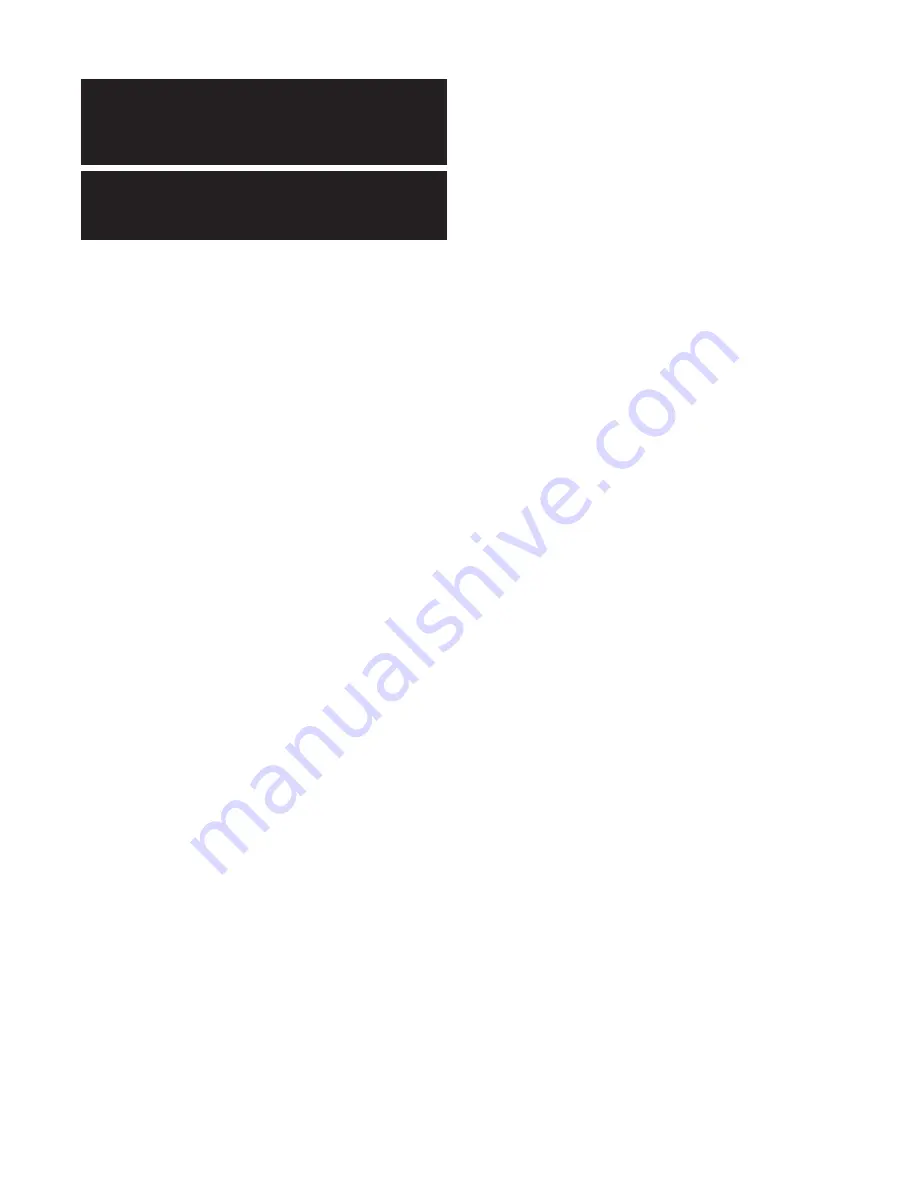
– 5 –
D. Electrical Connections
WARNING: Open all disconnect switches and
secure in that position before wiring unit.
Failure to do so may result in personal injury or
death from electrical shock.
WARNING: Controls must be protected from
water. Do not allow water to drip on the ignition
system.
NOTE: Before installing any wiring, check the unit
rating plate for supply power rating.
All electrical connections must conform to the current
edition of: ANSI/NFPA No. 70 National Electrical Code
and applicable state and local codes.
Entry location for all field-installed and control wiring is
through the control panel.
If optional disconnect is not furnished with the unit, the
field provided disconnect must be of the proper size
and voltage. Refer to unit rating plate for minimum
circuit ampacity and voltage. The disconnect must be
installed in accordance with Article 430 of the current
edition of ANSI/NFPA No. 70 National Electrical Code.
Check the supply voltage before energizing the unit.
The maximum voltage variation should not exceed
± 10%.
NOTE: Should any original wire supplied with the
unit have to be replaced, it must be replaced with
wiring material having a temperature rating of at
least 105° C.
E. Field Piping
CAUTION: To prevent water damage to building
and equipment piping, drain and vent plugs must
be installed.
NOTE: All field-installed piping must conform to
applicable codes.
Water Piping
All water piping must be in accordance with project
specifications and the requirements outlined in any ap-
plicable local, state, and national codes.
Insert a manual shut-off valve in the water supply line
required for the unit’s direct evaporative section. Com-
plete the piping to each section’s 3/8" make-up water
inlet.
NOTE: Soft water equipment should not be
attached to water lines going to the evaporative
cooler. "Soft Water" will cause corrosion and
decrease the effective life of the cooler.
Proper water quality and environmental conditions will
give you long service life from your direct evaporative
cooling unit. Significant deviation from “normal” conditions
may have a bearing on longevity of the equipment.
“Normal” circulating water chemistry falls within the follow-
ing limits:
• pH between 6.5 and 8.0.
• Chlorides (expressed as NaCl) below 750 ppm.
• Calcium (expressed as CaCO
3
) below 1200 ppm -
except in arid climates where the critical level for scale
formation may be much lower.
• Sulfates below 5,000 ppm – if calcium exceeds 1200
ppm, sulfates should be limited to 800 ppm (less in
arid climates) to prevent scale formation.
• Sulfides below 1 ppm.
• Silica (expressed as SiO
2
) below 150 ppm.
• Iron below 3 ppm.
• Manganese below 0.1 ppm.
• No organic solvents.
• No organic nutrients which could promote growth of
algae or slime.
• Chlorine (from water treatment) below 1 ppm free
residual for intermittent treatment, below 0.4 ppm free
residual for continuous chloration.
Insert a manual shut-off valve in the drain line from each
unit’s direct evaporative section’s drain.
NOTE: The direct evaporative section of every module
is provided with an adjustable bleed valve that is
plumbed to each section’s overflow stand pipe.
System drainage for the constant water bleed from
each evaporative section must be provided.
If units are provided with optional freeze protection and
automatic drain down kit, install the solenoid valves in the
following manner:
1. Install the normally closed and, if provided, the 1/2" or
3/8” normally open water fill line drain solenoid valve in
the water supply line at a point not subject to freezing
temperatures and complete the piping to the make-up
water inlet connection provided on each unit.