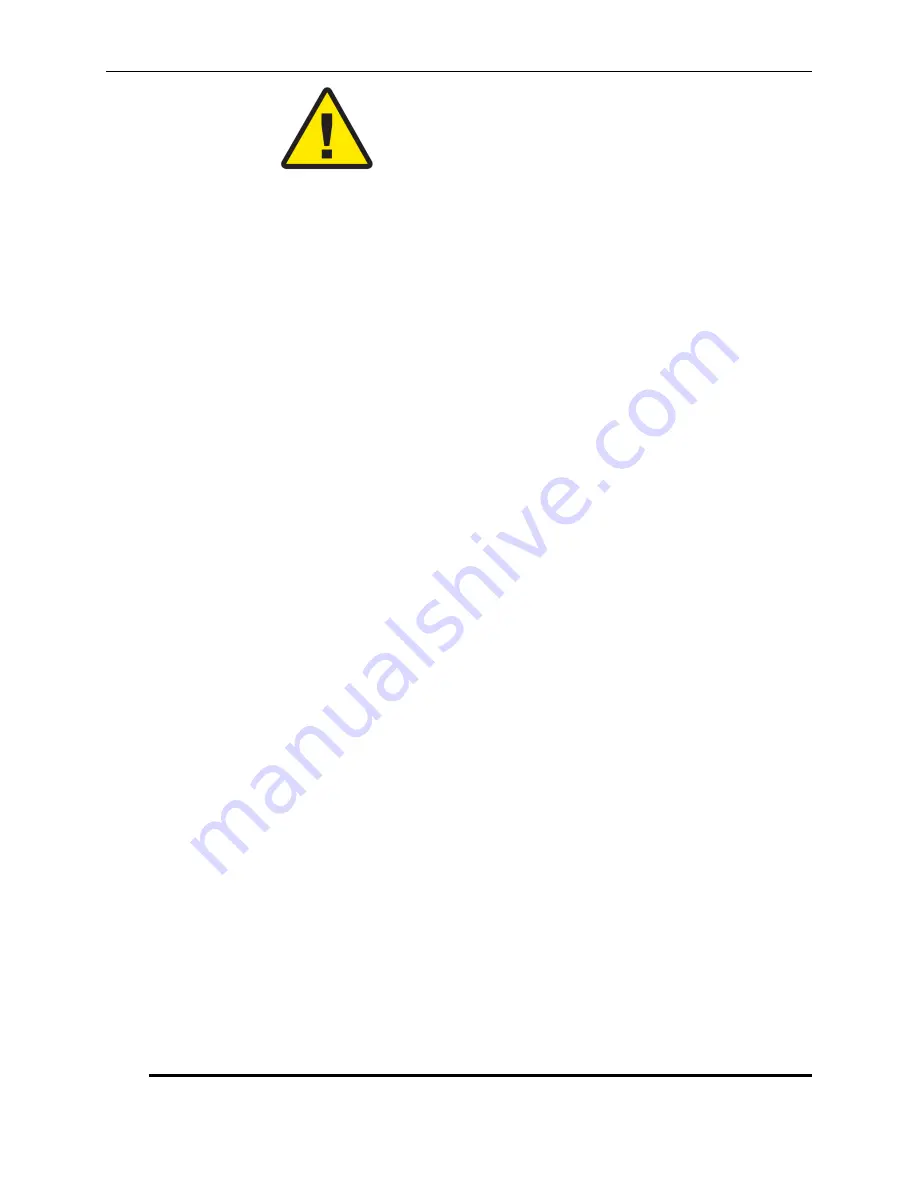
microcanner MC1000
MC FLEX (V1.0)
Page
2 of 19
WARNING!
OPERATING AUTOMATED EQUIPMENT IS DANGEROUS. DO NOT OPERATE
THE MC1000 CANNING SYSTEM UNTIL YOU HAVE READ THIS MANUAL AND
HAVE RECEIVED PROPER TRAINING. PRECAUTIONS MUST BE TAKEN TO
SAFEGUARD OPERATORS. OPERATORS MUST BE TRAINED AND AWARE
OF DANGER POINTS, IF SOMEONE FAILS TO FOLLOW SAFETY RULES,
INJURY OR DEATH COULD RESULT.
IMPORTANT SAFTEY PRACTICES
•
Conveyors are dangerous and present entanglement hazards. Loose clothing,
hair, and jewelry should be avoided at all costs. Never place hands near or
inside of a moving conveyor.
•
NEVER permit children, or un-trained operators anywhere near an operating
machine.
•
In the event of an emergency, hit the E-stop.
•
Never preform adjustments without being in E-Stop mode, or unplugging.
•
Never plug into an outlet that is not GFCI. Water and electricity do not mix.
•
Never open the control panel while powered up / plugged in.
•
Keep clear of all moving parts.
•
Clear machine jams only when in E-stop mode or fully powered down.
•
It is recommended that you wear safety glasses anytime during operation of the
MCFLEX canning system.
•
Never transport the MC FLEX while on its base. This is only for brewery mobility.
The frame may fail under shock loads of the road.