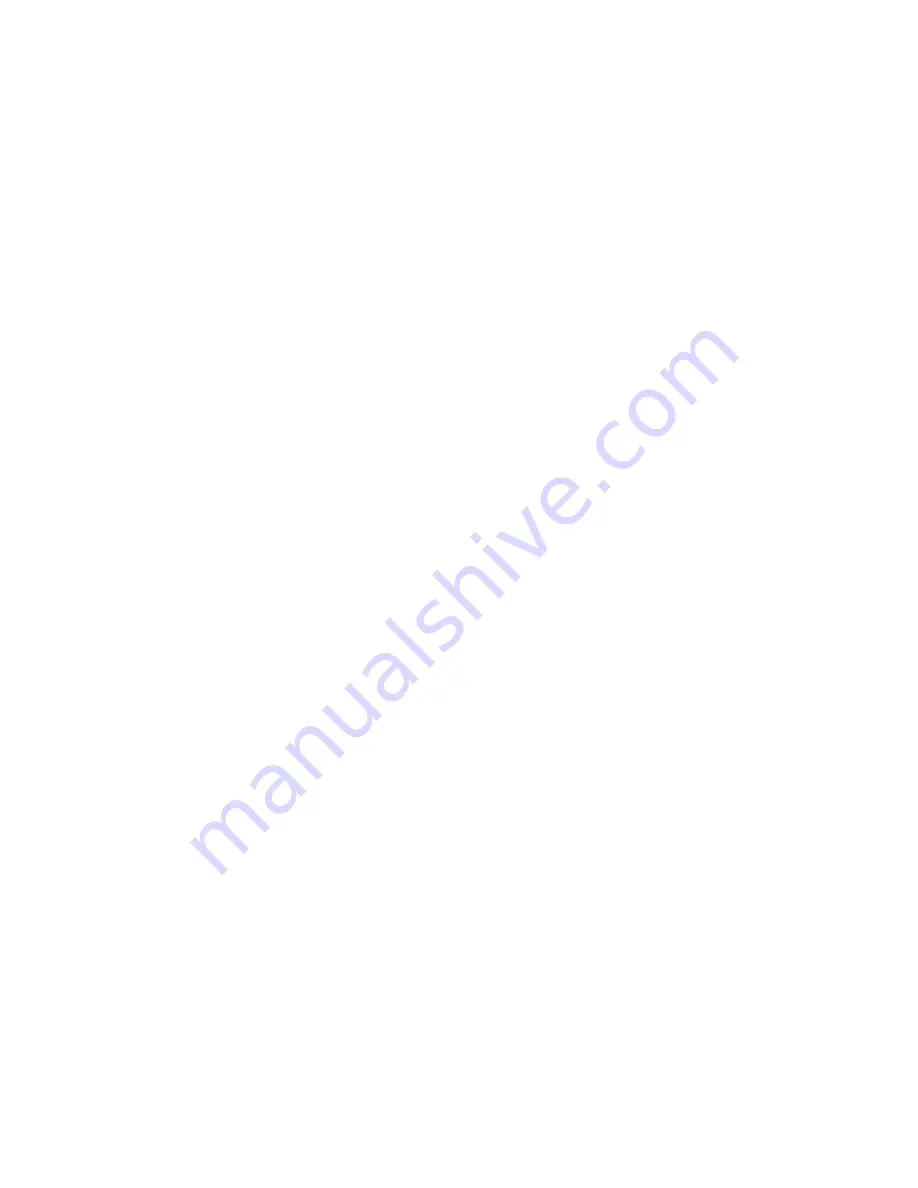
12. Machine Condition-Whether a machine is old or new, and whether well maintained or not contributes
to how well it runs and how long the band last. The better shape a machine is in, the better the bands will
run. Poor machines ruin bandsaw blades.
13. Proper Vises - The work must be properly held. Side vises and top vises, if necessary, should be in
good shape and able to firmly hold the work. Anything that moves will strip teeth.
14. Guides - The guides must support the band well while in the cut. The guides in conjunction with
tension are all that keeps the band straight. Roller guides should be snug against the band and turn
freely.
The surface should be flat and not worn at an angle. Solid carbide guides should also be sung against the
band and should show no sign of wear. They can be faced off if necessary. Backup guides should not be
grooved and should also turn freely if rollers. Be sure the teeth of the band do not ride up into the
guides.
15. Guide Arms - The guide arms should be as close to the work as possible. Beam strength is determined
by a cubed factor, so increasing the distance between the guides by a factor of 2 decreases the beam
strength by a factor of (2)^3 or 8. You lose a lot very quickly.
16. Brushes - A good set of brushes (powered is preferable) aid in the cleaning of chips from the gullets,
if available and properly adjusted. One test shows a better than 25
﹪
increase in life just by using
brushes.
Always check the brushes.
17. Coolant - A good coolant will help cool, lubricate and wash the bandsaw blades. Always maintain a
good flood of coolant when possible.
18. Material machinability - The tougher the material, the less expected band life. For instance 1018 vs.
Inconel 718.
19. Material Hardness - A Rockwell C scale reading of 40 is approaching a machinability of 0. Only
recently have we been able to go much beyond this with the introduction of our CT Type III band.
20. Material Shape - Structural and small solids are always harder on a band than large solids.
21. Production Requirement - Continuous runs of one size and material is easier than intermittent cutting
of various sizes, shapes and materials.
22. Room Temperature - Temperature has a big effect on the hydraulic system of a machine. Always allow
the machine to warm up before staring to saw.
5 – 4