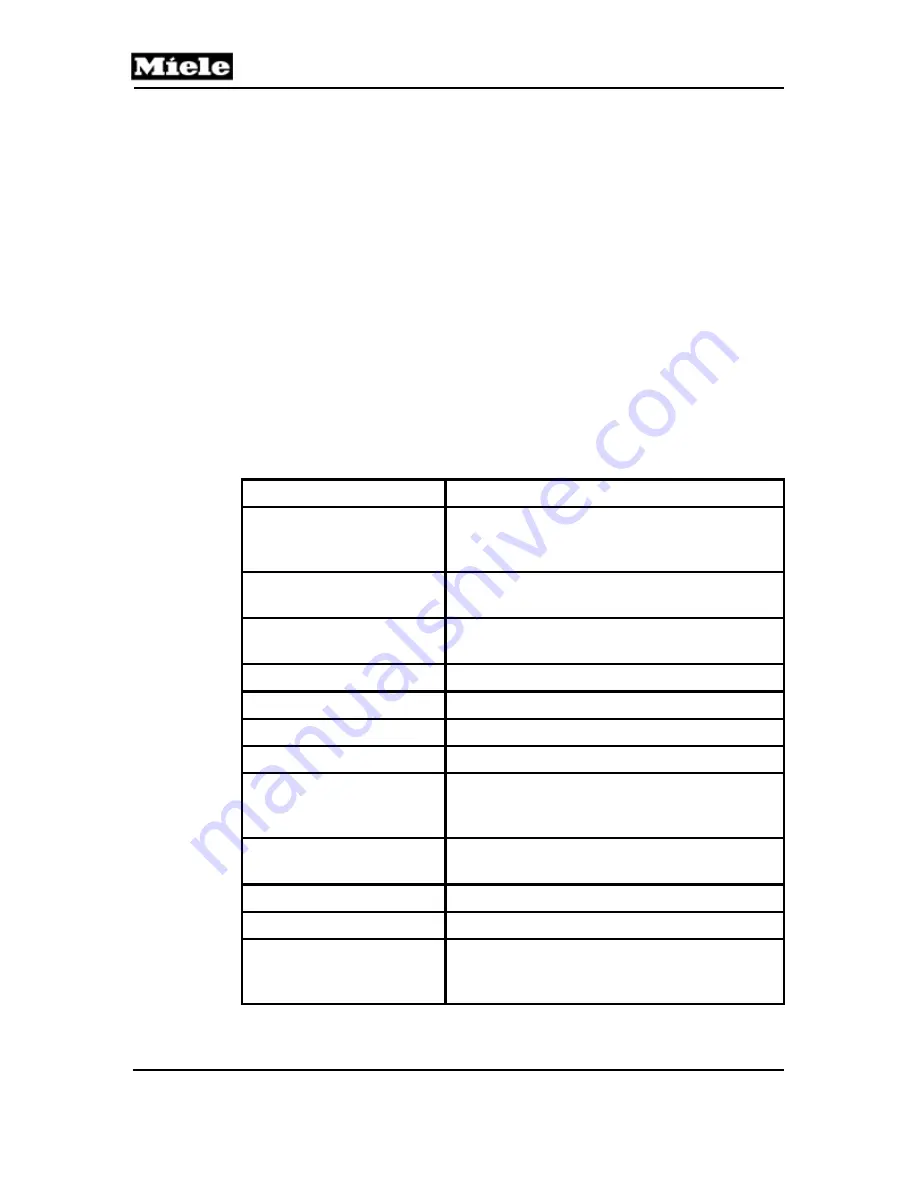
Technical Information
W1900 Series Clothes Washers
6.2
Service Mode - W1966 and W1986
Access
1. Switch Off the appliance. Close the Door.
2. Turn the Program Selector Switch to 12 o’clock.
3. Press and hold the Buzzer and Extended Buttons.
4. Switch On the appliance.
5. Release the Buzzer and Extended buttons.
Acknowledgement Indicator
Successful access into the Service Mode is indicated by a flashing
“Pre-Wash” LED. (On the W1986 the display shows the microprocessor
ROM ID code. Example: -08)
Navigation
Turn the Program Selector Switch to the desired position in accordance
with the Table 6-2 – Service Mode Functions.
Selector Switch Program
Function
COTTONS 190
Water intake via Pre-Wash valve. Water
reaches level 1 position then heaters are
activated up to 95º F.
COTTONS 140
Water intake via the Main Wash valve until
water level 2 is reached.
COTTONS 120
Water intake via the Rinse Valve until water
level 3 is reached.
COTTONS 105
(Not Used)
PERMA PRESS 105
Water intake via Hot Water Valve.
COTTONS COLD
Drain Pump is activated.
PERMA PRESS 140
Drum rotates w/ reverse action.
PERMA PRESS 120
Drain pump operates, drum spins to set spin
speed on control panel (up to 1200 rpm
only).
WOOLENS 85
*See the Fault Code Retrieval / Clearing
section 100 – 4.2 (next page)
DELICATES COLD
Buzzer activated.
DELICATES 85
LED flashing test.
DELICATES 105
Operating hours in blocks of 3. (Example:
9423 hours would be shown as “009” then
“423”) Note: Applies to W1986 only.
Table 6-2:
Service Mode Functions (W1966 & W1986)
50