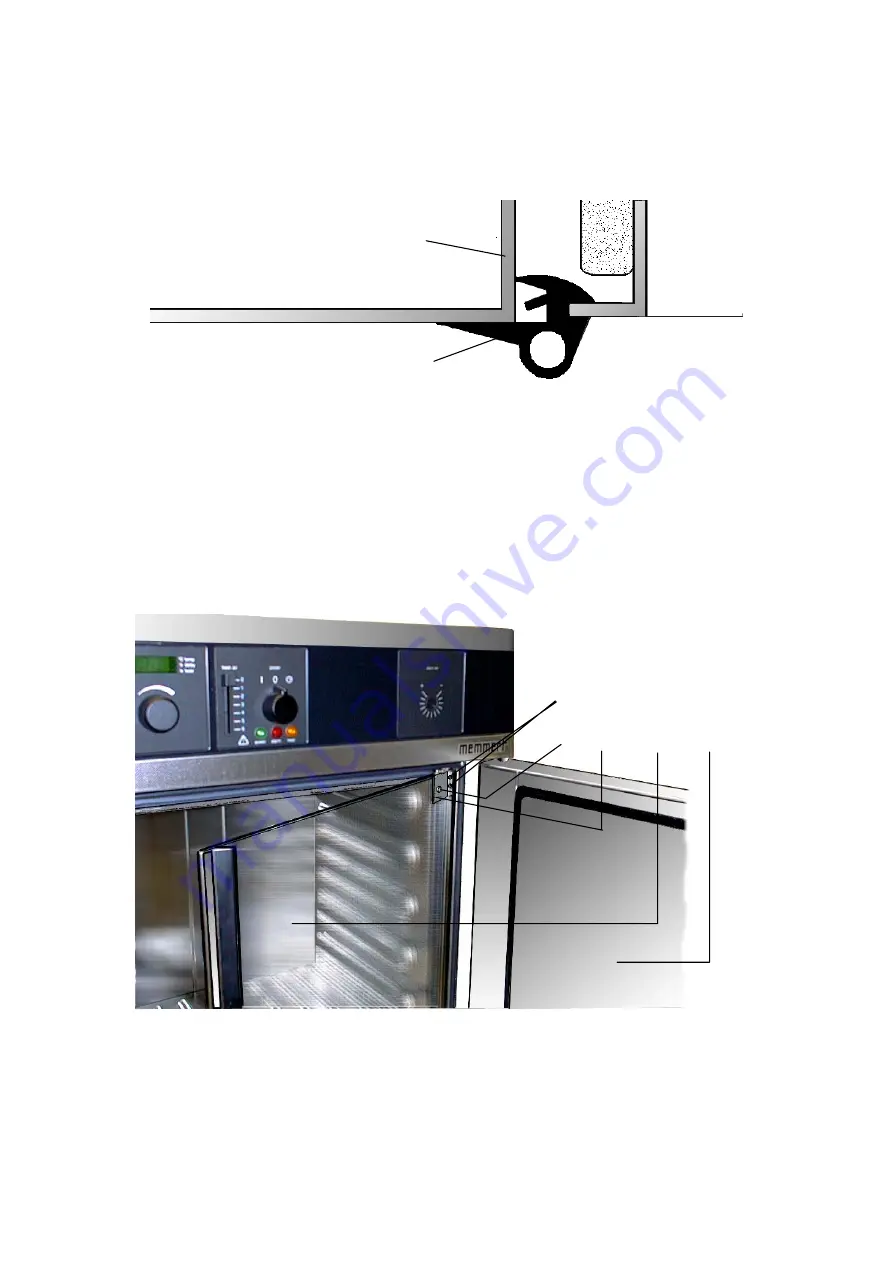
UE/BE 200-800, SE 200-400, ULE/SLE 400-800
UP/BP/ULP/SLP 400-800
13
13 Changing the seal of the working chamber
The seal of the working chamber can be pulled out after opening the door. The new
one can be fitted in according to the illustration.
The pre-cut seal should be inserted into the space without tension and then cut if
required.
14 Readjusting and dismantling the inner door on incubators BE / BP
Loosen the screws (3) (do not unscrew them completely, otherwise the fixing block at
the interior side will drop down).
Adjust the door and tighten the screws (3) again.
Check screw (4) and tighten it, if necessary.
Adjust the inner door closure, if required.
If a fixing block has dropped down, it will be accessible by pulling out the side parts
(see chap. 15) and can be mounted in position again.
For dismantling the glass door unscrew screw (4) (hold the nut at the opposite side with
spanner SW 13), tilt the glass door forward and lift it out of the lower door hinge.
Assemble in reverse order.
1 Door
2 Inner door
3 Screws for adjustment
4 Fixing screws (glass door)
5 Hinge for inner door (top)
Housing Post
Seal
Working
Chamber
3
4
5
2 1