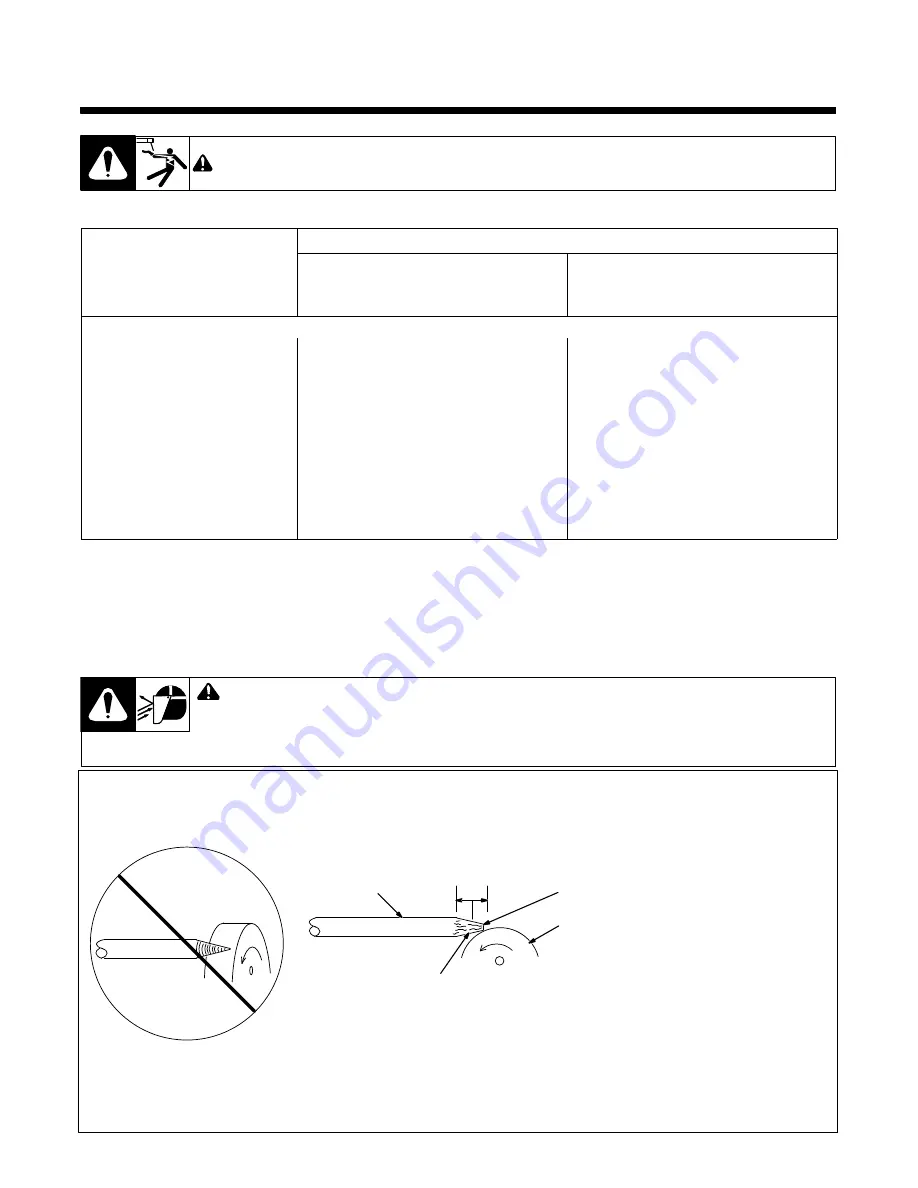
OM-216 869 Page 95
SECTION 11
−
SELECTING AND PREPARING A TUNGSTEN
FOR DC OR AC WELDING WITH INVERTER MACHINES
gtaw_Inverter_2010-04
Whenever possible and practical, use DC weld output instead of AC weld output.
11-1. Selecting Tungsten Electrode (
Wear Clean gloves To Prevent Contamination Of Tungsten
)
Amperage Range - Gas Type
- Polarity
Electrode Diameter
(DCEN)
−
Argon
Direct Current Electrode Negative
(For Use With Mild Or Stainless Steel)
AC
−
Argon
Balance Control @ 65% Electrode Negative
(For Use With Aluminum)
2% Ceria (Orange Band), 1.5% Lanthanum (Gray Band), Or 2% Thorium (Red Band) Alloy Tungstens
.010 in. (1 mm)
Up to 25
Up to 20
.020 in. (1 mm)
15-40
15-35
.040 in. (1 mm)
25-85
20-80
1/16 in. (1.6 mm)
50-160
50-150
3/32 in. (2.4 mm)
130-250
135-235
1/8 in. (3.2 mm)
250-400
225-360
5/32 in. (4.0 mm)
400-500
300-450
3/16 in (4.8 mm)
500-750
400-500
1/4 in. (6.4 mm)
750-1000
600-800
Typical argon shielding gas flow rates are 11 to 35 cfh (cubic feet per hour).
Figures listed are a guide and are a composite of recommendations from American Welding Society (AWS) and electrode manufacturers.
11-2. Preparing Tungsten Electrode For DC Electrode Negative (DCEN) Welding Or AC
Welding With Inverter Machines
Grinding the tungsten electrode produces dust and flying sparks which can cause injury and start fires.
Use local exhaust (forced ventilation) at the grinder or wear an approved respirator. Read MSDS for safety
information. Consider using tungsten containing ceria, lanthana, or yttria instead of thoria. Grinding dust
from thoriated electrodes contains low-level radioactive material. Properly dispose of grinder dust in an
environmentally safe way. Wear proper face, hand, and body protection. Keep flammables away.
Ideal Tungsten Preparation
−
Stable Arc
2-1/2 Times
Electrode Diameter
1
Grinding Wheel
Grind end of tungsten on fine grit, hard
abrasive wheel before welding. Do not use
wheel for other jobs or tungsten can become
contaminated causing lower weld quality.
2
Tungsten Electrode
A 2% ceriated tungsten is recommended.
3
Flat
Diameter of this flat determines amperage
capacity.
4
Straight Ground
Grind lengthwise,
not radial
.
1
3
4
Causes Wandering Arc
2
Wrong Tungsten
Radial Grinding
Preparation
Summary of Contents for DYNASTY 350
Page 6: ......
Page 16: ...OM 216 869 Page 10...
Page 26: ...OM 216 869 Page 20 Notes...
Page 85: ...OM 216 869 Page 79 243 217 C...
Page 86: ...OM 216 869 Page 80 Figure 8 2 Circuit Diagram For Maxstar 350 Models...
Page 87: ...OM 216 869 Page 81 243 215 C...
Page 88: ...OM 216 869 Page 82 Figure 8 3 Circuit Diagram For Dynasty 700 Models Part 1 of 2...
Page 89: ...OM 216 869 Page 83 243 218 C...
Page 90: ...OM 216 869 Page 84 Figure 8 4 Circuit Diagram For Dynasty 700 Models Part 2 of 2...
Page 91: ...OM 216 869 Page 85 243 218 C...
Page 92: ...OM 216 869 Page 86 Figure 8 5 Circuit Diagram For Maxstar 700 Models Part 1 of 2...
Page 93: ...OM 216 869 Page 87 243 216 C...
Page 94: ...OM 216 869 Page 88 Figure 8 6 Circuit Diagram For Maxstar 700 Models Part 2 of 2...
Page 95: ...OM 216 869 Page 89 243 216 C...
Page 96: ...OM 216 869 Page 90 228 525 B Figure 8 7 Circuit Diagram For Cooler...