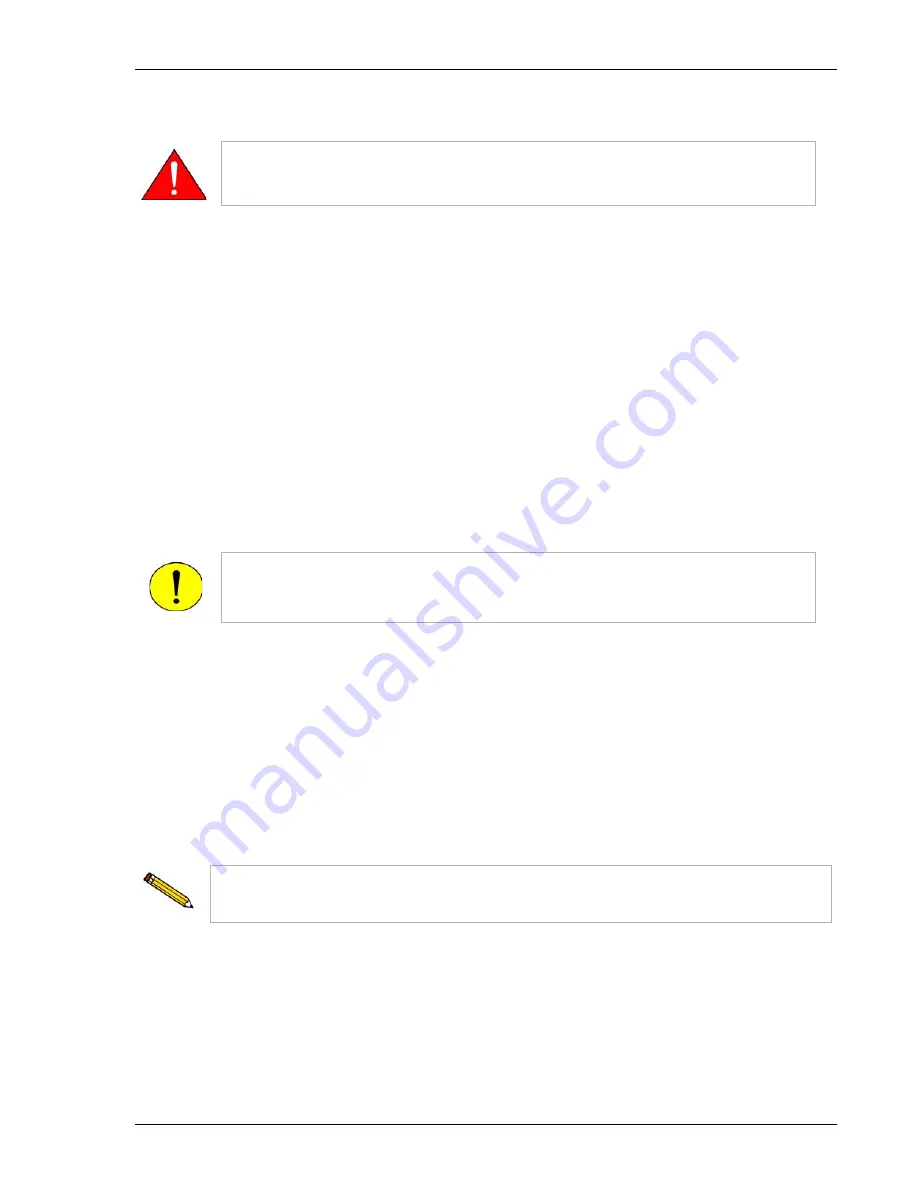
ASAP 2460 Operator’s Manual
Preventive Maintenance
246-42800-01 - Aug 2013
7-5
Checking and Cleaning the Analysis Port Dewars
Ice and suspended frost particles may accumulate in the bottom of an analysis port dewar. Particles or
deposits exceeding 1/4 in. (0.64 cm) in depth may jam between the bottom of the sample tube and the
bottom of the dewar, causing the dewar not to raise fully. Accumulations of fine particles impede liq-
uid nitrogen circulation around the bottom of the sample tube. This causes the sample temperature to
be slightly higher which, in turn, can cause pore volume measurement errors in those samples exhibit-
ing high isotherm slope above 0.97 relative pressure.
Accumulated ice is likely to melt and form a pool of water in the dewar if all liquid nitrogen evapo-
rates. The water must be removed; otherwise it will solidify when liquid nitrogen is added and could
press on the bottom of the sample tube causing breakage.
To ensure problems do not develop due to ice accumulation, check the dewar after each use. Clean
dewars on a weekly basis as follows:
1.
Remove the dewars and pour the liquid nitrogen from the dewars into an appropriate cryogenic
container.
2.
Rinse the dewars with warm water to melt any ice accumulation which may remain in the dewars
then dry thoroughly.
Replacing Analysis Port Filters
A porous metal filter is located in each analysis port. Using a contaminated filter on an analysis port
may extend the time required to achieve a vacuum at that port. More importantly, the contaminant may
adsorb or desorb during analysis, affecting the analysis results. A contaminated filter on an analysis
port may cause a leak test to fail (if the contaminant outgasses) or cause a free space reading to be
much lower than normal.
When handling dewars, be sure to observe the dewar precautions outlined in
Do not pour liquid nitrogen directly into a sink. Doing so may cause drain pipes to
burst.
Before removing and installing a port filter, ensure that the port valve is closed.
Observe the analysis system schematic to verify valve status.
Summary of Contents for ASAP 2460
Page 4: ......
Page 12: ...Table of Contents ASAP 2460 Operator s Manual viii 246 42800 01 Nov 2013...
Page 30: ...Using the Software ASAP 2460 Operator s Manual 1 18 246 42800 01 Aug 2013...
Page 93: ...ASAP 2460 Operator s Manual Generating Graph Overlays 246 42800 01 Aug 2013 2 63...
Page 94: ...Generating Graph Overlays ASAP 2460 Operator s Manual 2 64 246 42800 01 Aug 2013...
Page 202: ...Service Test ASAP 2460 Operator s Manual 4 36 246 42800 01 Aug 2013...
Page 230: ...Report Examples 2460 Operator s Manual 5 28 246 42800 01 Aug 2013 Isotherm Linear Plot...
Page 231: ...2460 Operator s Manual Report Examples 246 42800 01 Aug 2013 5 29 BET Surface Area Report...
Page 232: ...Report Examples 2460 Operator s Manual 5 30 246 42800 01 Aug 2013 BET Surface Area Plot...
Page 233: ...2460 Operator s Manual Report Examples 246 42800 01 Aug 2013 5 31 t Plot Report...
Page 236: ...Report Examples 2460 Operator s Manual 5 34 246 42800 01 Aug 2013...
Page 242: ...Service Test Mode 2460 Operator s Manual 6 6 246 42800 01 Aug 2013...
Page 270: ...Calibrating the System ASAP 2460 Operator s Manual 7 28 246 42800 01 Aug 2013...
Page 276: ...Ordering Information ASAP 2460 Operator s Manual 8 6 246 42800 01 Aug 2013...
Page 278: ......
Page 280: ......
Page 374: ...Appendix C ASAP 2460 Operator s Manual C 50 246 42800 01 Aug 2013...
Page 398: ...Appendix F ASAP 2460 Operator s Manual F 18 246 42800 01 Aug 2013...
Page 412: ...Index ASAP 2460 Operator s Manual Index 8 246 42800 01 Aug 2013...
Page 413: ...ASAP 2460 Operator s Manual Appendix G Aug 2013 SVP 1 SVP Smart VacPrep Operator Manual...
Page 414: ...Appendix G ASAP 2460 Operator s Manual SVP 2 Aug 2013...
Page 422: ...Contact Us vi Smart VacPrep Operator Manual...
Page 432: ...2 About the Software 2 4 Smart VacPrep Operator Manual...
Page 466: ...8 Error Messages 8 4 Smart VacPrep Operator Manual...