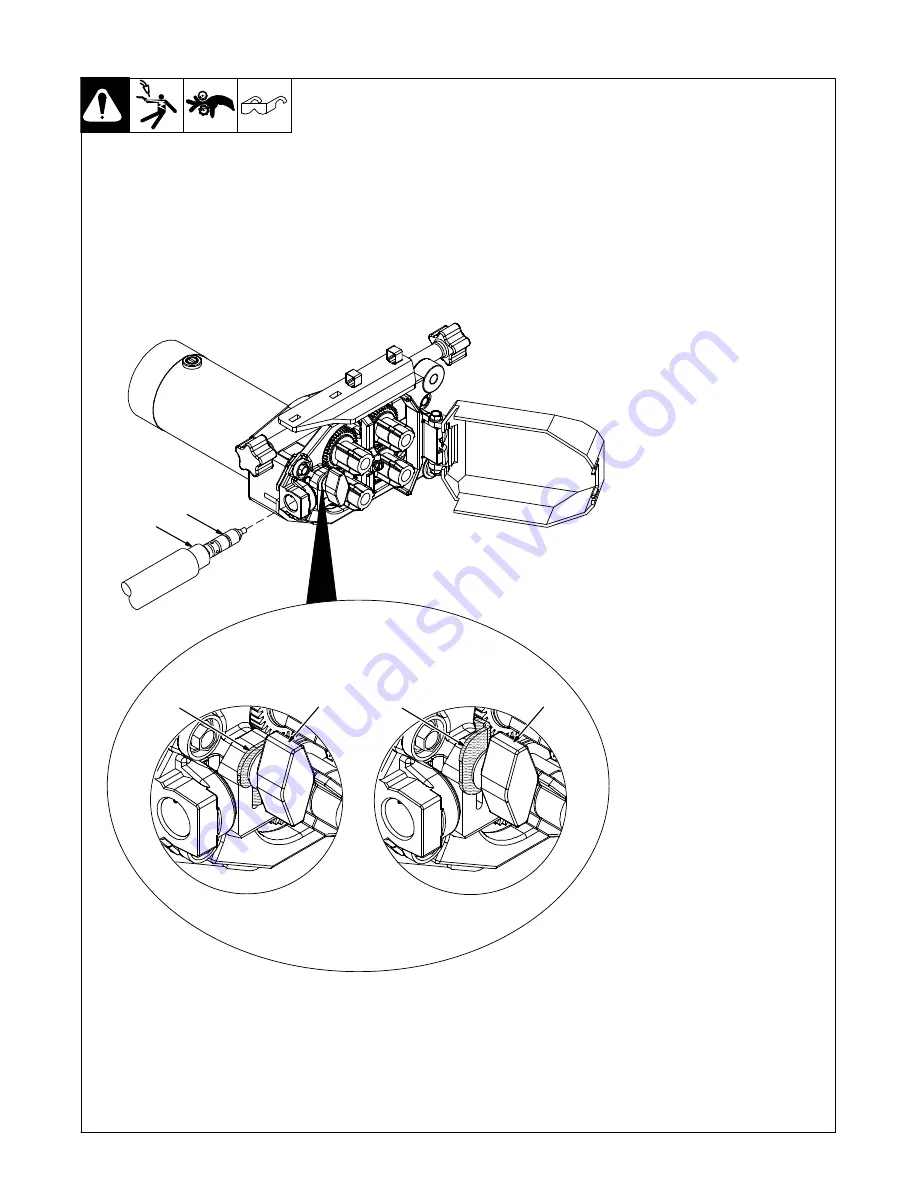
OM-248965 Page 16
5-5. Installing Welding Gun
Ref. 249 398-A
1
Gun Locking Tab
2
Power Clamp Knob
3
Gun Connection End
4
Power Pin Groove
Installing gun with Accu-Mate
connection
Loosen power clamp knob to allow
power pin of gun to clear the gun
locking tab.
Push power pin into power clamp
as far as possible to align the
groove in the power pin of the gun
with the gun locking tab.
Secure gun by tightening power
clamp knob.
Installing gun without Accu-
Mate
connection
When using a gun without the
groove in the power pin, loosen
power clamp knob and rotate gun
locking tab 180 degrees. This pre-
vents the locking tab from extend-
ing into the power pin gun connec-
tion.
Push power pin into power clamp
as far as possible.
Secure gun by tightening power
clamp knob.
4
Installing gun with
Accu-Mate connection
Installing gun without
Accu-Mate connection
3
2
2
1
1
Summary of Contents for Axcess E Dual
Page 4: ......
Page 13: ...OM 248965 Page 9 Notes...
Page 54: ...OM 248965 Page 50 SECTION 10 ELECTRICAL DIAGRAM Figure 10 1 Circuit Diagram...
Page 55: ...OM 248965 Page 51 218 564 F...