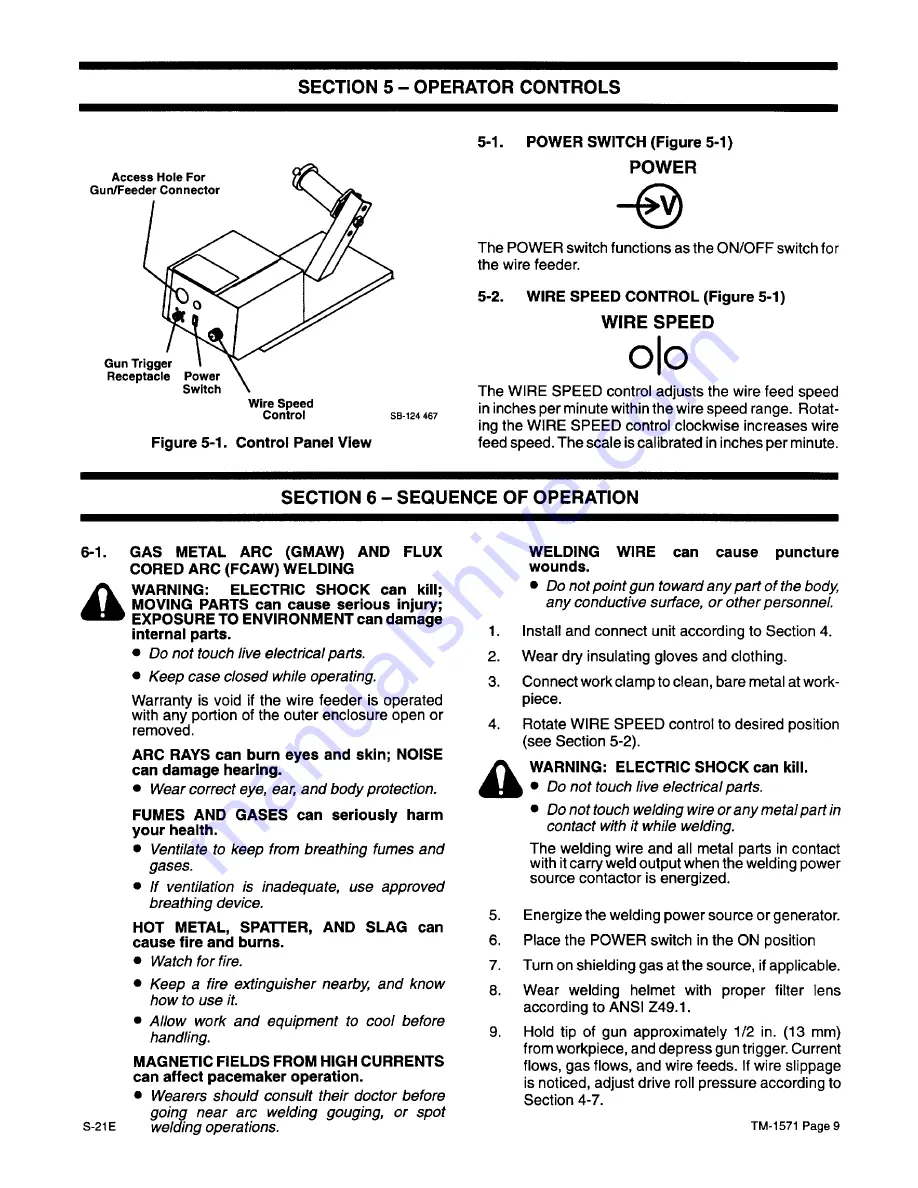
SECTION 5- OPERATOR CONTROLS
5-1.
POWER SWITCH (Figure 5-1)
POWER
The POWER switch functions as the ON/OFF switch for
the wire feeder.
5-2.
WIRE SPEED CONTROL (Figure 5-1)
WIRE SPEED
ojo
The WIRE SPEED control adjusts the wire feed speed
88-124 467
in inches per minute within the wire speed range. Rotat-
ing the WIRE SPEED control clockwise increases wire
feed speed. The scale is calibrated in inches per minute.
SECTION 6— SEQUENCE OF OPERATION
6-1.
GAS
METAL ARC (GMAW) AND FLUX
CORED ARC (FCAW) WELDING
A
WARNING:
ELECTRIC SHOCK can kill;
MOVING PARTS can cause serious injury;
EXPOSURE TO ENVIRONMENT can damage
internal parts.
• Do not touch live electrical parts.
• Keep case closed while operating.
Warranty is void if the wire feeder is operated
with any portion of the outer enclosure open or
removed.
ARC RAYS can burn eyes and skin; NOISE
can damage hearing.
• Wear correct eye, ear, and body protection.
FUMES AND GASES can seriously harm
your health.
• Ventilate to keep from breathing fumes and
gases.
• If ventilation is inadequate, use approved
breathing device.
HOT METAL, SPATrER, AND SLAG can
cause fire and burns.
• Watch for fire.
• Keep a fire extinguisher nearby and know
how to use it.
• Allow work and equipment to cool before
handling.
MAGNETIC FIELDS FROM HIGH CURRENTS
can affect pacemaker operation.
• Wearers should consult their doctor before
going near arc welding gouging, or spot
5-21 E
welding operations.
WELDING
WIRE
can
cause
puncture
Wounds.
• Do not point gun toward any part of the body
any conductive surface, or other personnel.
1.
Install and connect unit according to Section 4.
2.
Wear dry insulating gloves and clothing.
3.
Connect work clamp to clean, bare metal at work-
piece.
4.
Rotate WIRE SPEED control to desired position
(see Section 5-2).
A
WARNING: ELECTRIC SHOCK can kill.
• Do not touch live electrical parts.
• Do not touch welding wireorany metal part in
contact with it while welding.
The welding wire and all metal parts in contact
with it carry weld output when the welding power
source contactor is energized.
5.
Energize the welding power source or generator.
6.
Place the POWER switch in the ON position
7.
Turn on shielding gas at the source, if applicable.
8.
Wear welding helmet with proper filter lens
according to ANSI Z49.1.
9.
Hold tip of gun approximately 1/2 in. (13 mm)
from workpiece, and depress gun trigger. Current
flows, gas flows, and wire feeds. If wire slippage
is noticed, adjust drive roll pressure according to
Section 4-7.
Access Hole For
Gun/Feeder Connector
Gun Trigger
Receptacle
Wire Speed
Control
Figure 5-1. Control Panel View
TM-1571 Page 9
Summary of Contents for S-21E
Page 2: ......
Page 17: ...S 21E TM 1571 Page 13 Notes...
Page 38: ...CO 0 N C Ci 0 E 4 U U N in C J 1 4 I 0 IL N C J Ci E a Ci a V TM i571 Page 34 S 21E...
Page 42: ...SA 123 147 F Figure 12 3 Motor Control Circuit Card PCi TM 1571 Page 38 S 21E...
Page 46: ...Notes...
Page 47: ...Notes...
Page 48: ......