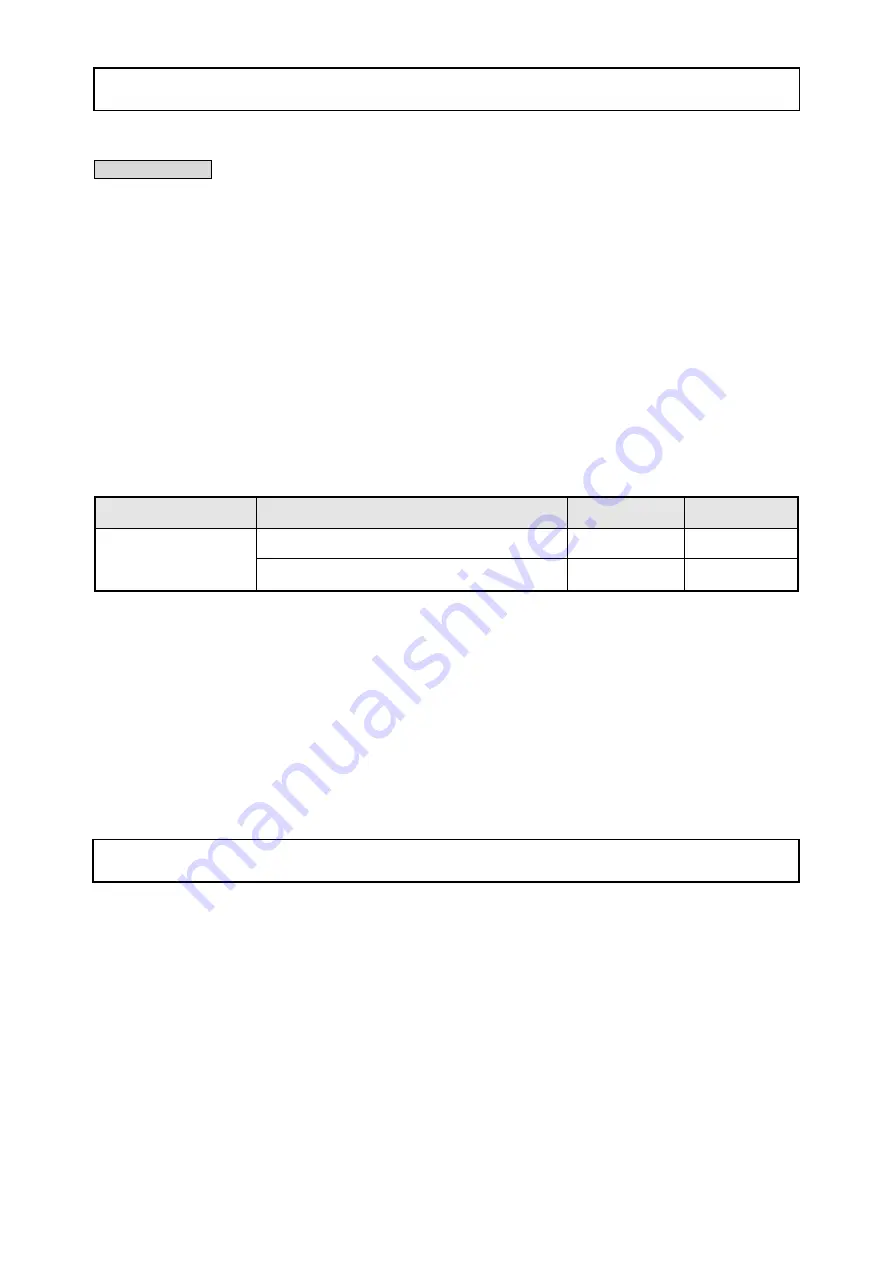
-8-
Apply specified amount of grease to the following portions.
Grease (SEP-3A)
• Surface of the Base Ass’y
[54]
where Liner (A)
[52]
slides ·································· 5 g
• Surface of Shaft (B)
[55]
where the Turn Table
[25]
slides ··································· 0.5 g
• Surface of the Turn Table
[25]
where Liner (A)
[52]
slides ··································· 3 g
• Pinion of the Rotor Ass'y
[100]
and tooth surface
and gear chamber of the Spindle Ass'y
[75]
··················································· 15 g
• Surface of Shaft (D)
[10]
·············································································· 1 g
• Surface of the O-ring (P-6)
[15]
of the Stopper Pin Ass'y
[14]
······························ 0.2 g
• Surface of the Hinge
[13]
where the Turn Table
[25]
slides ·································· 2 g
• Surface of the Gear Case
[2]
where the Hinge
[13]
slides (grease chambers) ········· 5 g x 2 places
• Inside of the Spring
[5]
················································································ 5 g
• Surface of the Hinge
[13]
where Shaft (C)
[12]
slides ········································· 1 g
• Sliding surface of the Link
[89]
······································································ 0.2 g
Please purchase the following grease as necessary.
Item
Registered part name
Net weight
Code No.
Grease (SEP-3A)
Grease (SEP-3A) (100 g)
100 g
930035
Grease (SEP-3A) (2.5 kg)
2.5 kg
930038
Advise the customer to lubricate the machine as indicated below at least once a month. Prior to lubrication,
any sawdust, dirt or other foreign matter should be thoroughly wiped away with a soft cloth.
(1) Swiveling section of the Gear Case
[2]
and Hinge
[13]
Coat the swiveling and sliding portions of the Gear Case
[2]
and the Hinge
[13]
with machine oil.
(2) Vise ass’y section
Coat the screw thread portion of the Knob Bolt M10 x 66
[35]
of the Vise Ass’y
[33]
with machine oil.
(3) Swiveling section of the Turn Table
[25]
and Hinge
[13]
Coat the swiveling and sliding portions of the Turn Table
[25]
and Hinge
[13]
with machine oil.
1. Checking after reassembly
• Check that the motor section can be moved up and down smoothly by holding the handle portion of the
Switch Handle Set
[106]
with operating force 58.8 N {6.0 kgf} max.
• Check that the Turn Table
[25]
can be rotated to the left and right smoothly by holding the Side Handle
[26]
with operating force 34.3 N {3.5 kgf} max. while the index stopper is released by pushing down the
Spring Plate
[29]
.
• Check that the Lower Guard
[90]
moves smoothly and properly.
• Check that the Off Lock Lever
[113]
and Trigger
[110]
operate smoothly and properly.
• Check that the motor does not start by pulling the Trigger
[110]
without moving the Off Lock Lever
[113]
of
the Switch
[114]
(switch operating force:100 N {10 kgf}).
• Check that LED
[84]
turns on and off by pushing the LED button.
• Check for braking (blade stopping time: 5 seconds max.)
• Check that the rotating direction of the spindle is the same as the arrow mark on the Gear Case
[2]
.
Lubrication points and type of lubricant
Checking and adjustment after reassembly