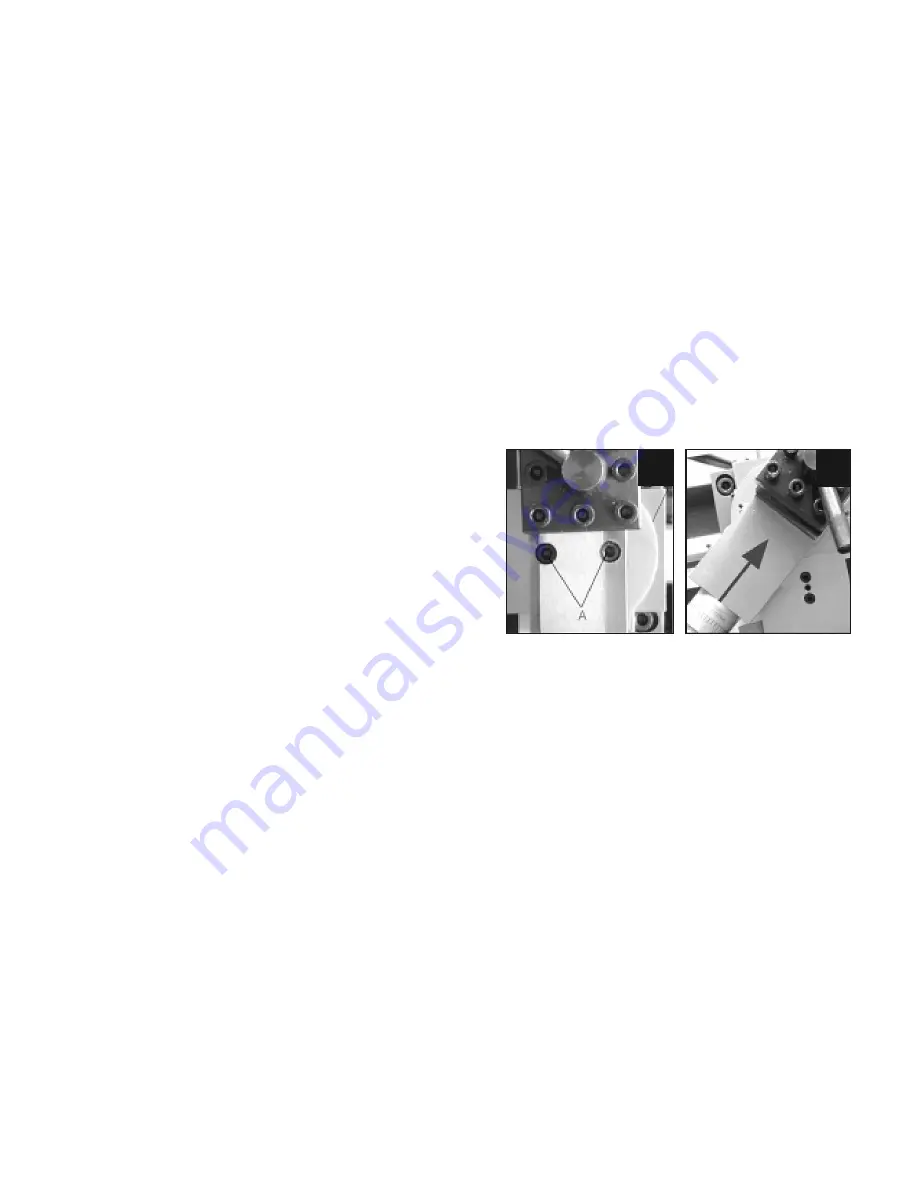
9
B. Simple Turning With Power Feed
The same basic setup is used as described previously, except that, before starting, the lead screw F/N/R Lever (on the rear of headstock) is set to
the “Forward” position and the auto feed lever (15) is operated in order to drive the carriage/saddle. As mentioned previously, the rotational speed
of the lead screw, and hence the rate of feed of the tool, is dependent upon the gear configuration of the gear train. The feed rate for normal turning
is considerably less than that used for screw cutting.
The lathe is factory-configured for normal turning; however, if you have been screw cutting, always remember to reset the gear configuration to that
for normal turning. Please refer to the chart on a later page which shows the gear configuration and an explanation of how to change the gears.
1. Taking all precautions previously mentioned, position the cutting tool a short distance to the right of the workpiece with the
appropriate depth of cut set on the cross-slide.
2. Ensure the lead screw F/N/R lever is set to “Forward” and select “Forward” on the Forward/Reverse switch on the main control panel.
Switch on the machine.
3. Turn the knob to achieve your desired spindle speed with your right hand and push down on the auto feed lever until the nut becomes
firmly engaged with the lead screw.
IMPORTANT: Your left hand should always be free in order to hit the emergency stop should it become necessary.
4. Carefully observe the movement of the tool and as it approaches the mark on the surface (denoting the end of cut), pull the auto feed
lever UP sharply and ensure it stays UP. If a degree of accuracy is required, it is recommended that you finish the cut by hand.
NOTE: If you require a shoulder with perfectly clean corners, then you need to use an appropriately shaped tool.
5. Retract the tool one or two complete turns on the cross-slide feed. Then crank the carriage/saddle so that the tool is at the start point
once again. Advance the tool the same number of turns, plus the depth of cut, and when ready, push down the auto feed lever and
proceed to take another cut.
C. Bevel Cutting
Bevel cutting involves the use of the compound slide, which is mounted on the
cross-slide and set at right angles to it (indicated by the zero mark on the body
of the cross-slide) for all normal cutting operations.
To set the compound slide so that the cutting tool will cut a bevel, first retract
the slide until the two socket head screws (A) are revealed as shown in fig. 7.
Loosen the screws sufficiently to allow the compound slide to be turned to the
desired angle, as indicated on the scale, and secure the slide in this position by
retightening the socket head screws.
The taper, or bevel, is cut by setting the cross-slide appropriately, then using the
compound slide feed handle to advance the cutting tool in the direction of the arrow as shown in fig. 8.
D. Screw Cutting
This operation requires a degree of skill and accuracy, and should not be attempted unless you are completely familiar with all aspects of the lathe.
Essentially, the carriage/saddle will move towards the headstock under power, the same as cutting with auto feed, except the rate of feed is greater,
as determined by the gear configuration. The cutting tool, therefore, is moving ever closer to the rotating chuck. Great care and concentration must
be exercised to ensure that the two do not meet when the machine is operating, as the damage caused would be disastrous.
The lathe is supplied with a lead screw that will produce imperial threads in a range from 12 to 52 threads per inch. It is important to remember that
the type of thread you need to cut (i.e., UNF, BA, BSP, BSW, etc.) will be totally dependant upon the cutting tool profile, as profiles differ from thread
to thread. For detailed information regarding screw cutting techniques, cutting tools, etc., you should consult a suitable handbook or obtain advice
and/or training from a qualified person.
The general procedure for screw cutting is as follows:
1. Try to get as much distance from the chuck to the end of the proposed screw thread as possible. If your design allows, cut a “run-off”
into the work piece which is of a smaller diameter than the root diameter of the proposed screw thread.
2. Install the appropriate gears for the thread required, and correctly mount the cutting tool. Set your required depth of cut, and position
the tool ready to begin cutting.
Note: Depth of cut is vitally important and may be calculated or obtained from an appropriate reference manual.
3. Take all necessary precautions previously stated, and start the machine with the automatic feed lever in its disengaged position (UP).
4. Engage the auto-feed lever sharply, turn the Forward/Reverse (F/R) switch to “Forward.” As the tool approaches the end of the
desired thread, push down on the red button that has been revealed under the emergency button to stop. Do not disengage the auto-feed lever.
5. Retract the tool using the cross-slide feed handle, noting the exact position on the scale and the exact number of turns. Turn the switch
to “Reverse”, then press the green button and the carriage/saddle winds back to the beginning and press the red button again. Now
change the Directional Switch to Forward. Restart the tool by winding IN the cross-slide the exact number of turns previously wound
OUT and then continue to wind IN the to the desired depth of cut. Press the green button to begin again.
6. Repeat as required in this manner until the thread is completed.
8
7