIG welding process. Rotating the knob clockwise increases amperage and count-
er-clockwise decreases amperage. Amperage adjustment is active when the swoosh above the knob is illuminated. If a remote control is connected to
the Remote 14 receptacle, the unit will automatically adjust output control to a primary/secondary configuration. In this configuration, the Amperage
Adjust knob on the unit becomes the primary and sets the maximum amperage output of the unit. The remote control becomes the secondary and
provides an amperage range of 0 to 100% based on the Amperage Adjust knob setting.
.
The Remote 14 receptacle is factory set to be active in TIG mode only. As an option, this receptacle may also be enabled in Stick mode (see Section
5-3).
6.
TIG Process Select Button
Press and release this button to activate the TIG welding process controls. The TIG text below the button illuminates as well as the active starting
method text and the swoosh above the amperage adjust knob. The operator must select the desired starting method and adjust the amperage knob to
the appropriate setting within a range from 10 to 350 amps. If the TIG process has been selected and a remote current/contactor control is connected,
holding the TIG process select button for more than two seconds will display the effective amperage command (based on the amperage setting and the
remote current/contactor control setting).
7.
TIG Starting Method Select Button
Press and release this button to select the desired TIG starting method either HF or Lift Arc. The text above or below the button will illuminate for the
active starting method. This button is only active with the TIG welding process selection and only then will text for the starting method selection
illuminate.