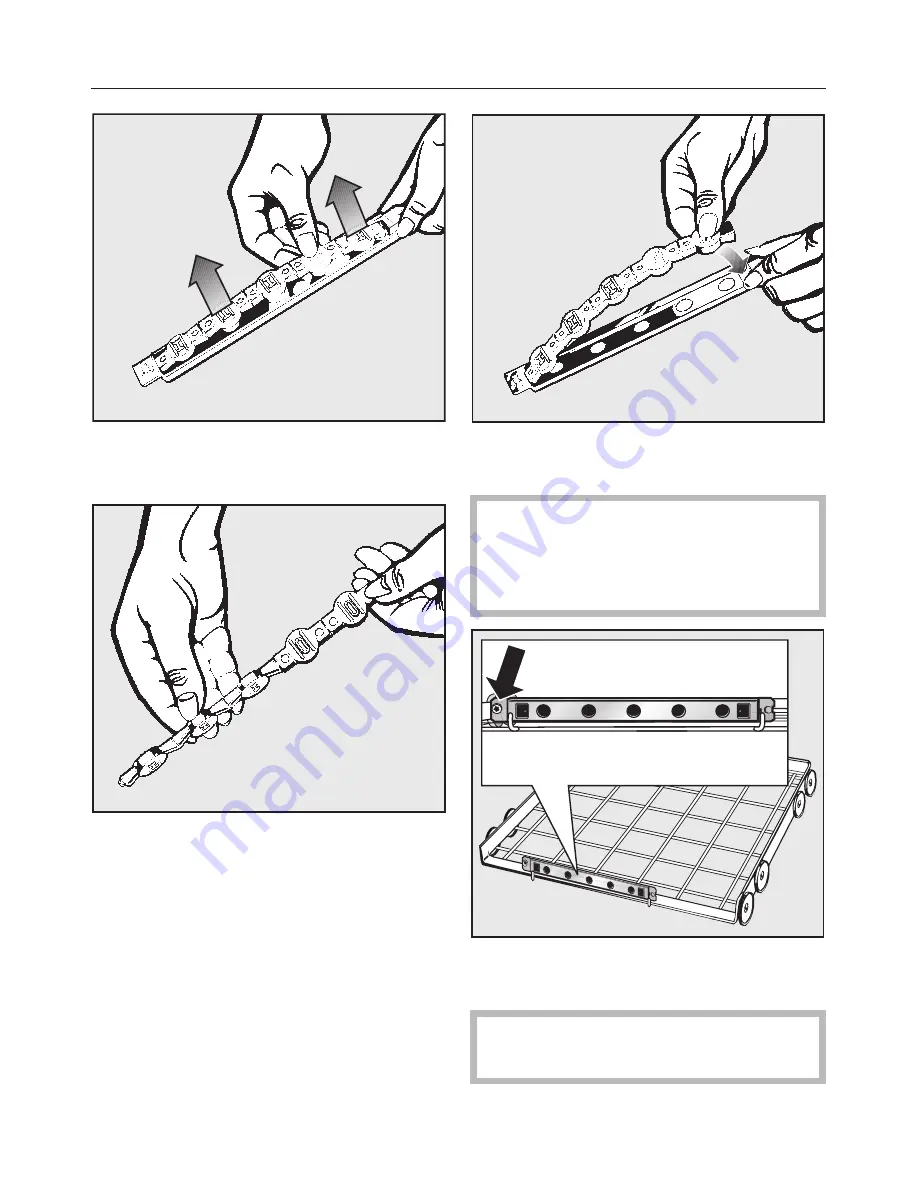
^
Remove the magnetic strip from the
track.
^
Set the programme place coding.
^
Put the magnetic strip back in the
track.
The magnetic strip must be placed
in the track such that the Bit coding
set out in the chart is visible through
the round windows in the track.
^
Place the track in the holder in the
mobile unit and screw firmly in place.
The magnetic strip must have
grey
magnets.
Automatic mobile unit recognition (AWK) (optional)
20