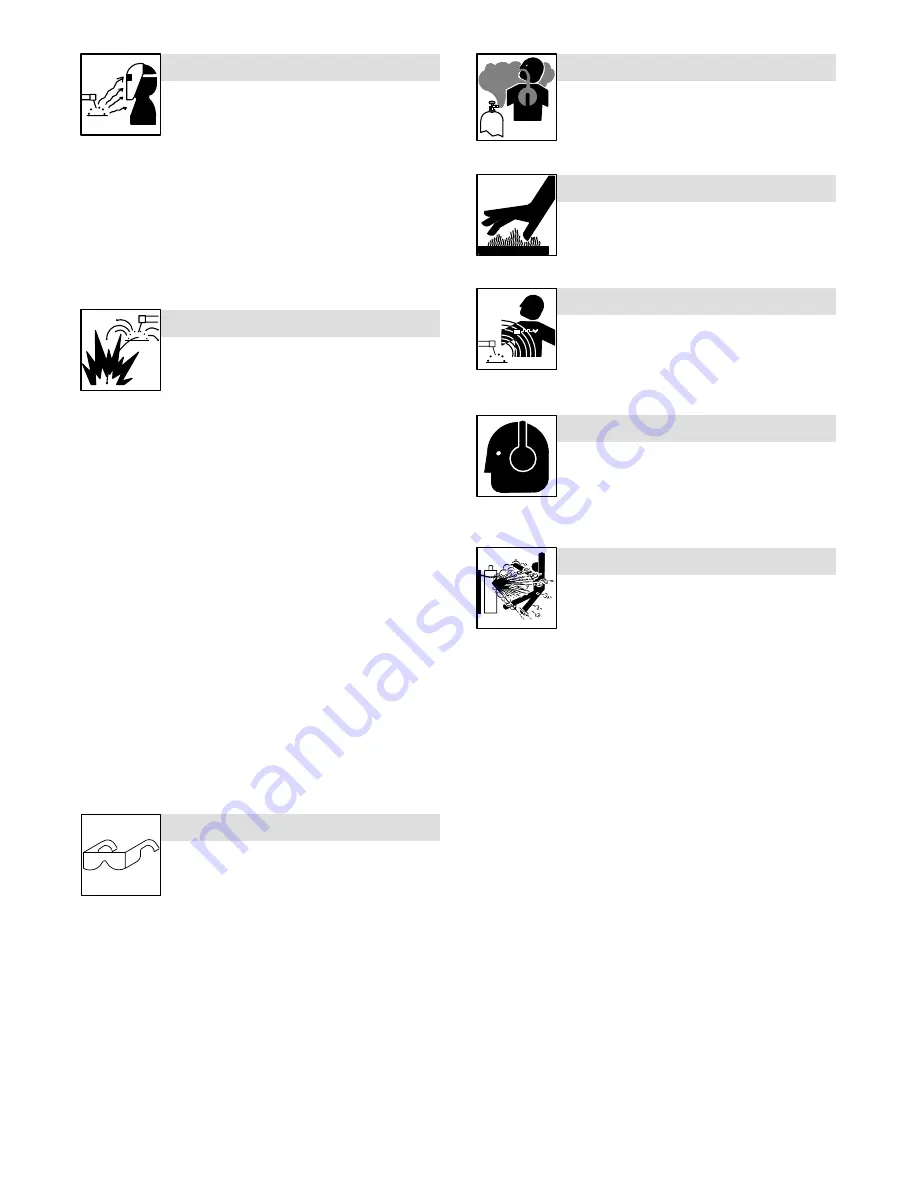
OM-2236 Page 2
Arc rays from the welding process produce intense
visible and invisible (ultraviolet and infrared) rays
that can burn eyes and skin. Sparks fly off from the
weld.
ARC RAYS can burn eyes and skin.
D
Wear a welding helmet fitted with a proper shade of filter to protect
your face and eyes when welding or watching (see ANSI Z49.1
and Z87.1 listed in Safety Standards).
D
Wear approved safety glasses with side shields under your
helmet.
D
Use protective screens or barriers to protect others from flash and
glare; warn others not to watch the arc.
D
Wear protective clothing made from durable, flame-resistant mate-
rial (leather and wool) and foot protection.
Welding on closed containers, such as tanks,
drums, or pipes, can cause them to blow up. Sparks
can fly off from the welding arc. The flying sparks, hot
workpiece, and hot equipment can cause fires and
burns. Accidental contact of electrode to metal objects can cause
sparks, explosion, overheating, or fire. Check and be sure the area is
safe before doing any welding.
WELDING can cause fire or explosion.
D
Protect yourself and others from flying sparks and hot metal.
D
Do not weld where flying sparks can strike flammable material.
D
Remove all flammables within 35 ft (10.7 m) of the welding arc. If
this is not possible, tightly cover them with approved covers.
D
Be alert that welding sparks and hot materials from welding can
easily go through small cracks and openings to adjacent areas.
D
Watch for fire, and keep a fire extinguisher nearby.
D
Be aware that welding on a ceiling, floor, bulkhead, or partition can
cause fire on the hidden side.
D
Do not weld on closed containers such as tanks, drums, or pipes,
unless they are properly prepared according to AWS F4.1 (see
Safety Standards).
D
Connect work cable to the work as close to the welding area as
practical to prevent welding current from traveling long, possibly
unknown paths and causing electric shock and fire hazards.
D
Do not use welder to thaw frozen pipes.
D
Remove stick electrode from holder or cut off welding wire at
contact tip when not in use.
D
Wear oil-free protective garments such as leather gloves, heavy
shirt, cuffless trousers, high shoes, and a cap.
D
Remove any combustibles, such as a butane lighter or matches,
from your person before doing any welding.
FLYING METAL can injure eyes.
D
Welding, chipping, wire brushing, and grinding
cause sparks and flying metal. As welds cool,
they can throw off slag.
D
Wear approved safety glasses with side
shields even under your welding helmet.
BUILDUP OF GAS can injure or kill.
D
Shut off shielding gas supply when not in use.
D
Always ventilate confined spaces or use
approved air-supplied respirator.
HOT PARTS can cause severe burns.
D
Do not touch hot parts bare handed.
D
Allow cooling period before working on gun or
torch.
MAGNETIC FIELDS
can affect pacemakers.
D
Pacemaker wearers keep away.
D
Wearers should consult their doctor before
going near arc welding, gouging, or spot
welding operations.
NOISE can damage hearing.
Noise from some processes or equipment can
damage hearing.
D
Wear approved ear protection if noise level is
high.
Shielding gas cylinders contain gas under high
pressure. If damaged, a cylinder can explode. Since
gas cylinders are normally part of the welding
process, be sure to treat them carefully.
CYLINDERS can explode if damaged.
D
Protect compressed gas cylinders from excessive heat, mechani-
cal shocks, slag, open flames, sparks, and arcs.
D
Install cylinders in an upright position by securing to a stationary
support or cylinder rack to prevent falling or tipping.
D
Keep cylinders away from any welding or other electrical circuits.
D
Never drape a welding torch over a gas cylinder.
D
Never allow a welding electrode to touch any cylinder.
D
Never weld on a pressurized cylinder − explosion will result.
D
Use only correct shielding gas cylinders, regulators, hoses, and fit-
tings designed for the specific application; maintain them and
associated parts in good condition.
D
Turn face away from valve outlet when opening cylinder valve.
D
Keep protective cap in place over valve except when cylinder is in
use or connected for use.
D
Read and follow instructions on compressed gas cylinders,
associated equipment, and CGA publication P-1 listed in Safety
Standards.
Summary of Contents for SRH-503
Page 4: ...Notes...
Page 23: ...OM 2236 Page 19 5 2 Electrode Amperage Selector...
Page 26: ...OM 2236 Page 22 Notes...