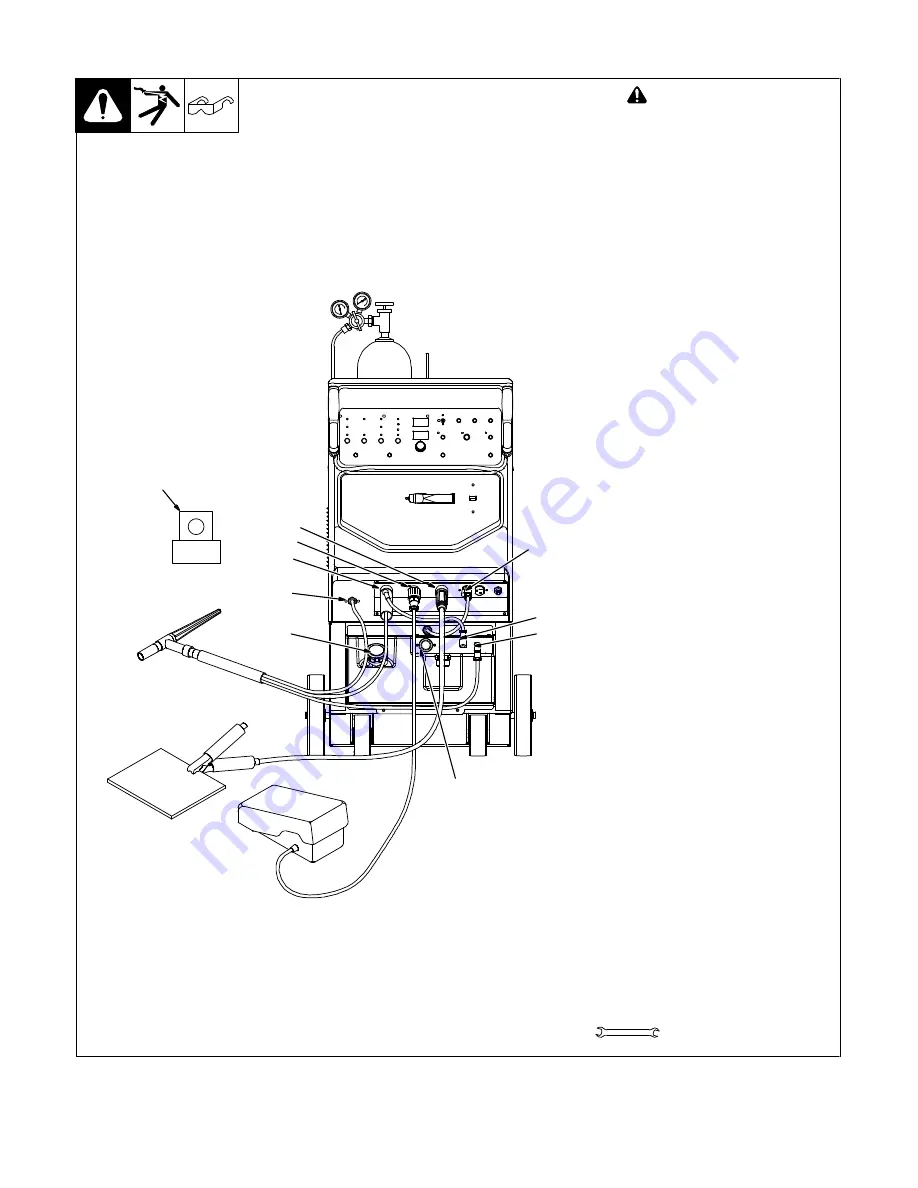
OM-230 161 Page 8
6-2. Optional Cooler Connections
805 102-B
Tools Needed:
11/16 in. (21 mm for CE units)
!
Disconnect cooler plug from
welding power source re-
ceptacle before filling.
1
Cap
Remove cap and fill tank with three
gallons of coolant (see Section
4-3).
2
Gas Out Connection
Connect TIG torch gas hose to gas
out fitting.
3
Electrode Weld Output
Terminal
4
TIG Block (Customer Sup-
plied)
Connect TIG torch to electrode
weld output terminal. Note: Some
models may require a TIG block
instead of the international style
water connector.
5
Remote 14 Receptacle
Connect remote control to recep-
tacle if desired.
6
Work Weld Output Terminal
Connect work lead to work weld
output terminal.
7
Water-In (From Torch)
Connection
Connect torch water-out (red) hose
to welding power source water-in
connection.
NOTICE
−
If welding power source
has a water valve, do not connect
hoses to water valve.
8
Water-Out (To Torch)
Connection
Connect torch water-in (blue) hose
to welding power source water-out
connection.
Operation:
9
115 VAC Cord
10 Flowmeter
To turn cooling unit On, connect
power cord to welding power
source 115 volts AC receptacle.
Unplug to turn unit Off.
Flow indicator spins to indicate that
at least 1.1 qt/min (1.0 L/min) of
coolant is flowing.
1
3
5
6
7
2
8
9
4
10
Summary of Contents for Cool Runner 3CS OM-230 161 F
Page 4: ......
Page 18: ...TM 216 869 Page 14 Dynasty 350 700 Maxstar 350 700 Notes...