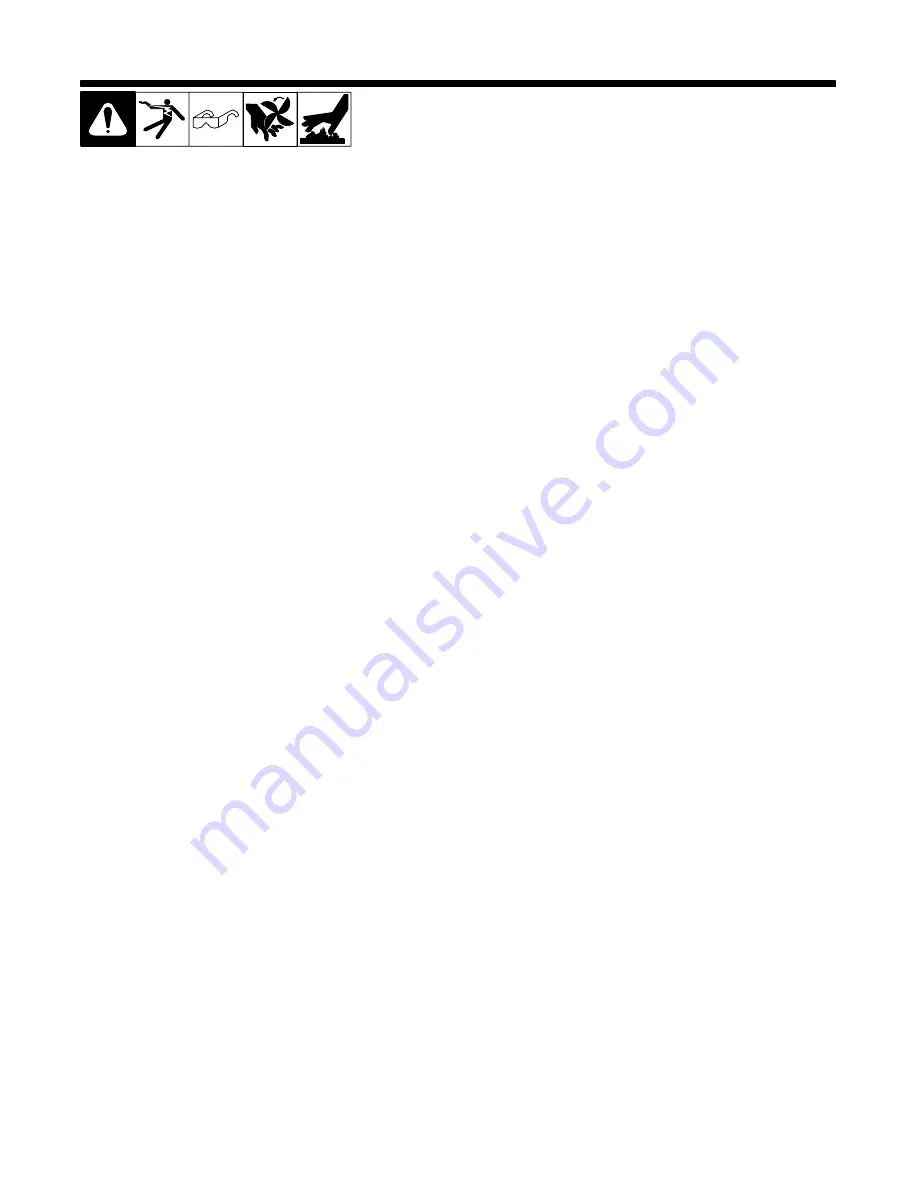
Page 5
SECTION 2
−
ARC STUD WELDING (SW) GUIDELINES
2-1.
Process Description
Arc stud welding (SW) is a welding process in which a metal fastener (weld stud) is joined to a workpiece. This process
is generally referred to as stud welding. The metal fastener is joined under pressure once sufficiently heated with an
electric arc.
The fastener or weld stud is positioned for welding through the use of a stud gun. When the operator activates the stud
gun trigger, the fastener (electrode) is welded to the workpiece without the use of filler metal. The welding duration of
SW is typically one second or less.
One end of a SW fastener is prepared for welding. A ceramic ferrule surrounding the weld end of the fastener provides
partial shielding of the weld. The ferrule also dams the molten metal to form a fillet type weld. Shielding gases or flux
may or may not be used to protect the weld.
2-2. Typical Uses Of The Arc Stud Welding Process
The arc stud welding process lends itself to a wide range of applications such as automotive, ship building, appliance,
aero-dynamics, boilers, light or heavy construction, preassembled fabrication designs and fit-up parts design.
The process may be utilized on a range of material thickness from about .060 in to several inches.
The stud welding process is advantageous for the following reasons:
D
Major design specifications may be readily adapted to the process, such as material types, metallurgical aspects,
special thread designs, fit-up tolerances, etc.
D
Capable of producing a full cross section weldment with a minimum of base metal distortion or surface disruption.
D
Can be used in locations which do not permit use of other fastening methods.
D
Process lends itself to the automated concept or high production shops.
D
Capable of producing welds which are less costly per unit than other methods.
D
Process may be effectively utilized with a minimum of time spent in personnel training.
D
Process may be effectively used in maintaining weld quality with a minimum inspection time.
2-3.
Equipment
Necessary equipment for stud welding:
D
Constant Current (CC) Power Source
D
Stud Welding Gun
D
Weld Cable With Stud Gun Control Card
D
Work/Ground Cable With “C” Clamp Type Connector