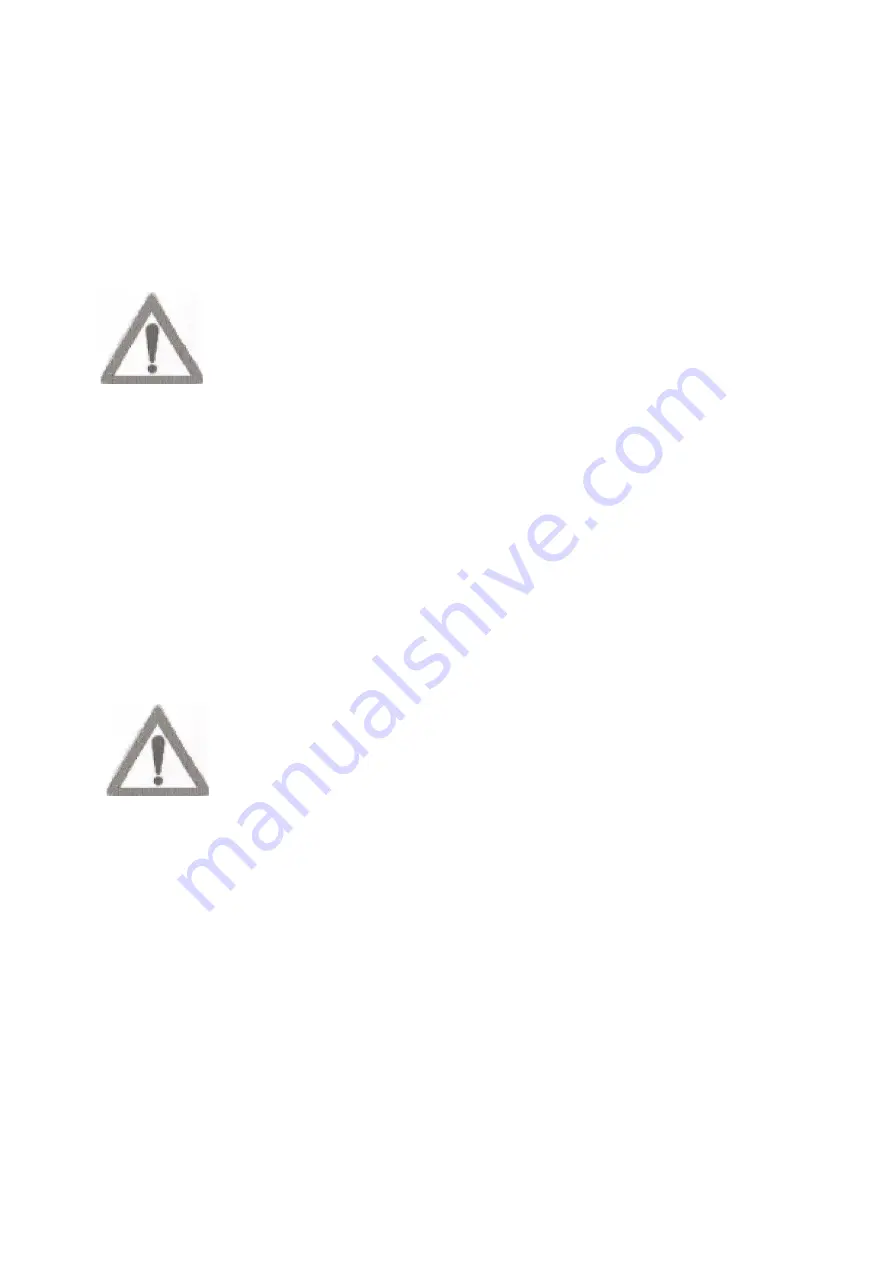
6
7. INSTALLATION OF SECURITY EQUIPMENT
Make sure that the brake is in the correct position during installation process. Loads that the brake will
stop downstream and upstream are different. The tip of the arrow on the brake should be upstream.
The brake has been adjusted in way that it can stop a load of (P + Q) downstream and that of Q/2
upstream. In the event that the direction of the brake is reversely placed, the security equipment cannot
stop the cab in case of a free fall.
The direction of the security equipment must definitely be installed in the correct
direction.
Please see that the pulley inside the block equally contacts to the rail in both sides by moving the
brake handle up and down. The brake handle remains in the middle of the block in the neutral position
of the brake, and inside the block the pulley is in a parallel position to the rail. In the movement of the
brake up and down, the pulley contacts by moving on the rail. Braking process stats following the said
contact. The tasks of the pulleys are to tighten the rail together with brake block fixed jaws and to
perform the braking process through pressure formation of the surfaces of the wheels onto the rail
surface.
It is necessary that the connection of the brake onto the suspension be completely made with the sizes
formerly specified and with M12 steel bolts. Brake blocks in both sides should equally be distant from
the rail and see the rail paddle in equal depths. This adjustment is compulsory in order that both sides
of the brake equally and synchronously activate. This case should be ensured by making suspension
skate adjustments. Otherwise, cases such as activation of one side of the brake blocks in advance or
one side’s holding the paddle occurs. This is an undesired condition in operation of the brakes. Brake
calculations have been made by assuming that both sides synchronously and equally hold.
Thus, distance adjustments should precisely be carried out and definitely
checked again prior to proceeding main operation.
In the event that any impropriety is detected in the tests performed before the elevator is taken into
operation, mounting distance errors than can lead to the said impropriety should be corrected. It should
be PAID ATTENTION that the guiding rails to be used are elevator springs complying with ISO 7465
standards. Friction values of materials used in the security equipment have been determined in
accordance with the properties of cold drawn and treated rails specified in the standard. In addition,
excessive lubricating and dirtiness that can occur on the rails cause these values to change. Thus,
excessive lubricating, dust, dirtiness etc should be prevented from forming on the rails.
No excessive lubricating should be done on the rails. In regular maintenances every month, whether
foreign matters exist inside of the brake block or not should be checked and corrosion formation
should be prevented. Reel seats should be checked in monthly maintenances and inside of the reel
seats should be cleaned during the 6 months or yearly maintenances.
Recovery of the cabin from the brake following the braking action should be performed by a qualified
personnel by moving it in contrary to the direction of the braking.