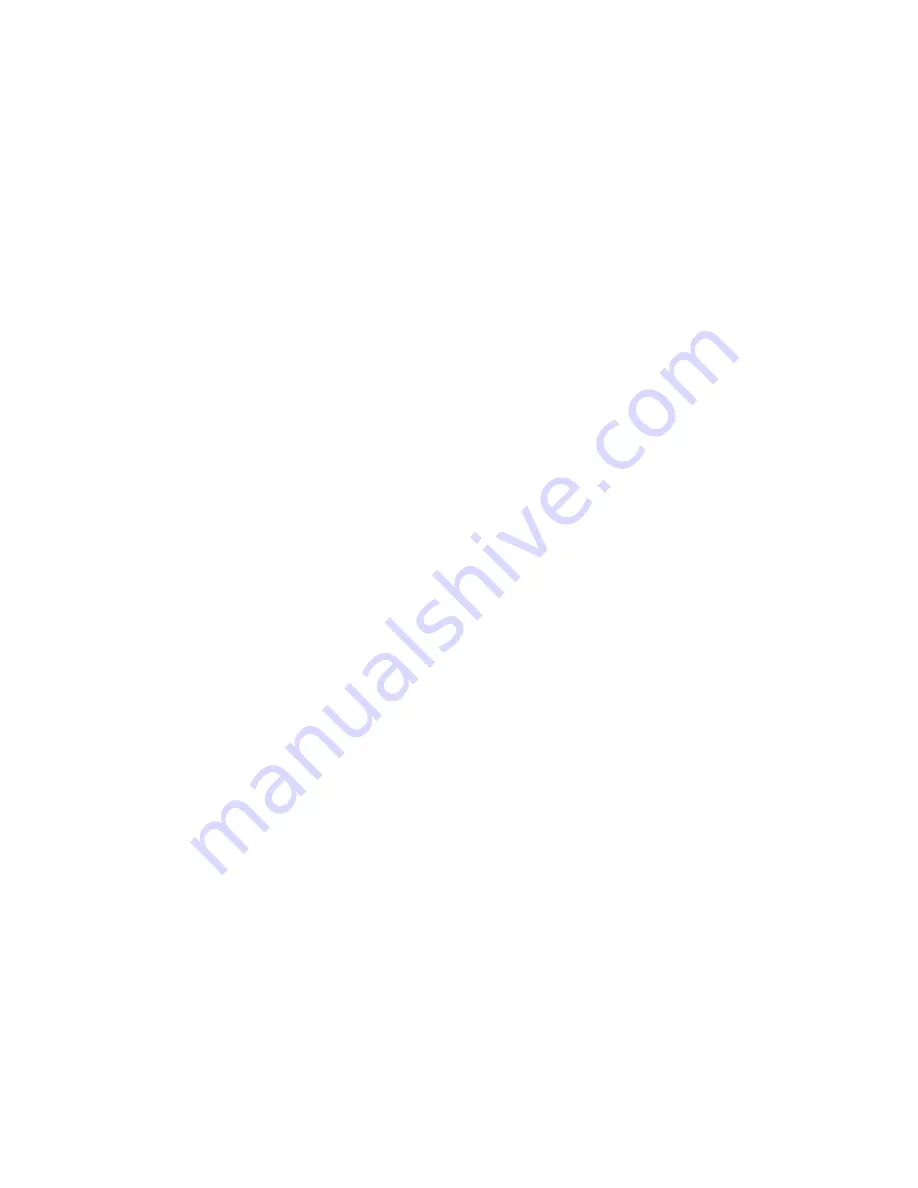
MHS Boilers Ltd ©
011204
17
for each group (BM). The boiler is then directly weather-dependently controlled.
KKM option
This is a boiler cascade manager permitting up to eight boilers to be switched in cascade. The
KKM also has the same possibilities as the E6 option.
Connection terminals
The operation of the appliance can be influenced by externally generated signals applied to the
appropriate terminals.
Terminal Description
L1
-
N-PE
Boiler power supply; must be fused at 10 A.
8 - 9
Domestic hot water primary pump control. This output provides a voltage (230 V)
when the boiler is operational as a result of a domestic hot water heating demand.
10 - 11
Boiler enable (240 V). Requiring a Volt Free switch. When these terminals are
connected the primary pump will be started and the boiler will be enabled. When there
is an open circuit between them the boiler will be shut down.
The pump will also stop after the set run on time. These terminals can be used,
among other things, for setting the boilers to standby during the summer months
whilst continuing to provide domestic hot water priority.
12 - 13
Operating signal. (240 V) The operating is removed if a fault has occurred more than
2 times within 6 minutes (the fault code will appear in the display with a “3”) or if a
fault is longer than 6 minutes active.
14 - 15
Control voltage for an external gas valve. This output begins to provide 240 V
before the boiler starts up; the voltage ceases after the boiler shuts down. This
output can be used to open hydraulic valves or to operate boiler room ventilation.
16 - 17
Calorifier thermostat (240 V). When these terminals are interconnected the boiler
will try to provide the set flow temperature programmed for the boiler.
This input
only functions if terminals 34 - 35 are interconnected.
18 - 19
Interlock input (240 V). If the connection between these terminals is interrupted,
the boiler will be deactivated and wait until the connection is restored (after 6
minutes or if the same fault has occurred three times within 6 minutes, this input
will be interlocked).
20 - 21
Lockout input (240 V). If the connection between these terminals is broken the
boiler will enter the fault mode. Reinstate the connection and press the reset
push-button.
30 - 31
External sensor*. After a suitable sensor has been connected it will be automatically
recognised when the power supply is switched on.
32 - 33
Low velocity header sensor*. This sensor can measure the temperature of a low
velocity header.
Summary of Contents for Ultramax 115
Page 26: ...MHS Boilers Ltd 011204 26 5 4 2 2 Pump characteristics...
Page 44: ...MHS Boilers Ltd 011204 44...
Page 45: ......
Page 46: ......