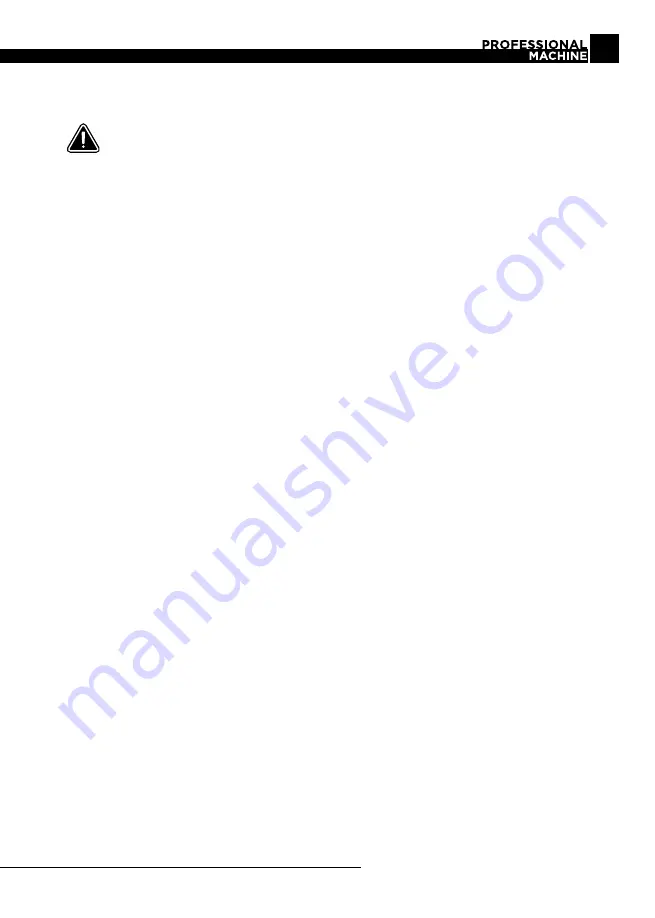
INSTALLATION AND USER MANUAL FOR STELLA COMBINE OVEN
I
25
Rules Required for Correct Machine Use
Manufacturer is not responsible for accidents and injuries caused by non-compliance with the
instructions.
•
Adjustment must be made by qualified and authorized personnel. Machine must be disconnected
from all energy sources during adjustment. All necessary safety measures should be taken in
exceptional cases.
•
Make sure that there is no risk of any waste before starting the adjustment process.
•
Always work in an environment with sufficient light.
•
Read the safety signs carefully and make sure you understand them.
•
Keep the outside of the machine, especially the burner part, clean and tidy.
•
Check all switches, safety devices and other control functions regularly before operating the
machine.
•
Device must be used by a qualified person who knows the safety and technical requirements and
has read the operating and maintenance manual.
•
The operator must wear suitable and light-tight clothing and clothing that is not likely to be
caught by the machine.
•
When loading products to the machine; the process must be done in accordance with the
manufacturer’s recommendations.
•
Do not move or clean any parts while the machine is running.
•
Immediately press the emergency stop button in case of danger.
•
Disconnect all power from the machine at the end of the working day.
•
Keep the control panel clean and tidy. If the control panel has been damaged, contact your local
dealer.
•
For details on cleaning the control panel, refer to the information in the. Maintenance and
Cleaning part.
•
The machine must not be used outside of its intended use.
Pre-Operation Control Areas
•
Operator must stand front of the oven during loading and unloading.
•
Check the operation of the steam aspirator.
•
Check the operation of the circulation fan.
•
Check the cooking cell cover for leaks.
•
Do not allow the cover glass to come into contact with water when it is hot.
•
Take precautions to prevent leaks and blockages in the fuel hoses in natural gas operated Stellas.
•
Take precautions to prevent blockages in the installation hoses. (Can prevent clogging with lime
solvent.
Summary of Contents for STELLA COMBINE
Page 1: ...INSTALLATION AND USER MANUAL FOR STELLA COMBINE OVEN I1...
Page 2: ...2 I memak com 2 I memak com...
Page 27: ...INSTALLATION AND USER MANUAL FOR STELLA COMBINE OVEN I27 TOUCH CONTROL PANEL SIGNALS...
Page 62: ...62 I memak com Machine Mechanism Lubricating Figure9 Figure10...
Page 67: ...INSTALLATION AND USER MANUAL FOR STELLA COMBINE OVEN I67...
Page 68: ...68 I memak com...