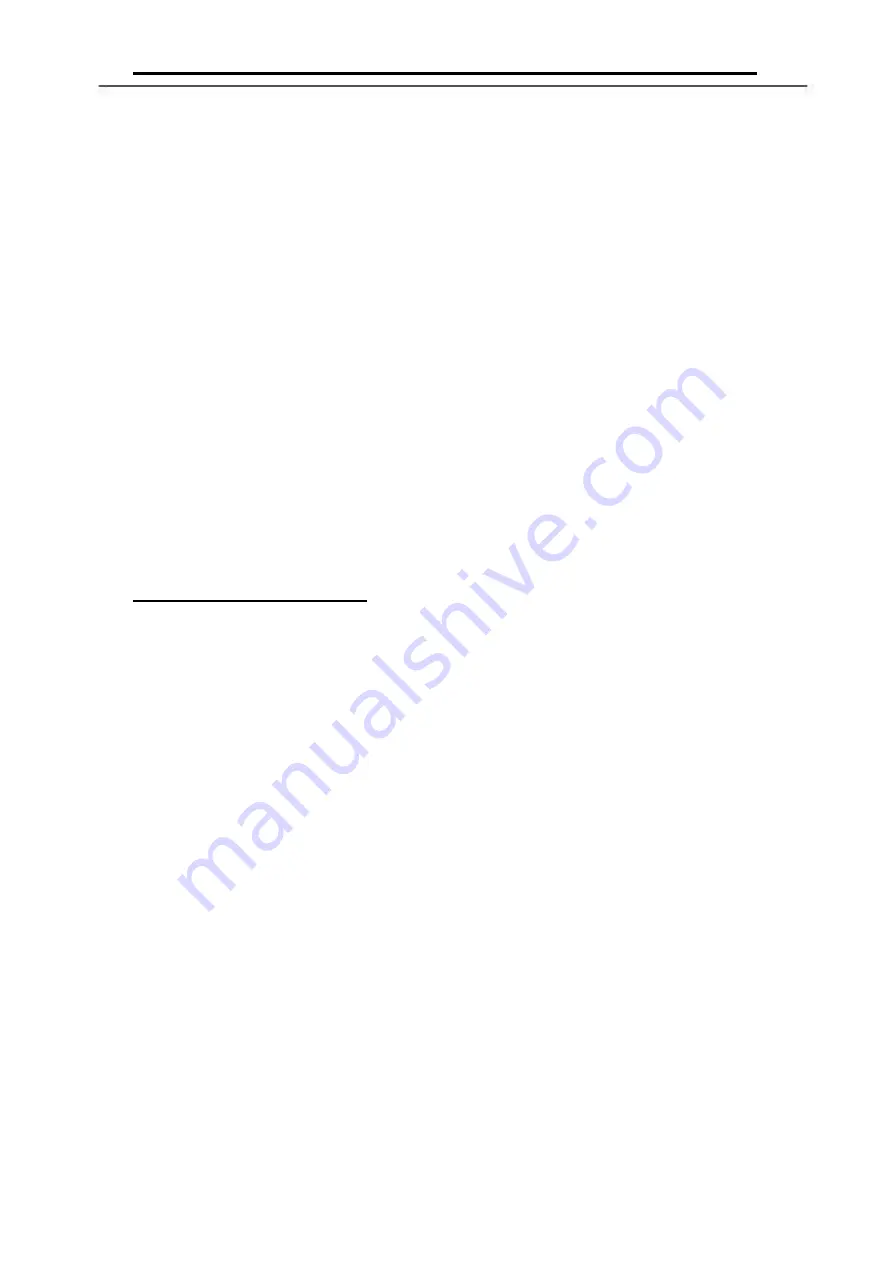
Maintenance Service and Troubleshooting
6. Common Problems in Refrigerators and Their Remedies
Issues occurring in refrigerators are closely related to the quality of their
components, the manufacturers’ workmanship, and if they are properly used and
maintained. The aspects generally used to gauge the working conditions of a
refrigerator include its temperature, operation rate, power consumption, noise
level, and other functional indexes. If any one of these factors is beyond its
permissible range, this indicates that there is a fault or issue in the refrigerator.
During the life cycle of a refrigerator, the probability of an issue occurring
within a specific time is called its failure rate. Comparing the refrigerator’s control
circuit system and its refrigerating system, the failure rate of the former is higher,
and that of the thermostat is the highest. In troubleshooting, first determine where
the problem originates from: the control system or the refrigerating system.
Generally there is no trouble-indicating instrument mounted on a domestic
refrigerator, so an issue’s location and nature should be determined according to
its features. Therefore, experience in servicing is important in troubleshooting.
Experienced service technicians can correctly locate issues and take reasonable
measures based on their comprehensive analysis of problematic characteristics
and of various kinds of refrigerators.
Three Checkup Essentials:
1. Look
a.
Check the refrigerating system tubing for cracks and welded parts for
leaks. If there is a leakage, an oil stain will appear.
b.
Check the suction and exhaust pressure values (high and low pressures)
of compressor to see if they are normal.
c.
Check frost conditions on the evaporator and the gas return tube. It is
abnormal to see no frost or frost on only one part of the evaporator.
d.
Check the speed of temperature drop inside freezer compartment. It is
abnormal if the speed is noticeably slower than the normal.
e.
Check area to see if it is suitable for placing a refrigerator there.
f.
Check door seal, casing, surface, and thermal insulation layer.
g.
Look at the main control panel to determine if various indicators are
normal.
2. Listen
a.
Listen to the noises emitted when the compressor is running. Hums from
a fully enclosed unit is caused by overload, indicating that the motor
cannot be started normally. A clattering sound from inside the start relay
signifies the start contacts cannot be released normally. A whistling
sound is caused by high-pressure gas escaping through a crack in the
pressure tube inside the compressor. The sound of striking clunks
indicate a suspended spring inside the compressor has broken.
15
Summary of Contents for WHS-169WES1
Page 4: ...Safety Precautions Safety Precautions 4 ...
Page 5: ...Safety Precautions 5 ...
Page 6: ...Safety Precautions 6 ...
Page 9: ...Circuit Diagram 1 Schematic Circuit Diagram Circuit Diagram 9 ...
Page 30: ......