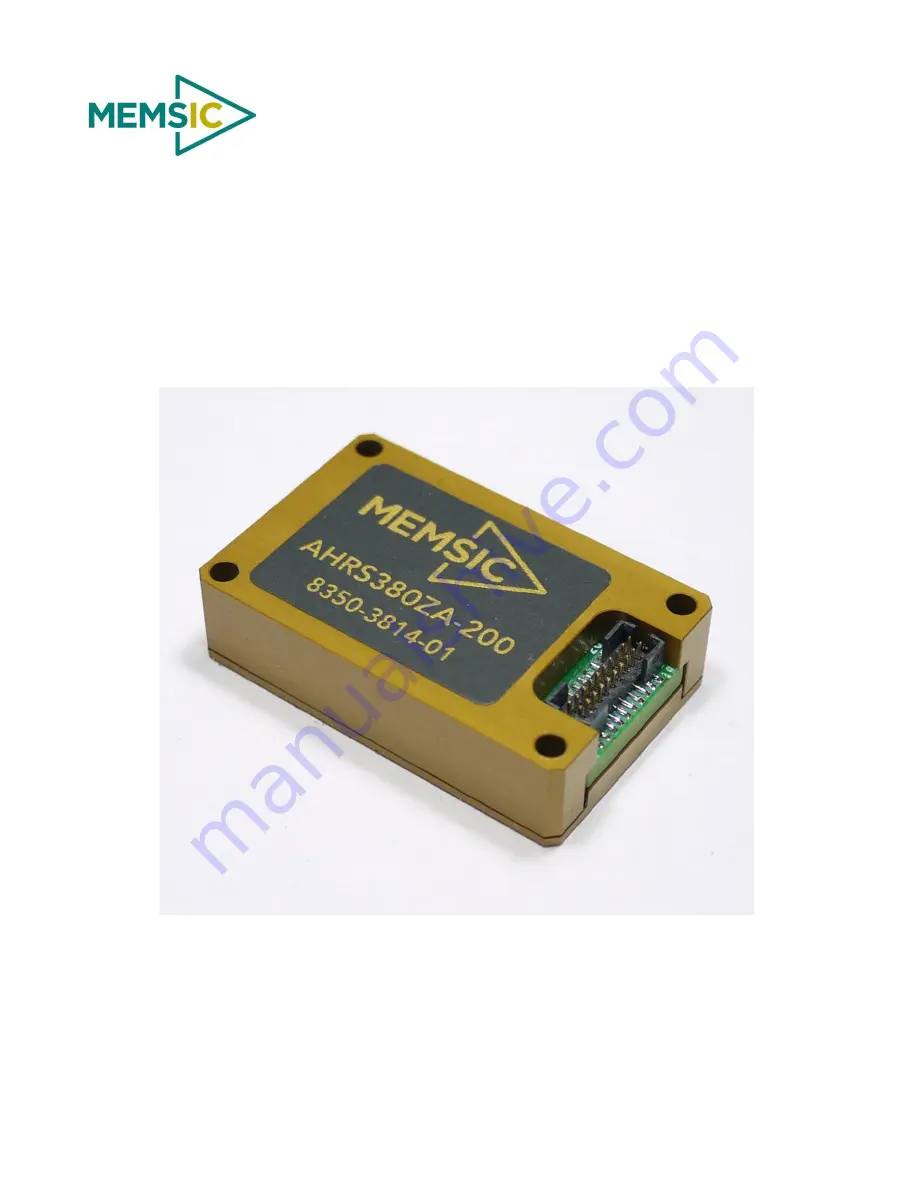
DMU380ZA Series
USER MANUAL
Document Part Number: 7430-3810-02
MEMSIC, Inc., 1759 McCarthy Blvd, Milpitas, CA 95035
Tel: 408-964-9700, Fax: 408-854-7702
email: [email protected], website: www.memsic.com
DMU380ZA Series
USER MANUAL
Document Part Number: 7430-3810-02
MEMSIC, Inc., 1759 McCarthy Blvd, Milpitas, CA 95035
Tel: 408-964-9700, Fax: 408-854-7702
email: [email protected], website: www.memsic.com