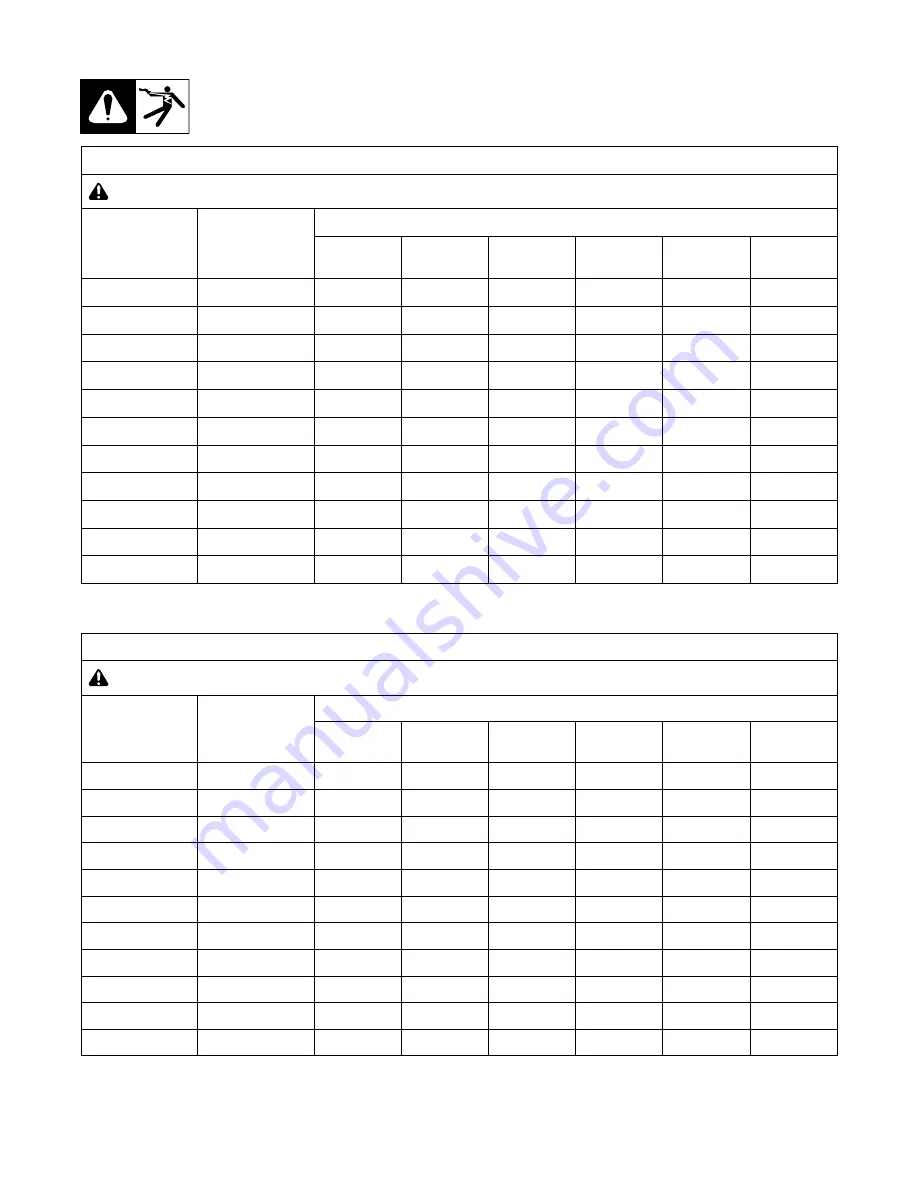
OM-4434 Page 56
13-11. Selecting Extension Cord (Use Shortest Cord Possible)
Cord Lengths for 120 Volt Loads
If unit does not have GFCI receptacles, use GFCI-protected extension cord.
Maximum Allowable Cord Length in ft (m) for Conductor Size (AWG)*
Current
(Amperes)
Load (Watts)
4
6
8
10
12
14
5
600
350 (106)
225 (68)
137 (42)
100 (30)
7
840
400 (122)
250 (76)
150 (46)
100 (30)
62 (19)
10
1200
400 (122)
275 (84)
175 (53)
112 (34)
62 (19)
50 (15)
15
1800
300 (91)
175 (53)
112 (34)
75 (23)
37 (11)
30 (9)
20
2400
225 (68)
137 (42)
87 (26)
50 (15)
30 (9)
25
3000
175 (53)
112 (34)
62 (19)
37 (11)
30
3600
150 (46)
87 (26)
50 (15)
37 (11)
35
4200
125 (38)
75 (23)
50 (15)
40
4800
112 (34)
62 (19)
37 (11)
45
5400
100 (30)
62 (19)
50
6000
87 (26)
50 (15)
*Conductor size is based on maximum 2% voltage drop
Cord Lengths for 240 Volt Loads
If unit does not have GFCI receptacles, use GFCI-protected extension cord.
Maximum Allowable Cord Length in ft (m) for Conductor Size (AWG)*
Current
(Amperes)
Load (Watts)
4
6
8
10
12
14
5
1200
700 (213)
450 (137)
225 (84)
200 (61)
7
1680
800 (244)
500 (152)
300 (91)
200 (61)
125 (38)
10
2400
800 (244)
550 (168)
350 (107)
225 (69)
125 (38)
100 (31)
15
3600
600 (183)
350 (107)
225 (69)
150 (46)
75 (23)
60 (18)
20
4800
450 (137)
275 (84)
175 (53)
100 (31)
60 (18)
25
6000
350 (107)
225 (69)
125 (38)
75 (23)
30
7000
300 (91)
175 (53)
100 (31)
75 (23)
35
8400
250 (76)
150 (46)
100 (31)
40
9600
225 (69)
125 (38)
75 (23)
45
10,800
200 (61)
125 (38)
50
12,000
175 (53)
100 (31)
*Conductor size is based on maximum 2% voltage drop