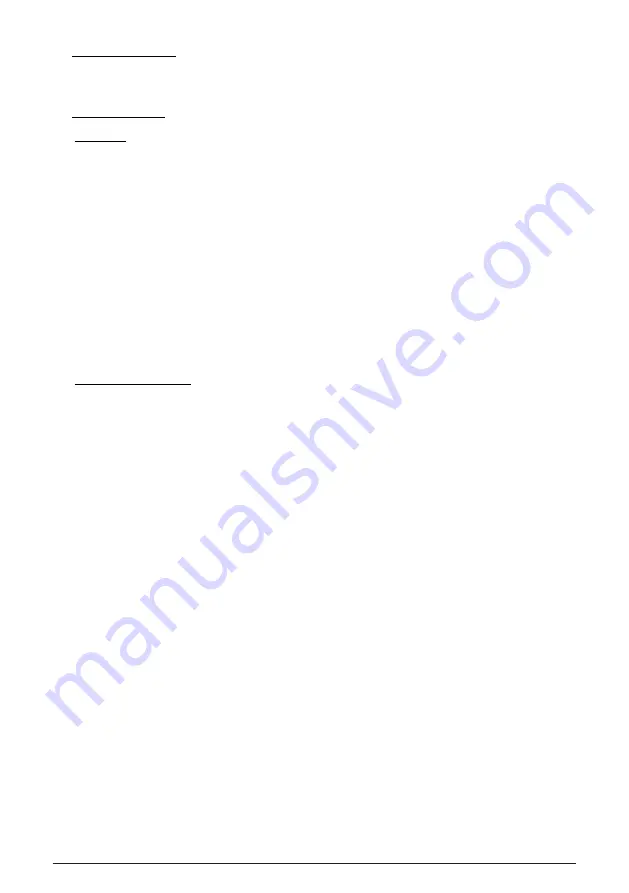
1.
INTRODUCTION
These horn units have been designed for use in harsh environmental conditions.
2. INSTALLATION
General
When installing and operating explosion-protected electrical equipment, require-
ments for selection, installation and operation should be referred to eg. IEC
60079-14 worldwide and the ‘National Electrical Code’ in North America.
Additional national and/or local requirements may apply.
Ensure that all nuts, bolts and fixings are secure.
Ensure that only the correct UL listed stopping plugs are used to blank off unused
gland entry points and that the NEMA/IP rating of the unit is maintained.
The unit is mounted via 2 x Ø 0.31” (8 mm) fixing holes in the base. The fixing
holes have been designed to accept an M6 screw or bolt. MEDC recommend the
use of stainless steel screws.
Cable Termination
CAUTION: Before removing the cover assembly, ensure that the power to the
unit is isolated.
Unscrew and remove the 4 off screws holding the cover assembly to the base.
Keep in a safe, accessible location.
Twist the cover gently clockwise and anti-clockwise, whilst pulling it away from the
unit. Remove to gain access to the interior of the base.
Cable termination should be in accordance with specifications applying to the
application. MEDC recommend that all cables and cores should be fully identified.
Ensure that only correct UL Listed cable glands are used and that the assembly is
shrouded and correctly earthed.
All cable glands should be of an equivalent NEMA/IP rating to that of the unit
and integrated with the unit such that this rating is maintained.
The internal earth terminal (where fitted), must be used for the equipment ground-
ing connection and the external terminal is for a supplementary bonding connec-
tion where local codes or authorities permit or require such a connection.
Once termination is complete, carefully push the cover back onto the unit, avoid-
ing damage to the mating surfaces. Replace & tighten the 4
off cover screws
evenly, to ensure maintenance of the required gap between the cover and enclo-
sure.
07/17
© Eaton MEDC Ltd 2017