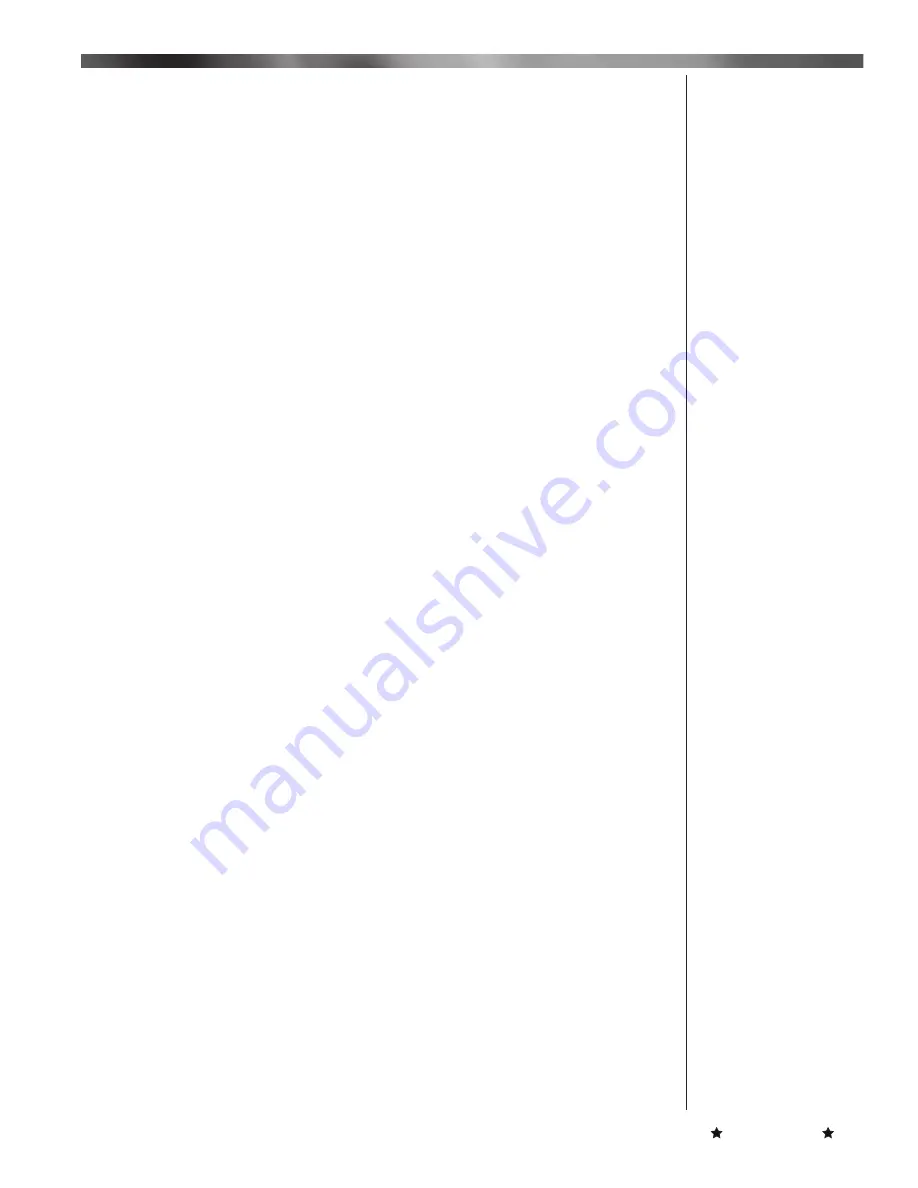
11
Midco International Inc.
8471 91
MADE
in the
USA
Part 1 - Installation & Service
26.
Check gas pressure on side inlet of fi rst solenoid gas valve.
27.
Inlet pressure to side inlet of fi rst solenoid gas valve at high fi re should be 5″ WC.
28.
Readjust main gas pressure regulator if required.
29.
Check diff erential gas pressure at barb fi ttings.
30.
Diff erential gas pressure should be 1.8″ WC for high fi re.
31.
To adjust high fi re fi nal setting the manual valve downstream of Dungs valve can be closed
slightly.
Power up unit and the starting sequence begins. The EBM blower motor is energized and will run up
to high blower speed for 20 seconds. After initial prepurge the EBM blower motor will modulate down
to low speed. Once EBM blower motor reaches low speed the main gas valve and ignition control
will be energized. If the burner lights and the temperature control is calling for heat the burner will be
modulated depending on the DC Volt signal being generated from the temperature control.
__________________________________________
The Midco LNB burner comes with a limiting gas orifi ce which is required to maintain the Low NOx
readings and fi ring rate. The orifi ce is located between the Ratio Regulator Zero Governor valve
and EBM blower inlet. Do not attempt to modify the location or orifi ce size. Attach a diff erential gas
pressure manometer to check gas fl ow. The locations for attaching the gas pressure manometer are
located on the main gas valves. See page 4. Of the two taps that should be used, one is located on
the upstream tap on fi rst main gas valve and the other on the downstream bottom tap on the 2nd main
gas valve for LNB 1000. Refer to piping diagram, Figure # 4A, for proper location. For LNB 500 attach
a diff erential gas pressure manometer to check for gas fl ow to outlet pressure tap on main gas valve,
and the other on the 1/8″ tap on gas pipe downstream of main gas valve. Remove the plug on both
fi ttings. Attach a barb fi tting in order to hook up the required tubing to the diff erential gas pressure
manometer. Set temperature control below booth temperature so burner will light and stay lit at low
fi re (or remove DCV wiring from RTC board). Energize burner power switch.
The burner blower will be energized and start sequence will begin. Once the main fl ame is established
the burner will start at low fi re. The gas pressure at the two gas pressure taps will be approximately.
0.11″ W.C. to .25″ WC. This is the minimum fi ring rate for the Midco LNB burner.
Adjusting low fi re:
If the fl ame stays on and low fi re setting is too high, adjust low fi re on the Ratio
Regulator Zero Governor. The LNB burner is shipped with the adjustment screw located on the top of
the Ratio Regulator Zero Governor at 4-5 turns counterclockwise. To decrease low fi re turn the screw
counterclockwise. To increase low fi re turn the screw clockwise. If the low fi re is adjusted properly
the fl ame will be mostly blue with a slight orange glow, visually inspect the fl ame through burner
peep sight. Check the diff erential gas pressure and fl ame signal and adjust the Ratio Regulator Zero
Governor valve as required.
Adjusting high fi re:
Turn temperature control above set point to provide 10 DCV to RTC board to
set high fi re. Minimal adjustments can be made. Check inlet pressure to fi rst gas valve it should be 5″
W.C. maximum. Adjust main gas pressure regulator if required. Flame signal should be steady and
above 2 UA DC. For gas pressure settings see Charts 1 & 2 on page 5.
__________________________________________
Burner Ignition Sequence with Fenwal control.
1.
Call for heat
a. LNB Burner blower will go to maximum speed
b. SCEBM-1 control LED will fl ash red
2.
After 20 seconds delay
a. LNB burner will go to minimum speed
b. Ignition control will be energized
c. Ignition control will send 120V to the spark generator
d. SCEBM-1 control LED will remain solid red
e. Main gas valves will be energized
f.
SCEBM-1 control LED will fl ash red (DC signal below 2 DCV) or green (DC signal
above 2 DCV), depending on DCV signal
V Burner Setup
VI Burner
Ignition Sequence
IV Burner Startup
Continued