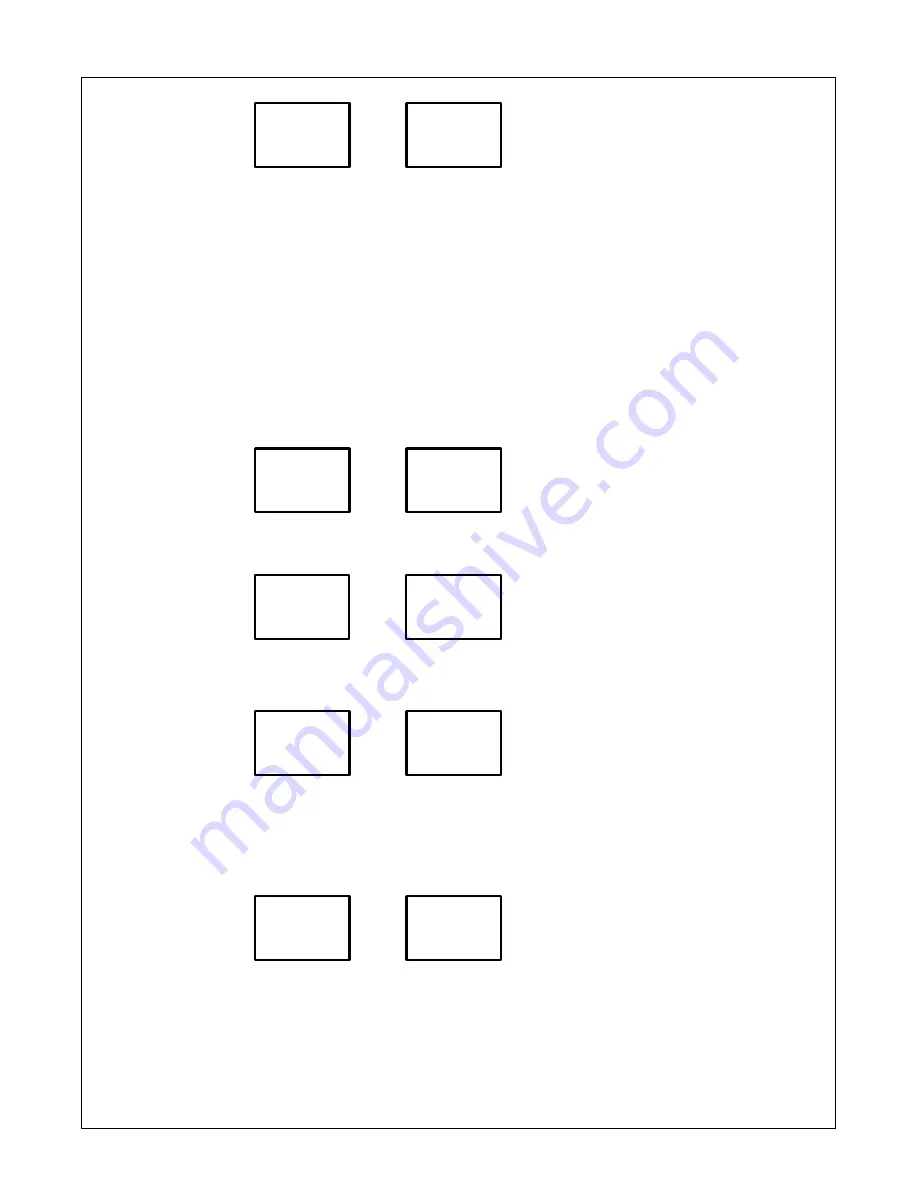
.
A complete Parts List is available at www.MillerWelds.com
OM-257219 Page 26
6-2
Configuration Option Menu (Continued)
PULSED MIG Manual/Auto Control
This option sets the PULSED MIG control as manu-
al (PULS MAN) or Auto (PULS AUTO) operation.
When set to manual operation, the arc length set-
ting on power source and wire speed setting on wire
feeder need to be adjusted independently to
achieve the desired arc length. When set to Auto
operation, once arc length is determined it is not
necessary to change the arc length value with
changes in wirefeed speed.
The AlumaPower 450 MPa and synergic
feeders
allow single knob control of the arc. As wirefeed
speed is increased or decreased, the pulse param-
eters increase or decrease matching the power
output to the wire speed.
.
Auto Operation will only work with synergic
wire feeders. All other wire feeders will only op-
erate as manual control. Even when Auto is
displayed, operation will be manual when any
other feeder is connected. See product literat-
ure for a list of compatible synergic wire feed-
ers.
PULSED MIG Adjustment
This option allows adjusting the Pulsed MIG pro-
cess in units of Arc Length (PULS ARCL) or preset
voltage (PULS VOLT).
.
In PULS AUTO operation adjustments can
only be made in units of arc length.
Wire Feed Speed And Wire Diameter Units
WFS IPM:
WFS is displayed in inches per minute
Diameter is displayed in inches
WFS MPM:
WFS is displayed in meters per minute
Diameter is displayed in millimeters
Revision Information
This option identifies the unit’s weld library (INFO
LIB) and firmware revision (INFO REV).
Press the Setup Button while the unit is displaying
INFO LIB to identify the unit’s weld library.
Press the Setup Button while the unit is displaying
INFO REV to identify the unit’s firmware revision.
Pressing the Setup Button while the unit is display-
ing INFO NO will move to the next configuration op-
tion.
Exit Configuration Option Menu
Press the Setup Button while the unit is displaying
EXIT NO to return to the first configuration option.
Press the Setup Button while the unit is displaying
EXIT YES to exit the Configuration Option Menu.
.
The Configuration Option Menu can be exited
at any time by turning the unit off. Only if the unit
is turned off after EXIT NO is displayed will con-
figuration option changes be saved.
PULS
AUTO
INFO
NO
PULS
ARCL
EXIT
NO
WFS
IPM