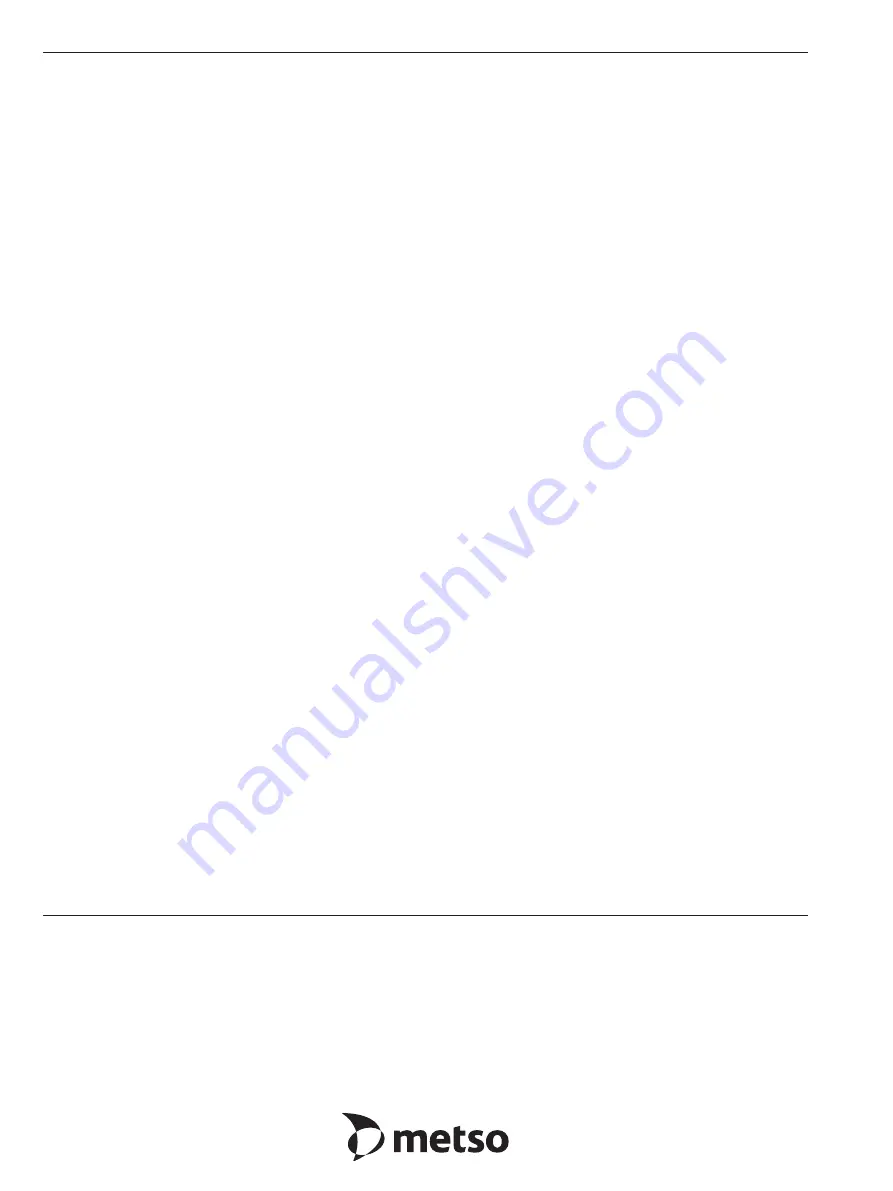
Subject to change without prior notice.
Metso Flow Control Inc.
Europe, Vanha Porvoontie 229, P.O. Box 304, FI-01301 Vantaa, Finland. Tel. +358 20 483 150. Fax +358 20 483 151
North America, 44 Bowditch Drive, P.O. Box 8044, Shrewsbury, M A 01545, USA. Tel. +1 508 852 0200. Fax +1 508 852 8172
South America, Av. Independéncia, 2500-Iporanga, 18087-101, Sorocaba-São Paulo, Brazil. Tel. +55 15 2102 9700. Fax +55 15 2102 9748
Asia Pacific, 238B Thomson Road, #17-01 Novena Square Tower B, Singapore 307685. Tel. +65 6511 1011. Fax +65 6250 0830
China, 11/F, China Youth Plaza, No.19 North Rd of East 3rd Ring Rd, Chaoyang District, Beijing 100020, China. Tel. +86 10 6566 6600. Fax +86 10 6566 2583
Middle East, Roundabout 8, Unit AB-07, P.O. Box 17175, Jebel Ali Freezone, Dubai, United Arab Emirates. Tel. +971 4 883 6974. Fax +971 4 883 6836
www.metso.com/valves
8
IMO-R28 EN
7.
TESTING
Metso recommends certifying each valve with a gas seat
and shell leak tests after rebuilding. Repair facilities may
use the facility standard test or customer specified leak test
procedure. In the absence of a local standard or customer
specified leak test procedure, Metso recommends the
following test procedure.
7.1
General
7.1.1 Test fixtures
-
Metso recommends stainless steel test fixtures to
prevent contamination from corrosion particles.
- Tank car side fixture is a flange that dimensionally
matches the tank car mounting interface on which the
valve will be installed.
- Outboard fixture is a flange or fixture that seals against
the outboard valve interface.
- Test fixtures, hoses, fittings etc. shall be clean to prevent
introducing debris during testing.
7.1.2 Gaskets
-
Metso recommends testing with same gasket that
will be used to install the valve on the tank car. (Use of
non-standard gaskets or o-ring fixtures, may lead to
erroneous results.)
7.1.3 Media
- Test media shall be clean dry Nitrogen or clean dry
compressed air.
7.2
Shell Test
7.2.1
Mount the tank car side and Outboard pressure
test fixtures with appropriate gaskets.
7.2.2
Place the ball in the ½ open position and pressurize
the valve body to 100 PSIG from the tank car side
fixture.
7.2.3
Apply leak detection fluid (Sherlock®, Snoop®,
etc.) to the outside of the valve and the gland
packing. Observe the valve for leakage, in the
form of continuously forming bubbles or foam, for
2 minutes.
7.2.4
Adjust packing as needed to seal any leakage.
7.3
Seat Test
7.3.1
After completing the Shell test, depressurize the
valve and remove the outboard pressure test
fixture.
7.3.2
Place the ball in the closed position.
7.3.3
Place water on the ball until the seat is covered.
7.3.4
Pressurize the tank car side to 30 psig and observe
the seat for bubbles that continue to form during
the 2 minute observation time.
7.3.5
NO LEAKAGE ALLOWED
7.3.6
Upon a Successful 30 PSIG test, increase the
pressure to 100 PSIG.
7.3.7
Check for leakage for 2 minutes at 100 PSIG.
7.3.8
NO LEAKAGE IS ALLOWED.