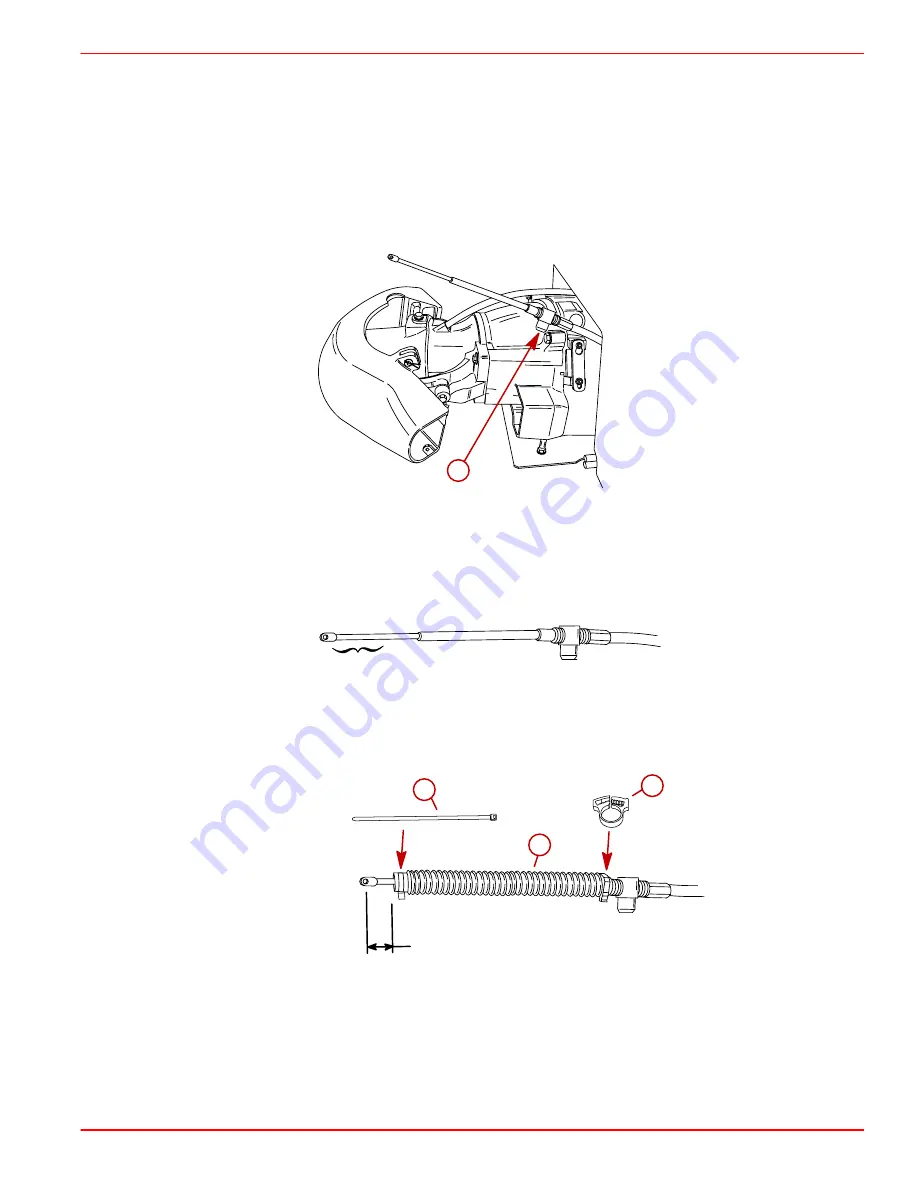
250 HP JET DRIVE INSTALLATION MANUAL
Page 23
90-10240040 DECEMBER 2003
Shift Cable Adjustment
IMPORTANT: The shift cable MUST BE properly adjusted. The shift cable is adjusted
so that the reverse gate is not pre-loaded against either the forward or reverse stop.
Pre-load in either position may cause failure of the stop and/or premature wear of the
shift cable or control box components. It may also cause stiffness of the throttle
control.
1. Thread the cable barrel onto the shift cable.
a
a -
Cable Barrel
2. Use a de-greaser and clean off all oil film from the area on the shift cable shown.
NOTE: Removing the oil film from the shift cable is necessary to prevent the bellows from
sliding on the cable.
a
a -
Remove Oil Film From This Area
3. Slide the bellows over the shift cable end. Position and install the bellows onto the cable
conduit as shown. Fasten ends with clamp and cable tie.
25.4 mm (1 in.)
a
b
c
a -
Bellows
b -
Clamp
c -
Cable Tie
Summary of Contents for 250 Jet
Page 46: ......