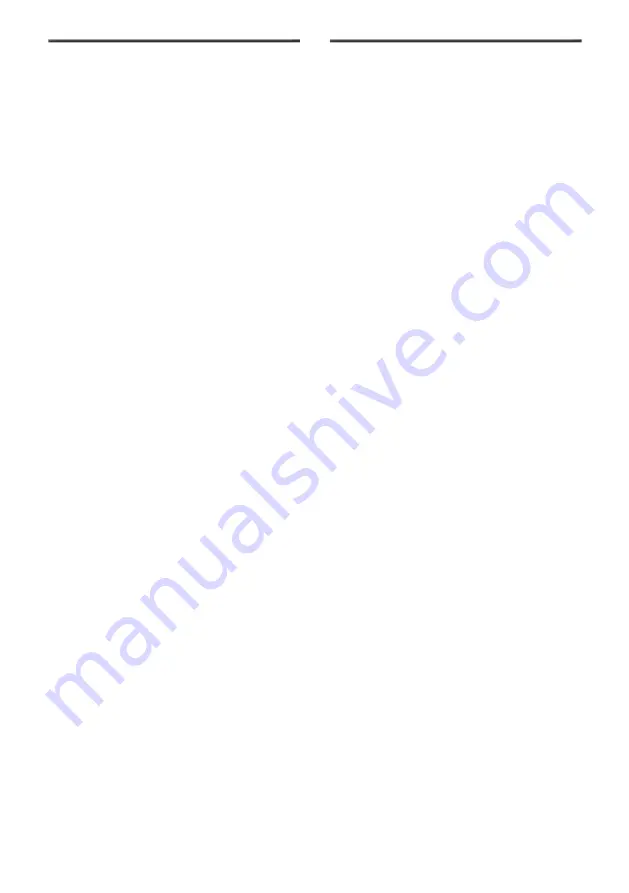
IMPORTANT
Read these safety instructions carefully in addition to the instructions for use,
operation and maintenance. Keep them in a safe place for consultation
following use.
This air hydraulic jack has been designed for use in the elevation of cars and
lorries. Any other application beyond the conditions established for use of this
jack will be considered inappropriate.
Handle the jack correctly and ensure that all parts are in good condition prior
to its initial and subsequent uses and that no parts are missing. Otherwise, do
not use the jack and contact your nearest manufacturer, supplier or technical
service.
Operation and maintenance of the jack should only be performed by authorised
persons, having read carefully and understood the contents of this manual.
Do not modify the jack in any way.
Non-compliance with these instructions may result in injury or damage to the
user, the jack or the load to be lifted.
The manufacturer accepts no responsibility for the improper use of the jack.
1. SAFETY INSTRUCTIONS
1.1 The load to be lifted should never exceed the rated capacity of the jack.
1.2 The jack should be supported on a solid, level and horizontal surface
to avoid any sinking. It should be well illuminated and free of unnecessary
materials.
1.3 Ensure that there are no passengers inside the vehicle to be lifted and non
essential persons should keep a safe distance from the working area. The
engine should be switched off and the hand brake applied. Use safety stands
if necessary.
1.4 The air supply hose should not be worn and connections should be in good
condition. Keep the hose clean and away from heat, dirty areas or sharp edges
and do not bend it. Don´t pull the hose to remove the jack.
1.5 Position the jack under the vehicle manufacturer’s recommended lifting
points, which should be stable and centred over the jack saddle. These points
will be free from grease or dirt. All off-centred loads may produce risks.
1.6 The jack should be positioned so as to avoid the need for the operator to
introduce any part of his/her body underneath the vehicle. Never work under a
raised vehicle without previously supporting it with mechanical stands or other
appropriate methods.
1.7 During lifting and lowering operations, all possible precautions should be
taken to avoid movement of the vehicle load. Ensure that there are no persons
or obstructions underneath the vehicle prior to lowering.
1.8 The operator should be able to observe the lifting device and the load
during all movements. In the presence of dangerous conditions, such as
movement of the vehicle, etc, the lifting or lowering process must be
interrupted.
1.9 The jack is a lifting device and should never be used to support or move the
vehicle. To perform any operation underneath the vehicle, first support it using
the appropriate mechanical stands. The handle and wheels with which these
devices are equipped should only be used for positioning under the load and
moving the device from one place to another. Check that the wheels rotate
freely.
1.10
IMPORTANT
. Use only the manufacturer´s extensions. Never use more
than one extension at a time (Fig.8). Saddle “C” must be placed direct on the
jack piston, never on the extension (Fig.9)
1.11 Disconnect the air supply hose from the connector located in the handle,
once the operation is completed and prior to carrying out any maintenance
work.
1.12 As an additional safety measure against overload, the jack is fitted with an
overload valve, set at the factory. This valve should not be tampered with under
any circumstances.
2.1 ASSEMBLY, USE AND OPERATION (N10-3L,N15-2L,.....)
2.1.1 Before operating the jack, a small assembly operation is required,
consisting of: Removing the upper cover, place the jack handle in position (4)
and secure the bolt (26) and its washer (27), which are included in a kit as
indicated (Fig.6). Replace the cover.
2.1.2 The handle has four positions: Foldable for transportation and packing
(1). Out of operation (2). Movement (3). In operation or horizontal (4). Each
position is achieved by disengaging the trigger lever (1, Fig. 7). The purpose
of the handle is to position the jack or simplify its movement. Do not exert any
pressure on the handle.
2.1.3 Should the jack need to be packaged for transportation, remove the
screw (26) and the washer (27) and move the handle to position (1, Fig.5)
2.1.4 It is essential that an air filter-lubricator unit is installed (Fig.2), which is
drained daily.
2.1.5 Drain the compressor daily. Poor air quality damages essential parts for
the proper operation of the jack.
2.1.6 Prior to connecting the air supply hose (3), it is necessary to check that
the control lever (2) is in the OFF position (Fig.7). The air hose should not have
a section inferior to that of the air entry connector (3). If unusually long hoses
are used, the air pressure should be increased.
2.1.7 Ensure that the same air pressure is going to be maintained during
operation. Optimum performance of this jack is obtained with a pressure of
7-10kg/cm2 and a minimum air flow of 280 l/min.
2.1.8 A final operation to be performed prior to using the jack is the elimination
of any air that may have entered the hydraulic system during transportation.
With the air hose connected (3), push the control lever (2, Fig.7) towards the
DOWN position, holding it there for some seconds. Move the control lever to
the UP position to complete a load free lifting cycle. Move the control lever
(2) to the DOWN position to retract the pistons and hence check that the
lowering action is performed steadily without any jerking movements. If the
lowering action is unsteady, repeat the cycle until the lowering of the pistons
is completed in a steady and uniform way. This will show that the draining
operation has been successfully completed.
GB
2.1.9 Now the jack is ready for operation.
2.1.10 Lifting Positioning the jack under the lifting point of the vehicle,
and following all of the safety instructions described, the lifting operation
is performed by moving the to lever control (2, Fig.7) to the UP position
and holding it there until the vehicle has been lifted to the desired height.
Immediately place metal stands or another appropriate method to support the
elevated vehicle.
2.1.11 Lowering Check that there are no obstacles or people underneath the
vehicle. Once the operation is completed, remove the mechanical support
stands by lifting the vehicle slightly in order to simplify their removal. Lowering
is performed by moving the handle (2, Fig.7) to the DOWN position and
maintaining it until the operation is completed. To avoid brusque lowering
operations, the jack is fitted with a system which automatically regulates and
controls the lowering operation (L.C.S.).
2.1.12 Proceed to retract the pistons by pushing and holding the handle (2,
fig.7) in the DOWN position until they are fully introduced.
2.1.13 If the jack is not going to be in use, close the air supply and disconnect
the supply hose.
2.1.14 After each use, check the components of the jack. If any anomaly is
detected, rectify it.
2.2 ASSEMBLY, USE AND OPERATION (NP15-2B)
2.2.1 The handle has three positions: Movement (1), in operation (2) or
horizontal (3). The purpose of the handle is to position the jack or simplify its
movement. Do not exert any pressure on the handle.
2.2.2 It is essential that an air filter-lubricator unit is installed (Fig.2), which is
drained daily.
2.2.3 Drain the compressor daily. Poor air quality damages essential parts for
the proper operation of the jack.
2.2.4 The air hose should not have a section inferior to that of the air entry
connector (1 , fig.3). If unusually long hoses are used, the air pressure should
be increased.
2.2.5 Ensure that the same air pressure is going to be maintained during
operation. Optimum performance of this jack is obtained with a pressure of
7-10kg/cm2 and a minimum air flow of 280 l/min.
2.2.6 Now the jack is ready for operation.
2.2.7 Lifting Positioning the jack under the lifting point of the vehicle, and
following all of the safety instructions described, the lifting operation is
performed by pushing the push-button UP (Fig.3) and holding it there until the
vehicle has been lifted to the desired height. Immediately place metal stands or
another appropriate method to support the elevated vehicle.
2.2.8 Lowering Check that there are no obstacles or people underneath the
vehicle. Once the operation is completed, remove the mechanical support
stands by lifting the vehicle slightly in order to simplify their removal. Lowering
is performed by pushing the push-button DOWN (Fig.3) and maintaining it until
the operation is completed. To avoid brusque lowering operations, the jack is
fitted with a system which automatically regulates and controls the lowering
operation (L.C.S.).
2.2.9 Proceed to retract the pistons by pushing and holding the push-button
DOWN (fig.3) until they are fully introduced.
2.2.10 If the jack is not going to be in use, close the air supply and disconnect
the supply hose.
2.2.11 After each use, check the components of the jack. If any anomaly is
detected, rectify it.
3. MAINTENANCE
3.1 Both the maintenance and repair of this jack may only be carried out by
qualified and authorized personnel.
3.2 Before performing any maintenance operation, disconnect the air supply
hose from the connection (1, Fig.3) located in the handle (NP15-2B) and (3,
Fig.7) located in the handle (N10-3L)
3.3 Clean and lubricate the moving parts of the jack at regular intervals and
introduce a small amount of lubricant in the air inlet connection. The whole jack
should be kept clean and protected from aggressive conditions at all times.
3.4 Oil Level The pistons should be fully retracted prior to proceeding to check
or refill the oil level. The oil level is correct whet it is between the two marks on
the rod. Refill as required in accordance with the volume indicated in the table.
3.5 If all of the oil needs to be replaced, position the jack between two
supports so that the connecting tube (1, Fig.4) can be removed through which
the oil will flow and be collected in a container which will be handed over to an
authorised agent. Other methods may also be used to remove the oil: Using
a pneumatic oil extractor, positioning the jack in a slanted lateral position,
removing the tank etc.
3.6
IMPORTANT
An excess of oil may affect the operation of the jack.
3.7 Only use hydraulic oil, HL or HM type, with an ISO grade of cinematic
viscosity of 20cSt at 40ºC or of an Engler viscosity of 2 at 50ºC.
3.8
EXTREMELY IMPORTANT
Never use brake fluid.
3.9 Always use original parts. The use of non-original components may damage
the jack and will invalidate the guarantee.
3.10 Damaged or illegible labels should be replaced with new ones.
3.11 Whenever the jack is not in use, the pistons should be fully retracted so as
to reduce the risk of corrosion.
3.12 When ordering spare parts, please state the reference indicated in the
general chart. Repair kits for the hydraulic set (X), motor (Y) and offloading (Z)
are available containing all the gaskets and seals.