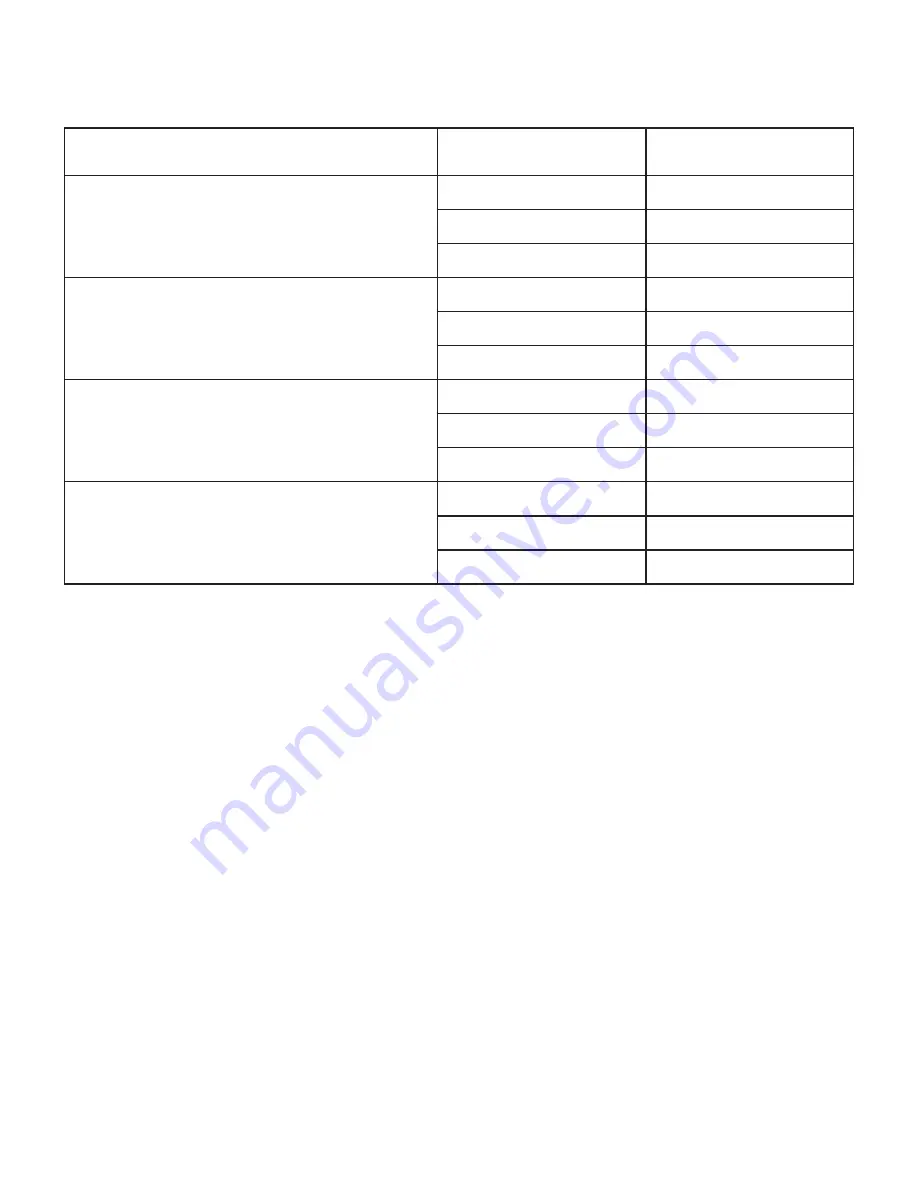
12
Depending on the humidity level and impurity conten
Humidity, %
Content of impurities, %
K2 Factor value
Up to 18 inclusive
5
1.0
10
0.9
15
0.8
Over 19 ‘22’
5
0.9
10
0.8
15
0.7
‘23’ ‘26’
5
0.8
10
0.7
15
0.6
‘27’30’
5
0.7
10
0.6
15
0.5
Table 5
The Metra Separator cleaning:
Before sending the Metra Separator to storage or preservation, it is necessary to perform cleaning and check fastenings
of the moving parts.
When withdrawing the Metra Separator from storage or preservation, it is necessary to remove dust and dirt deposits using
a soft cloth, check the smoothness of the impeller rotation and carry out maintenance of the motor.
11.1. Quick cleaning:
•
Switch on the Metra Separator, adjust the ‘Speed’ knob to the maximum possible value, open the ‘Feed Gate Control’
handle of the hopper, open the CDC (Cyclone Dust Collector) gate.
•
The Metra ADS Separator should run in this mode for 3-5 minutes.
•
Clean the waste trays, if necessary.
Quick cleaning should be made no less than once per shift.
11. MAINTENANCE
Summary of Contents for ADS-200
Page 1: ...1 OPERATING MANUAL GRAIN CLEANER METRA ADS...
Page 17: ...17 Metra Separator strapping scheme Annex 1...
Page 18: ...18...