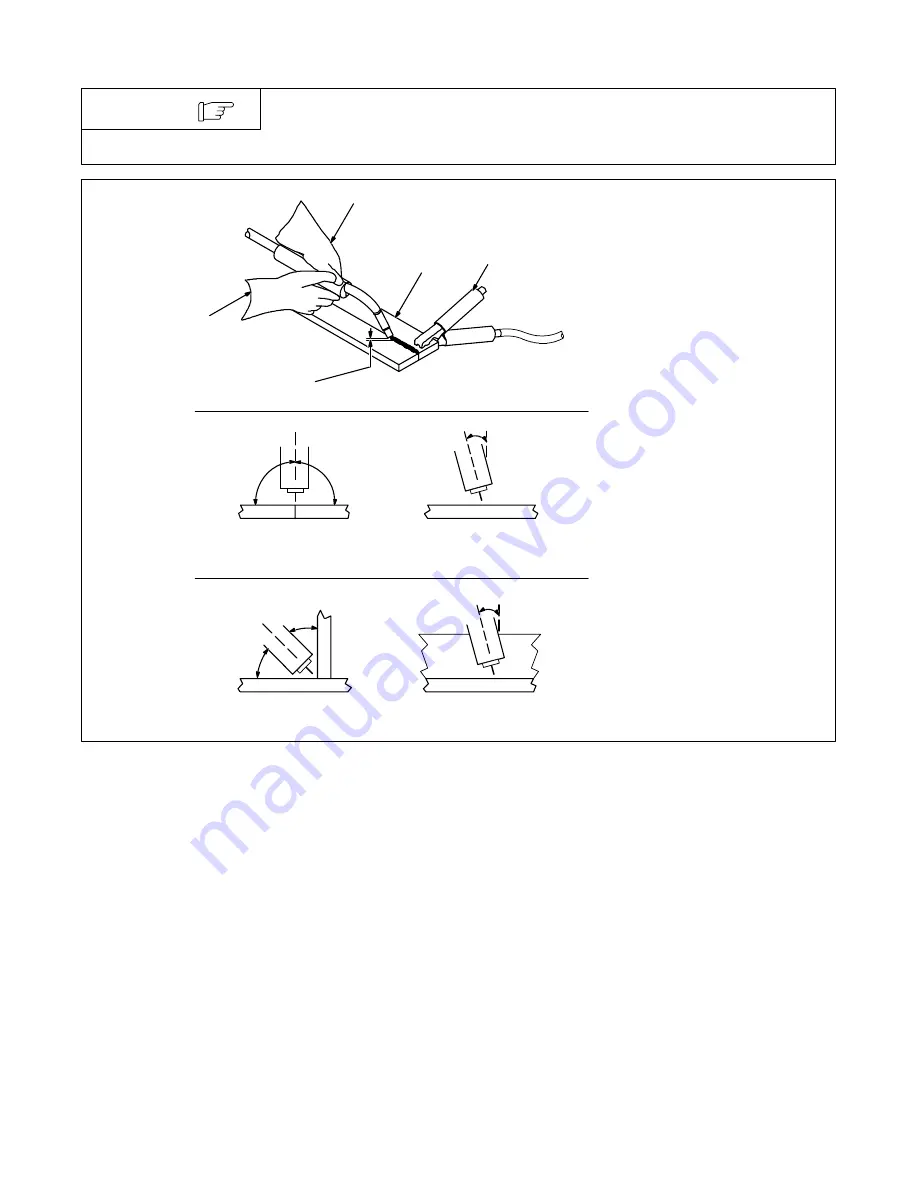
OM-187 926 Page 23
7-3. Holding And Positioning Welding Gun
Welding wire is energized when gun trigger is pressed. Before lowering helmet and
pressing trigger, be sure wire is no more than 1/2 in (13 mm) past end of nozzle,
and tip of wire is positioned correctly on seam.
NOTE
1
Hold Gun and Control Gun
Trigger
2
Workpiece
3
Work Clamp
4
Electrode Extension (Stickout)
1/4 to 1/2 in (6 To 13 mm)
5
Cradle Gun and Rest Hand on
Workpiece
2
3
5
4
90
°
90
°
0
°
-15
°
45
°
45
°
GROOVE WELDS
FILLET WELDS
End View Of Work Angle
Side View Of Gun Angle
End View Of Work Angle
Side View Of Gun Angle
1
0
°
-15
°
S-0421-A