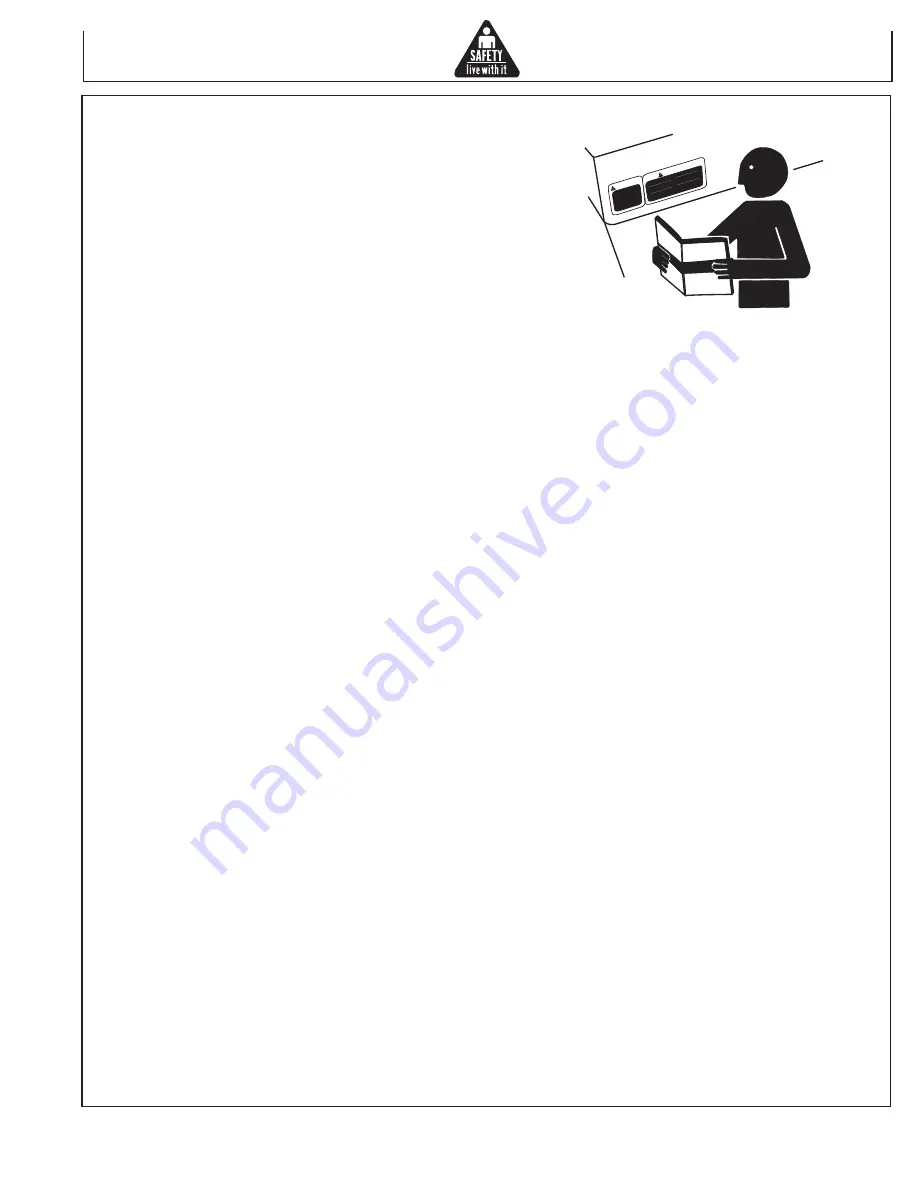
Operator’s Manual
11
IMPORTANT SAFETY INSTRUCTIONS
WARNING: To reduce the risk of injury, read this operator’s manual
completely before using. When using this product, the following
basic precautions should always be followed:
1. Risk from Negligence: Risk of injury from negligent use. Never
allow children or adolescents to operate this unit! Stay alert-
watch what you are doing. Do not operate the unit when fatigued
or under the influence of alcohol or drugs. Know how to stop the
unit. Be thoroughly familiar with controls.
2. Risk of Unit Damage: Risk of major repair. Do not operate the
unit without an air filter. Do not operate the unit in a corrosive
environment. Always operate the unit in a stable, secure
position to prevent the u
nit from falling. Follow all maintenance
instructions listed in this manual. Overuse can cause overheating;
allow cooling period; follow rated duty cycle. Reduce current or
reduce duty cycle before starting to weld again. Do not block or
filter airflow to unit.
3. When starting the unit, using recoil starter grip, be sure that
nothing is in a position to be hit by the operator’s hand or arm.
Be sure the switch on electric power tools is in the “OFF” position
before plugging them into the unit.
4. Do not operate the unit or any electrical tool in any area where
water or similar materials constitute an electrical hazard to the
operator. Do not operate on wet surfaces, in rain or in snow.
5. Always be sure that the unit is on secure footing so that it cannot
slide or shift around, endangering workers.
6. Avoid contacting the hot exhaust manifold, muffler or cylinder(s).
7. Keep clear of all rotating parts.
8. Unless the tool or appliance is double insulated, it must be
grounded through a properly grounded receptacle. Tools and
appliances which have 3 prong plugs must be plugged into
extension cords and electrical receptacles with 3 holes. Before
operating any electrical item, be sure it is in good repair.
9. Beware of using this equipment in confined spaces. Confined
spaces, without sufficient fresh air ventilation, can contain
dangerous gases. Running gasoline engines in such environments
can lead to deadly explosions and/or asphyxiation.
10. Use extreme caution when lifting this unit. This unit is heavy
so proper lifting techniques should be used.
SAVE THESE INSTRUCTIONS
WAR
NING
WAR
NING
S IN
THE
MA
NUA
LS.
WAR
NING
S IN
THE
MA
NUA
LS.
CAU
TION
O CA
UTIO
NS I
N
O TH
E MA
NUA
LS
O CA
UTIO
NS I
N
O TH
E MA
NUA
LS
O CA
UTIO
NS I
N
O TH
E MA
NUA
LS
O CA
UTIO
NS I
N
O TH
E MA
NUA
LS