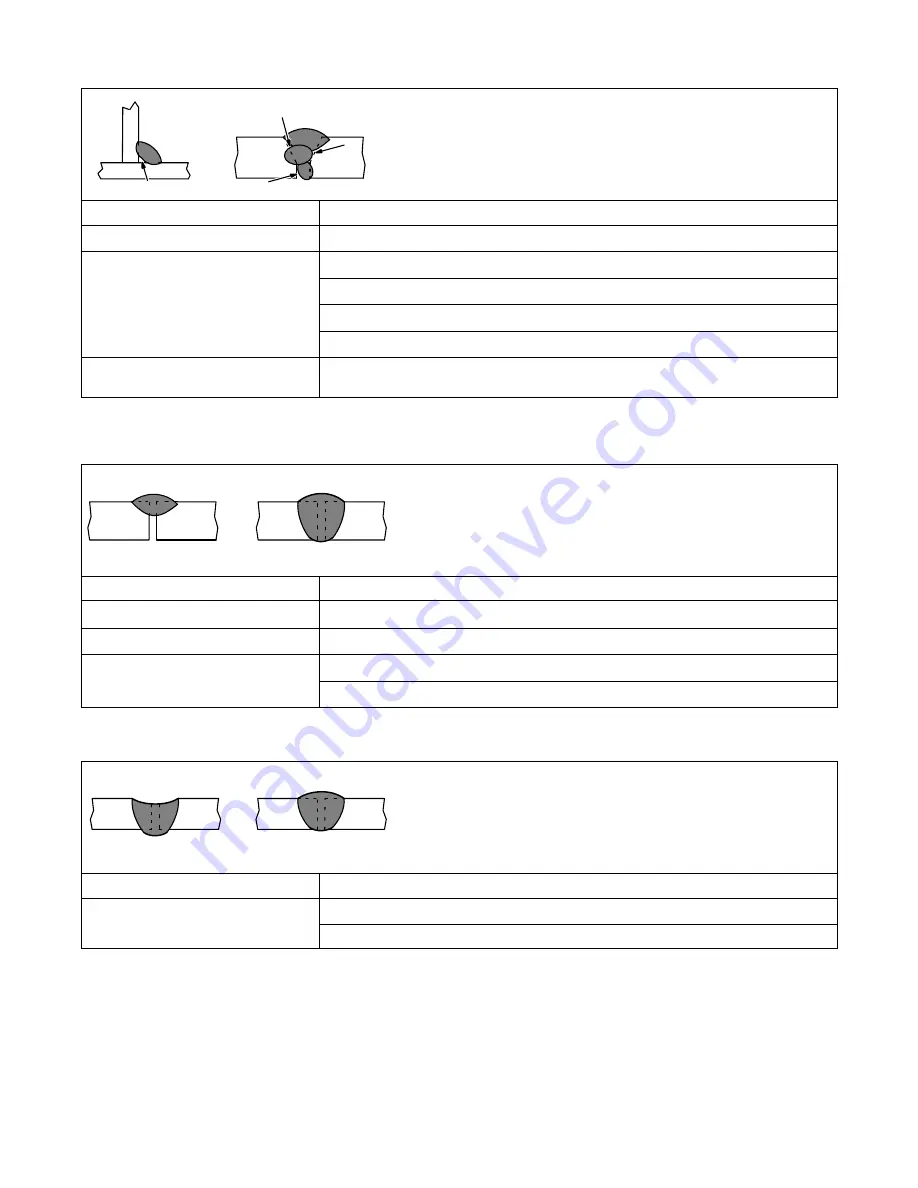
OM-4417 Page 44
12-16. Troubleshooting
−
Incomplete Fusion
Incomplete Fusion
−
failure of weld metal to fuse completely with
base metal or a preceeding weld bead.
Possible Causes
Corrective Actions
Insufficient heat input.
Increase amperage. Select larger electrode and increase amperage.
Improper welding technique.
Place stringer bead in proper location(s) at joint during welding.
Adjust work angle or widen groove to access bottom during welding.
Momentarily hold arc on groove side walls when using weaving technique.
Keep arc on leading edge of weld puddle.
Workpiece dirty.
Remove all grease, oil, moisture, rust, paint, coatings, slag, and dirt from work surface before
welding.
12-17. Troubleshooting
−
Lack Of Penetration
Lack Of Penetration
−
shallow fusion between weld metal and
base metal.
Lack of Penetration
Good Penetration
Possible Causes
Corrective Actions
Improper joint preparation.
Material too thick. Joint preparation and design must provide access to bottom of groove.
Improper weld technique.
Keep arc on leading edge of weld puddle.
Insufficient heat input.
Increase amperage. Select larger electrode and increase amperage.
Reduce travel speed.
12-18. Troubleshooting
−
Excessive Penetration
Good Penetration
Excessive Penetration
−
weld metal melting through base metal and
hanging underneath weld.
Excessive Penetration
Possible Causes
Corrective Actions
Excessive heat input.
Select lower amperage. Use smaller electrode.
Increase and/or maintain steady travel speed.
Summary of Contents for Blue Star 145
Page 4: ......
Page 34: ...OM 4417 Page 30 226 738 A Figure 10 2 Circuit Diagram for DX Models ...
Page 54: ...OM 4417 Page 50 ...