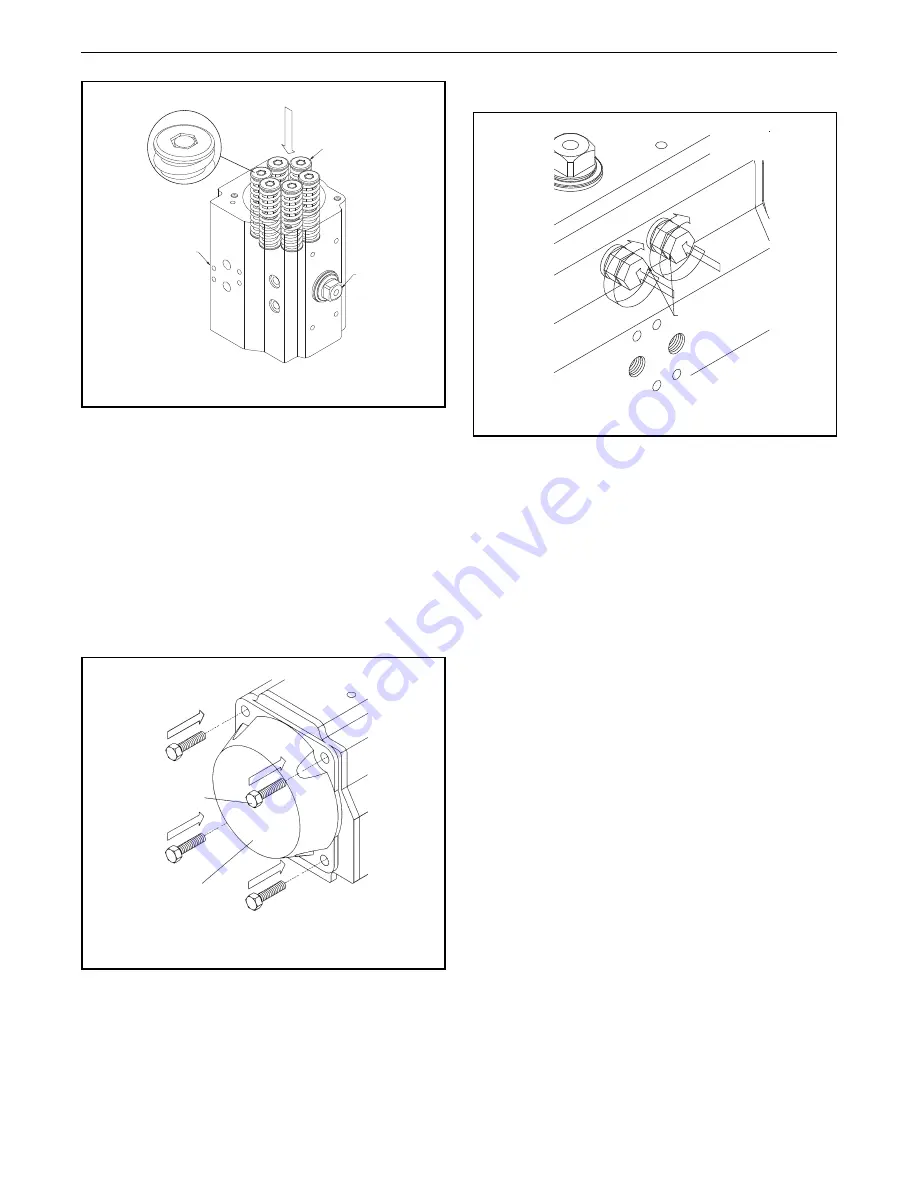
7
B. Apply silicone grease to the end-cap o-ring seals,
using the recommended o-ring-area grease listed
in
(Table 2)
. Fit the end-cap o-ring seals (14) into
the groove in each end cap (30, 31).
C. Fit the end caps (30, 31) onto the body (50),
verifying that the o-ring seals (14) remain in the
grooves.
D. Insert all end-cap screws (13) and hand tighten.
Complete tightening by following the sequence
indicated in
(Figure 16)
.
4. Assembly of Stop Screws (2) and Stroke
Adjustment. (Figure 17):
A. Insert the nut (4), washer (3), and o-ring (11) onto
the stop screws (2).
B. Screw the stop screws (2) into the body (50).
5. External Travel Stop Adjustment, (Figure 17):
The stop adjustment screw (2) to the right controls the
clockwise end of travel. The stop adjustment screw (2) to
the left controls the counter-clockwise end of travel.
A. Cycle the actuator/valve to the clockwise end of
travel and measure to determine if the valve is in
the proper position. (In most applications this
will be fully closed.)
B. If the valve is not in the correct clockwise position,
turn the right stop adjustment screw (2) IN to
reduce actuator travel, or OUT to increase actuator
travel.
C. When the correct clockwise position is obtained,
hold the adjusting screw (2) stationary while
tightening the lock nut (4).
D. Cycle the actuator/valve to the counter-clockwise
end of travel and measure to determine if the valve
is in the proper position. (In most applications
this will be fully opened.)
E. If the valve is not in the correct counter-clockwise
position, turn the left stop adjustment screw (2)
IN to reduce actuator travel, or OUT to increase
actuator travel.
F. When the correct counter-clockwise position is
obtained, hold the adjusting screw (2) stationary
while tightening the lock nut (4).
6. Position Indicator (19, 39) Assembly. (Figure 18):
A. Fit position indicator (19) on the shaft (60),
verifying that it indicates the correct actuator
position.
B. Tighten cap screw (39) to secure the position
indicator.
Figure 16
3
13
1
30, 31
4
2
Figure 17
2, 3, 4, 11
Figure 15
60
17
50