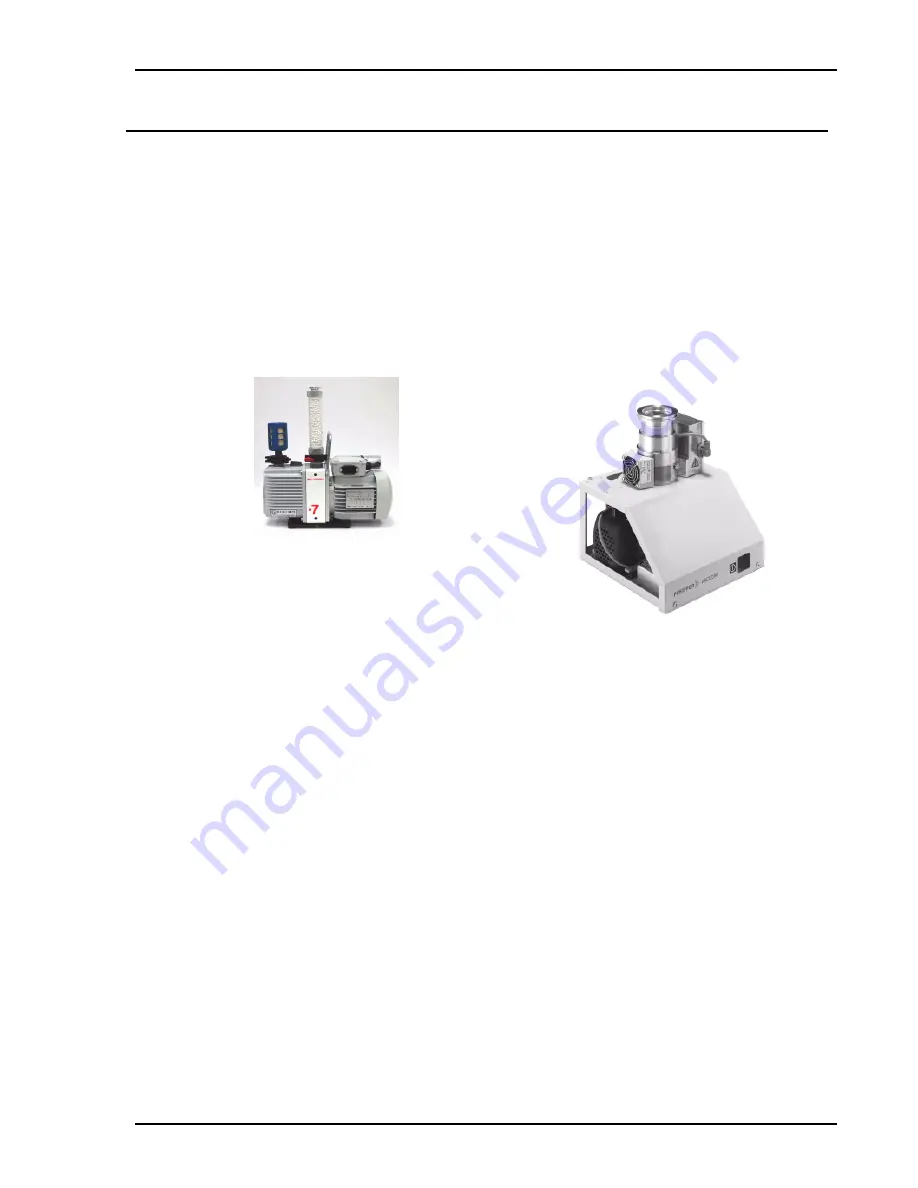
Gemini VII 2390 Confirm
Installing the Vacuum Pump
Feb 09 Gemini VII 2390 Confirm Installation Instructions and Checklist
5
Installing the Vacuum Pump
The Gemini requires an external vacuum system that meets these specifications:
Vacuum source achieving 20 x 10
-3
mmHg (or better) at the instrument inlet for oil-based or
oil-free pumps.
For oil-based pumps: an anti-suckback valve is required to prevent oil from being admitted
into the Gemini should there be a power failure. A device to reduce oil vapor backstreaming is
also recommended.
Two types of pumps are available from Micromeritics:
Use the appropriate instructions for the customer’s vacuum pump:
•
•
“High-Vacuum/Oil-Free Pump Combination” on page 16
•
“Non-Micromeritics Provided Vacuum Pump” on page 18
Oil-based pump
High-vacuum and oil-free pump combination