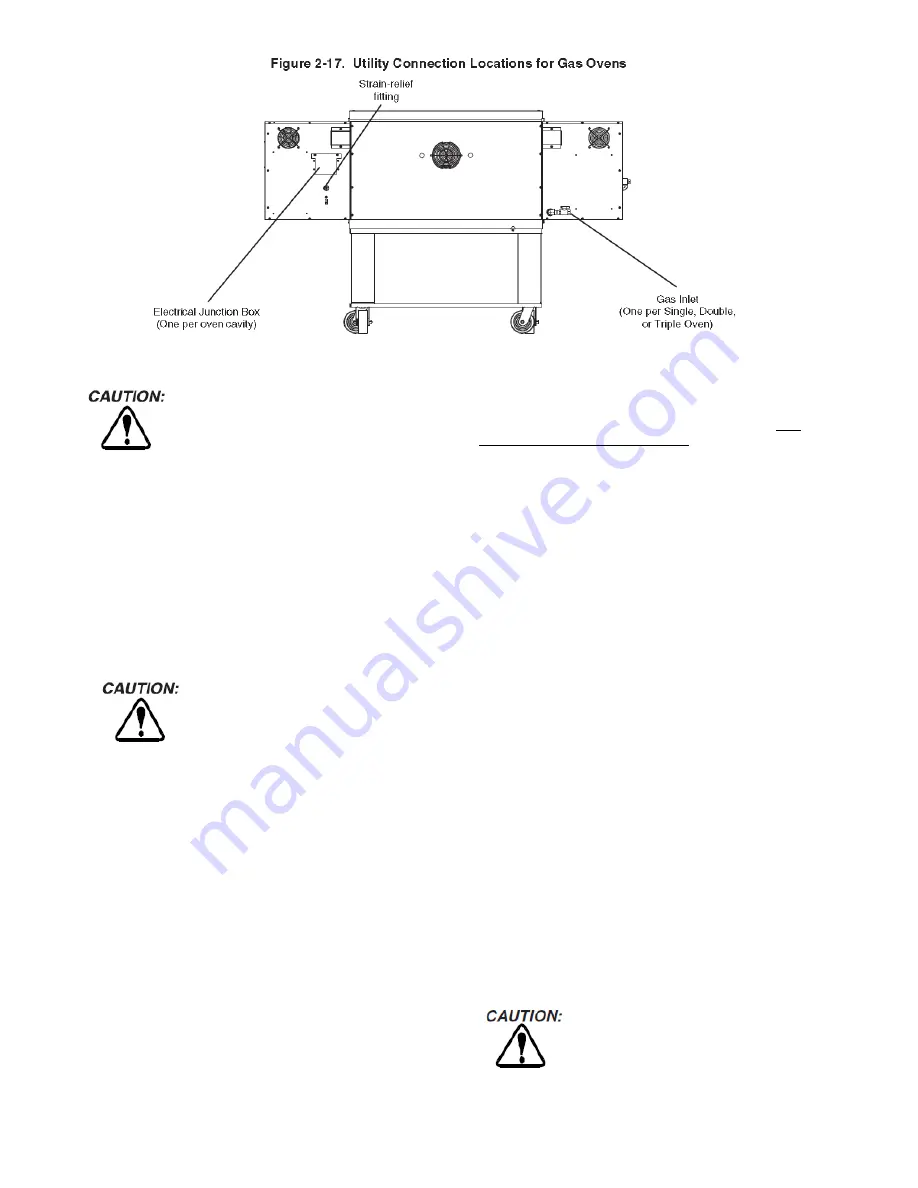
19
VII.
GAS SUPPLY
DURING PRESSURE TESTING NOTE
ALL OF THE FOLLOWING:
1. The oven and its individual shutoff valve must be
disconnected from the gas supply piping system during
any pressure testing of that system at test pressure in
excess of ½ psi (3.45 kPa).
2. The oven must be isolated from the gas supply piping
system by closing its individual manual shutoff during
any pressure testing of the gas supply piping system at
test pressure equal to or less than ½ psi (3.45 kPa).
3. If incoming pressure is over 14” W.C. (35 mbar), a
separate regulator MUST be installed in the line
BEFORE the individual shutoff valve for the oven.
To prevent damage to the control valve
regulator during initial turn-on of gas, it is
very important to open the manual shutoff
valve very slowly.
After the initial gas turn-on, the manual
shutoff valve must remain open except
during pressure testing as outlined in the
above steps or when necessary during
service maintenance.
A. Gas Utility Rough-In Recommendations
The following system specifications are STRONGLY
RECOMMENDED. Deviating from these recommendations
may affect the baking performance of the oven.
Gas Meter
One or two cavities: 425 CFH meter
Three oven cavities: 630 CFH meter
Gas Line
DEDICATED GAS LINE from the gas meter to
the oven
1-½” (38.1mm) pipe for Natural gas
1-½” (38.1mm) pipe for Propane gas
Maximum length: 200’ (61m). Each 90° elbow
equals seven additional feet (2.13m) of pipe.
B. Connection
Check the oven’s gas supply requirements before making
the gas utility connections. Gas supply requirements are
listed on the oven’s serial plate and in Table 1-4. Gas
Orifice and Pressure Specifications (in Section 1,
Description).
Check the serial plate to determine the type of gas (Propane
or Natural) to be used with the oven.
Refer to the instructions in the gas hose package (included
in the Installation Kit) before connecting the gas line. One
gas line connection method is shown in Figure 2-18;
however, compliance with the applicable standards and
regulations is mandatory.
Inlet and regulated gas pressure readings can be taken
using a digital tube manometer at the tap location shown in
Figure 2-19. Figure 2-19 shows the burner assembly and
Figure 2-21 shows the gas valve.
NOTE:
The installation must conform with local codes or in
the absence of local codes, to the National Fuel
Gas Code, ANSI Z223.1-latest edition.
Certain safety code requirements exist for the installation of
gas ovens; refer to the beginning of Section 2 for a list of the
installation standards. In addition, because the oven is
equipped with casters, the gas line connection shall be made
with a connector that complies with the Standard for
Connectors for Movable Gas Appliances, ANSI Z21.69 (in
U.S.A.), as well as a quick-disconnect device that complies
with the Standard for Quick-Disconnect Devices for Use With
Gas Fuel, ANSI Z21.41 (in U.S.A.).
C. Gas Conversion
Where
permitted
by local and national codes, it is possible to
convert ovens from natural gas to propane or from propane
to natural gas. Use the appropriate Middleby Gas
Conversion Kit for the specific oven model.
The terms of the oven’s warranty require all
startups, conversions and service work to be
performed by a Middleby Authorized Service
Agent.
Summary of Contents for PS638 Series
Page 10: ...5 A P N 71687 SINGLE OVEN BASE TOP KIT...
Page 11: ...6 B P N 73754 DOUBLE OVEN BASE TOP KIT...
Page 12: ...7 C P N 73556 TRIPLE OVEN BASE TOP KIT...
Page 13: ...8 III PS638 OVEN LAYOUTS A Single Oven...
Page 14: ...9...
Page 15: ...10 III PS638 OVEN LAYOUTS cont B Double and Triple Oven...
Page 16: ...11...
Page 41: ...36 SECTION 5 WIRING DIAGRAMS...
Page 42: ...37 Electric Schematics...
Page 43: ...38...
Page 44: ...39...
Page 45: ...40...
Page 46: ...41 SECTION 6 ASSEMBLY DRAWINGS...
Page 47: ...42...
Page 48: ...43...
Page 49: ...44...
Page 50: ...45...