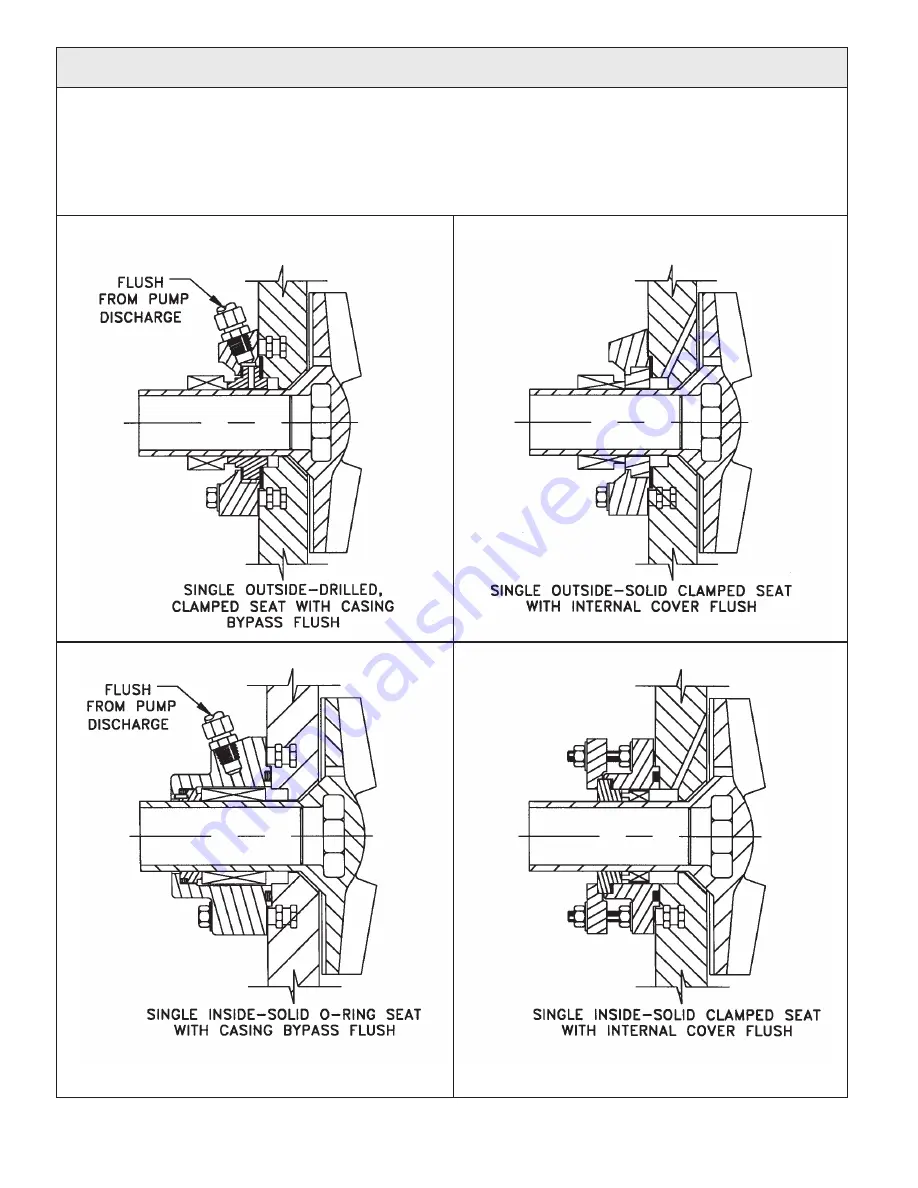
6
17
1530 series seal aNd stuFFiNg box arraNgemeNts
PRODUCT FLUSH:
A portion of the pumped fluid is recirculated through the
stuffing box to provide lubrication and cooling to the seal.
Use plastic fittings only.
electrical coNNectioNs
A) All electrical work done to the unit should be
done by a qualified electrician. All local, state and
federal electrical codes should be adhered to.
B) Wire motor according to motor manufacturers
instructions. Ensure that all connections and
covers are tight and that proper sized wire and
switch-gear are used.
C) All pumps operate in a clockwise direction
when viewed from the motor end, (see
direction arrow on the pump motor adapter).
Connect electric motor to power supply and jog
motor to check rotation. If motor is operating
in wrong direction, reverse leads and recheck.
WarNiNg: do Not start pump With
liQuid iN the casiNg uNtil motor
rotatioN has beeN determiNed as
damage could result From
sustaiNed reVerse rotatioN uNder
pumpiNg load.