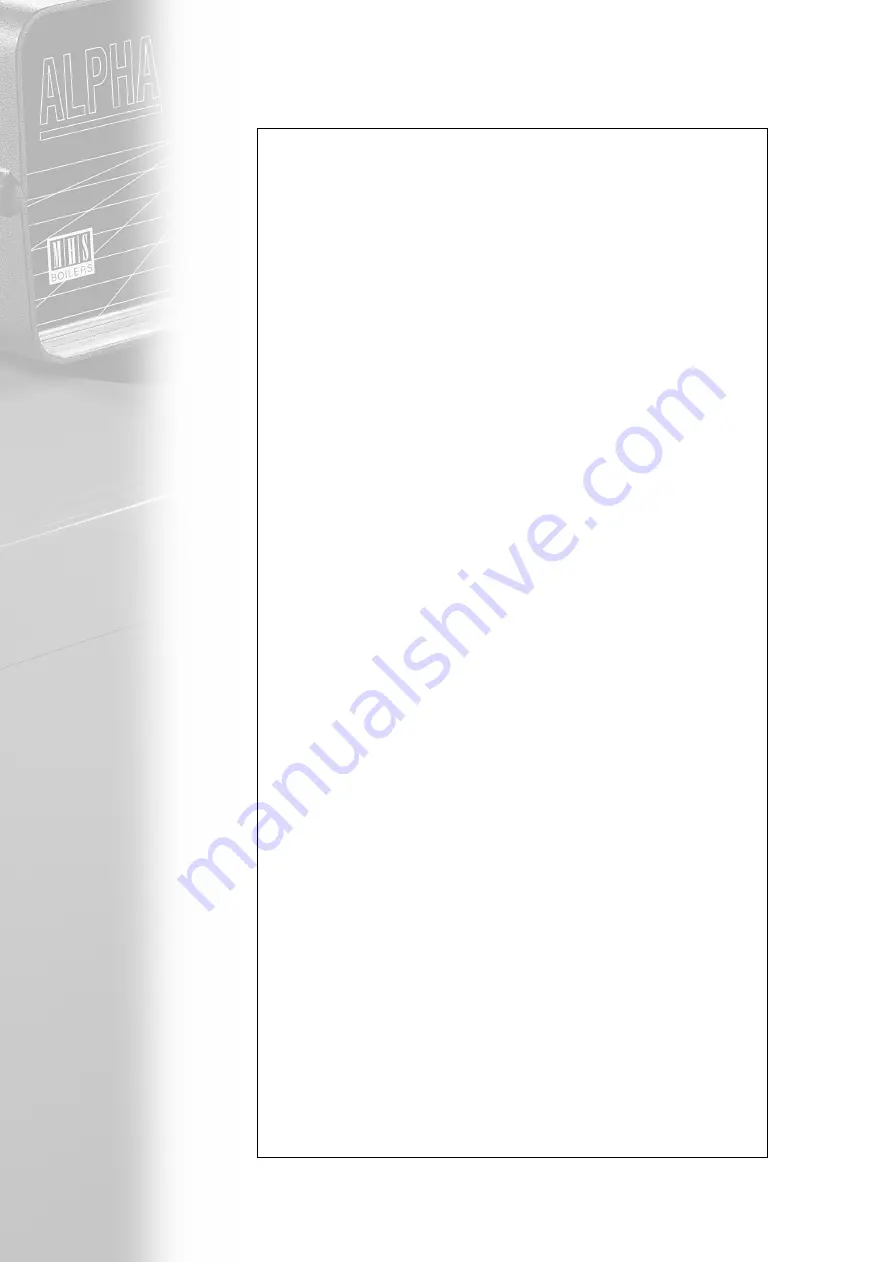
2
ALPHA 700
contents
page
section
3
. . . . . . . . . . .
1.0
General Notes
2.0
Product Description
4
. . . . . . . . . . .
3.0
Key Points
5
. . . . . . . . . . .
4.0
Specification for Alpha 700
5.0
Delivery
6
. . . . . . . . . . .
6.0
Single Boiler Dimensional Data/Clearances
7.0
Installation Requirements
7
. . . . . . . . . . .
8.0
Air Supply & Ventilation
9.0
Boiler Base
10.0
Clearances
8
. . . . . . . . . .
11.0
Technical Data
9
. . . . . . . . . .
12.0
System Schematic Using Reverse/Return
13.0
System Schematic Using Diverter Valves
10
. . . . . . . . .
14.0
Minimum Water Flow Rate
15.0
Circulating Water
16.0
Flue Systems
11
. . . . . . . . .
17.0
Control Panel
12
. . . . . . . . .
17.0
Standard Boiler Control Panel Electrical Diagram
13-17
. . . . . . .
18.0
Boiler Installation
18
. . . . . . . . .
19.0
System Connections
19
. . . . . . . . .
20.0
Mounting The Burner
21.0
Controls
22.0
Commissioning Procedures
20
. . . . . . . . .
23.0
Initial Lighting
24.0
Adjustment & Safety Checks
21
. . . . . . . . .
25.0
Boiler Servicing
22
. . . . . . . . .
26.0
To Turn On The Appliance
27.0
To Turn Off The Appliance
23
. . . . . . . . .
28.0
Fault Finding
24-25
. . . . . . .
29.0
Boiler Log
26
. . . . . . . . .
30.0
Service Repair Record Sheet
27
. . . . . . . . .
31.0
Spare Parts