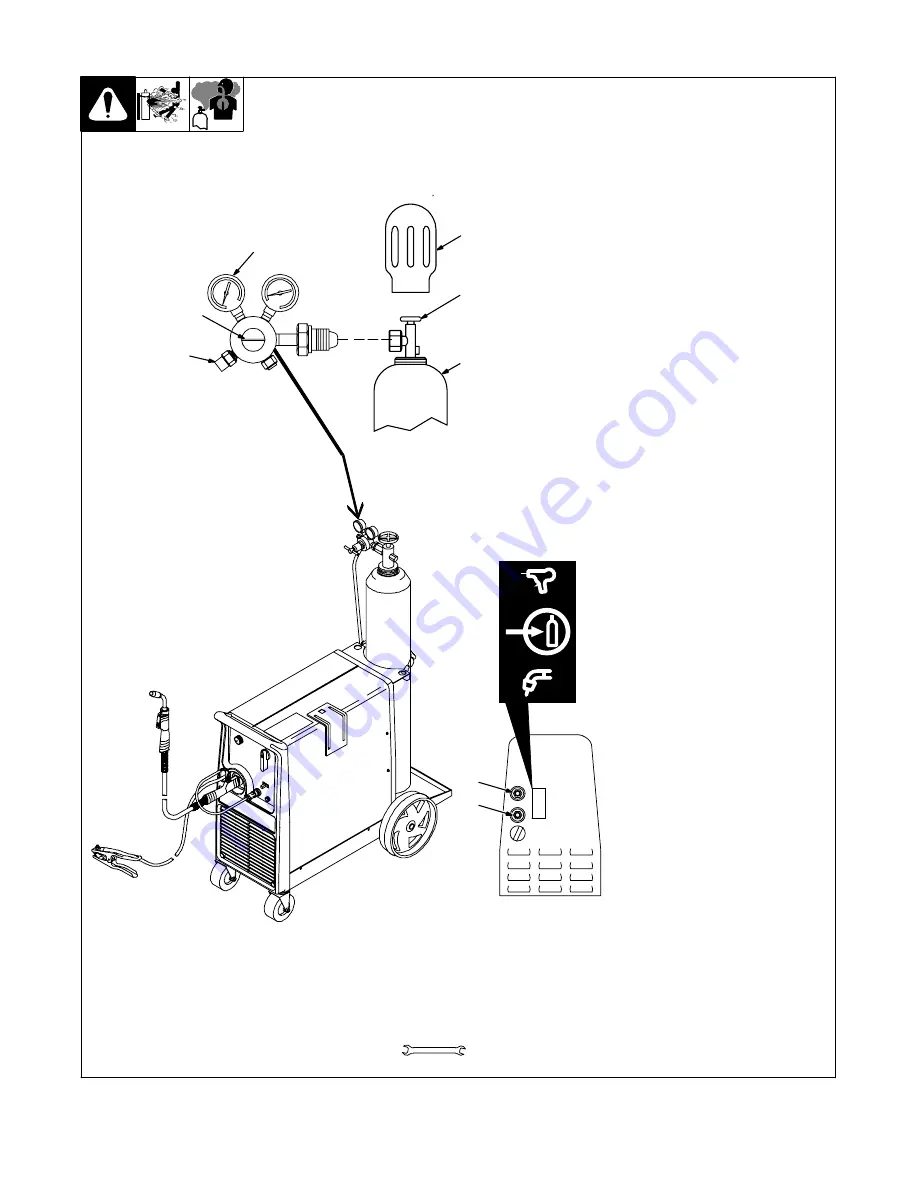
OM-1325 Page 14
4-10. Installing Gas Supply
802 028-A / Ref. 802 991-B
Tools Needed:
Obtain gas cylinders and chain to
running gear, wall, or other
stationary support so cylinders
cannot fall and break off valve.
1
Cap
2
Cylinder Valve
Remove cap, stand to side of
valve, and open valve slightly. Gas
flow blows dust and dirt from valve.
Close valve.
3
Cylinder
4
Regulator/Flowmeter
Install so face is vertical.
5
Regulator/Flowmeter Gas
Hose Connection
6
Welding Power Source Gas
Hose Connection For Spool
Gun
7
Welding Power Source Gas
Hose Connection For MIG
Gun
Connect gas hose between
regulator/flowmeter gas hose con-
nection, and fitting on rear of
welding power source.
8
Gas Flow Adjustment Control
Typical flow rate is 25 cfh (cubic
feet per hour). Check wire
manufacturer’s recommended
flow rate.
1-1/8, 5/8 in
4
5
1
2
3
8
Rear
Panel
Argon Gas Or
Mixed Gas
6
7
.
DO NOT use Argon/Mixed gas regulator/flowmeter
with CO
2
shielding gas. See Parts List for optional
CO
2
gas regulator/flowmeter.
210 022-A
Summary of Contents for Millermatic 210
Page 25: ...OM 1325 Page 21 Notes...
Page 27: ...OM 1325 Page 23 204 890...
Page 45: ...OM 1325 Page 41 Notes...
Page 56: ...Notes...
Page 57: ...Notes...
Page 58: ...Notes...