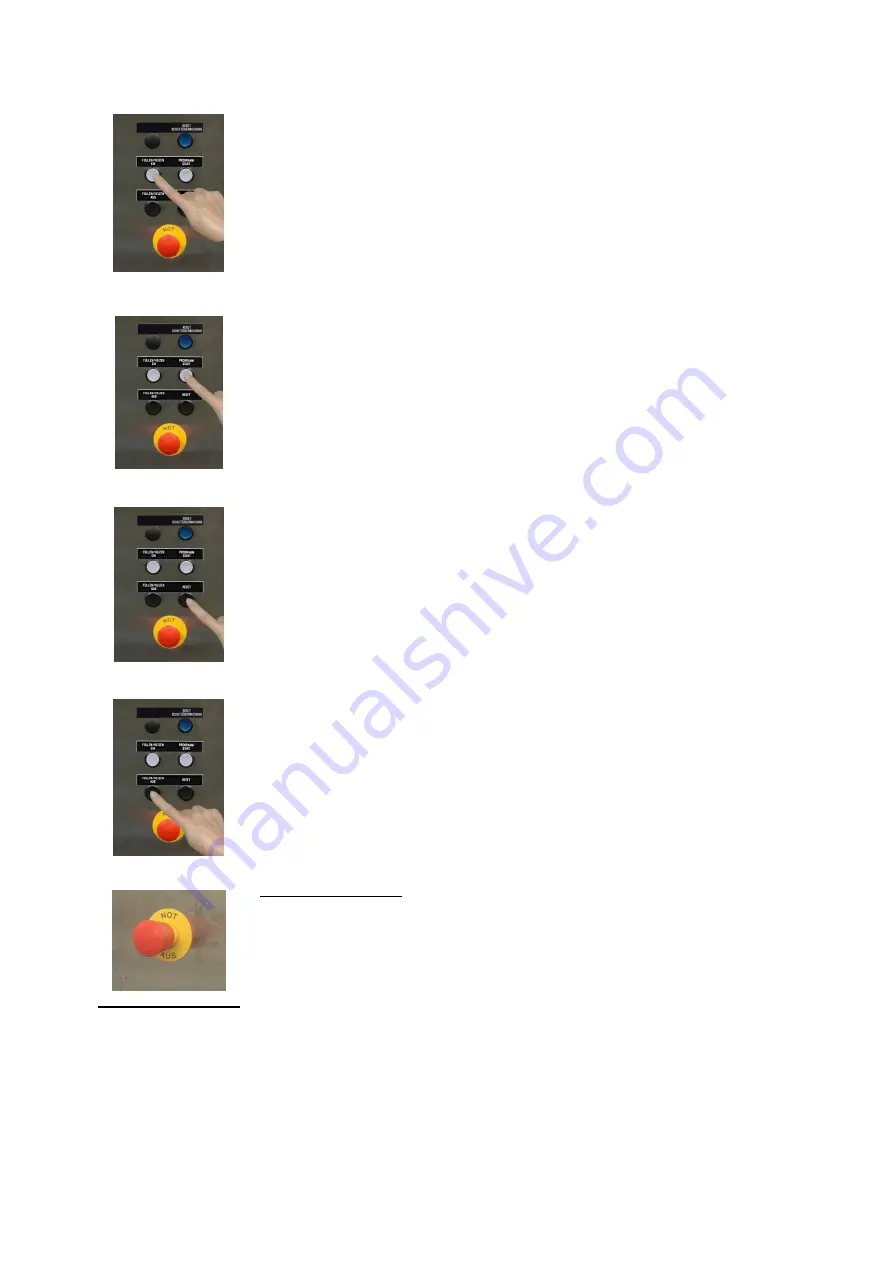
15 / 32
9648649
10.2
Operation
FILLING/HEATING
When pressing the key
“Filling/Heating on“
the wash tanks are automatically filled and
heated up. (This process may take some time depending on the water temperature, water
pressure and heating power available.)
PROGR. START
After displaying "OPERATING MODE" in the touch panel, the machine is put into operation
with the
"PROGRAM START"
button.
Make sure before that all doors are closed.
The machine takes control of all other functions (such as monitoring the wash tank, rinsing
and drying temperature, loss of water in the wash tank, etc.), thereby eliminating the need
for further control or operation.
RESET
Washing can be temporarily interrupted with the
"RESET"
button; i.e. the wash pumps and
transport are switched off.
However, the tank heating elements are not switched off with the result that the machine
remains ready for operation and washing can recommence when the button
“OPERATION”
is pressed.
FILLING/HEATING OFF
With the key
„FILLING/HEATING OFF“
the machine is completely set out of operation.
(Note! "Cleaning the machine")
EMERGENCY STOP
EMERGENCY STOP
The machine has one or more emergency off switches. This enables the entire machine to
be shut down. Restarting the machine requires unlocking the emergency off switch and is
only possible in the switch cabinet.
The machine must be restarted only once it has been established that the hazardous situ-
ation triggering the emergency stop has been rectified and restarting the machine will not
cause any danger.