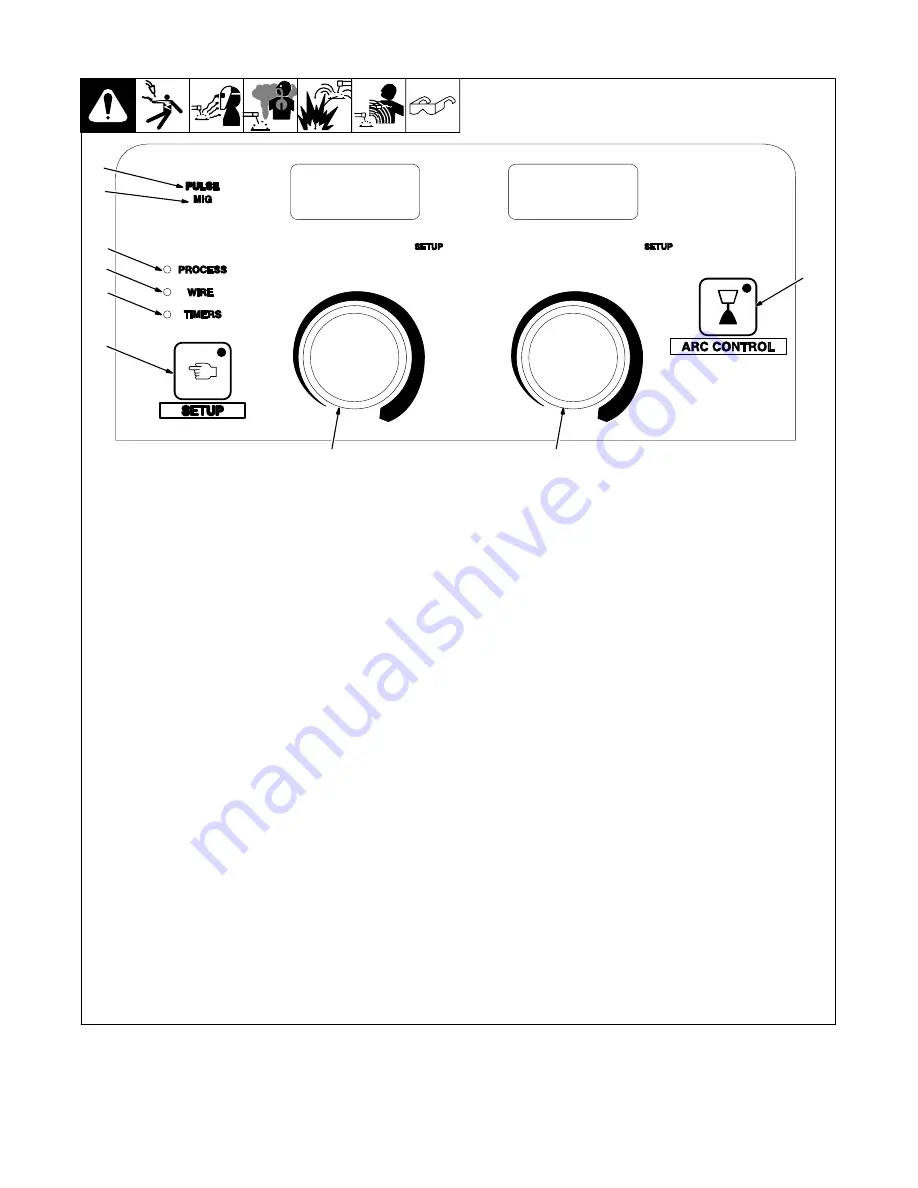
.
A complete Parts List is available at www.MillerWelds.com
OM-1327 Page 32
5-3. Timers
To enter the
TIMERS
(5) menu depress the
SETUP
(6) button 4 times or until the
TIMERS
light (5) is illuminated.
Items that can be adjusted in this menu are:
Run-in speed
(
R‐IN
)
−
The speed of the
wire prior to the welding arc being struck.
This setting is a percentage of the Wire
Feed Speed the unit is set to for welding.
Programming value ranges from 25-150.
Preflow
(
PRE
)
−
The amount of time that the
shielding gas will flow after the trigger is
depressed and before the welding arc will
be allowed to be active. Range of setting is
from 0-5 seconds.
Postflow
(
POST
)
−
The amount of time that
the shielding gas will flow after the arc has
been shut off. Range of setting is 0-10
seconds.
Spot Timer
(
SPOT
)
−
The amount of time
that the arc will be active before it shuts off
automatically. Range of setting is from
0-120 seconds. Spot timer is reset upon re-
lease of welding gun trigger.
Display
(
DISP
)
−
Allows the Wire Speed
display to show actual welding amperage
while arc is active and for 5 seconds after
arc is shut off. Setting is either
AMPS
or
WFS
for standard Wire Feed Speed.
Once in the
TIMERS
(5) menu, rotate the
left knob (8) to find a particular item, and ro-
tate the right knob (9) to change setting or
status.
Depress
SETUP
(6) button to get out of
TIMERS
(5) menu and to enter welding
mode.
Ref. 213 935-A
1
9
8
2
3
4
5
6
7
Summary of Contents for Millermatic 350
Page 14: ...OM 1327 Page 10 ...
Page 51: ...OM 1327 Page 47 Notes ...
Page 53: ...OM 1327 Page 49 246 030 A ...