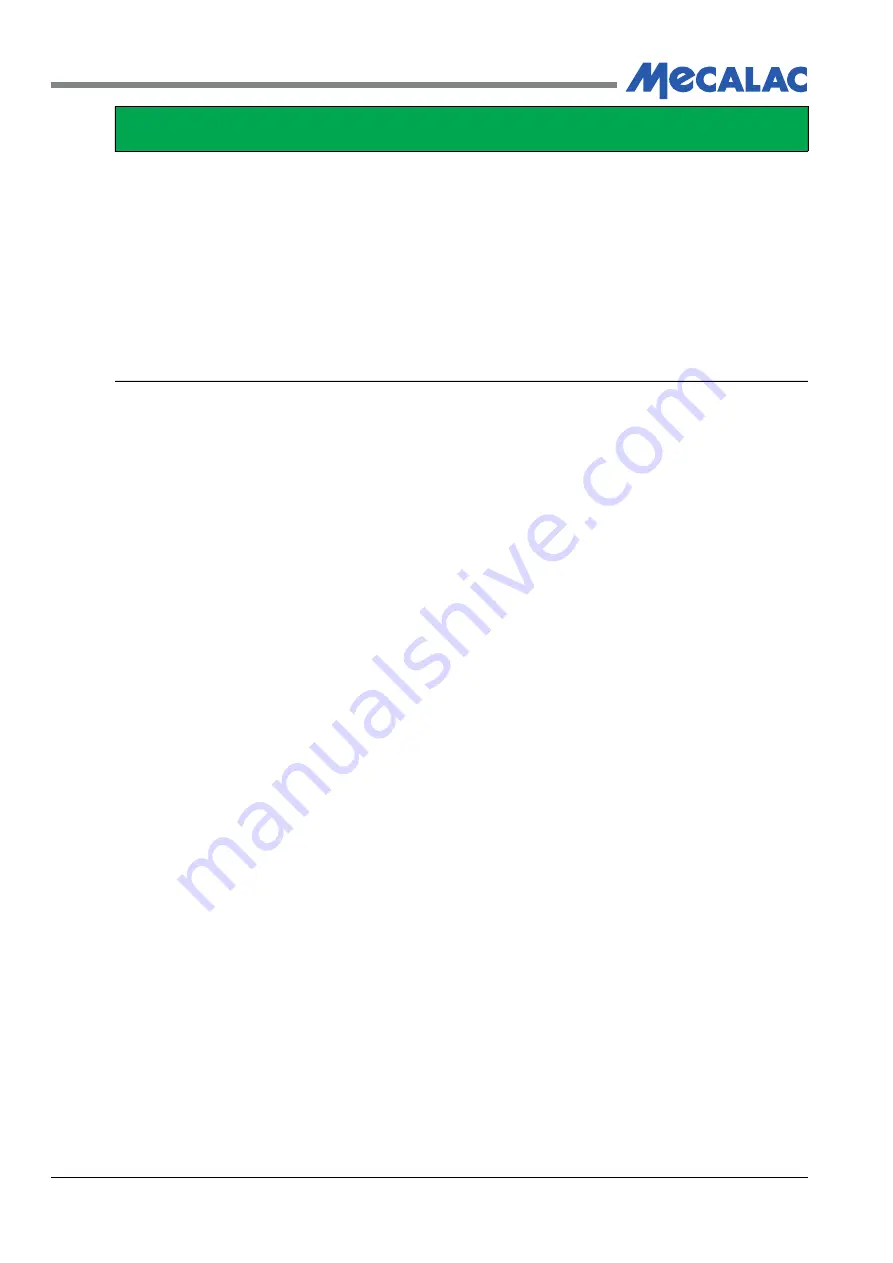
Page 6 - 2
TA3H, TA3SH & TA3.5SH
6. Initial Setup & Adjustments
6.3
Start Up and Adjustments
When all delivery checks have been made and the ROPS has been placed and secured in the
work position:-
• Start the engine and allow to run for a few minutes to warm up.
• Check all instruments and warning lights are functioning correctly.
• Check lighting and indicators operate (if fitted).
• Stop the engine and check for any fluid leaks or signs of overheating.
• Re-start the engine, drive the machine a short distance to check operation of transmission,
brakes and steering.
• Check if the skip tips, lowers and (swing skip models only) rotates in either direction.
• Park up and stop the engine.
• Report and have rectified any faults before placing machine into service.
PROCEDURE
1. Remove the linch pins from the locking pins either side of the ROPS.
2. Remove the locking pins.
3. Push the top half of the ROPS upwards to the working position.
4. Refit the locking pins.
5. Secure the locking pins in position with the linch pins.
6. Remove the rubber cover and fit the beacon to the stem on top of the ROPS.
7. Switch on the beacon and check it is working correctly.
Summary of Contents for TA3.5SH
Page 6: ...Table of Contents 4 TA3H TA3SH TA3 5SH Table of Contents...
Page 72: ...Page 7 10 TA3H TA3SH TA3 5SH 7 Standard Operating Procedures...
Page 76: ...Page 8 4 TA3H TA3SH TA3 5SH 8 Emergency Operating Procedures...
Page 114: ...Page 11 2 TA3H TA3SH TA3 5SH 11 Recovery...
Page 118: ...Page 13 2 TA3H TA3SH TA3 5SH 13 Glossary...
Page 119: ...TA3H TA3SH TA3 5SH Appendices 1 Appendices Appendix 1 Electrical Diagrams...
Page 126: ...Appendices 8 TA3H TA3SH TA3 5SH Appendices...
Page 127: ...TA3H TA3SH TA3 5SH Appendices 9 Appendices Appendix 2 Hydraulic Diagrams...
Page 132: ...Appendices 14 TA3H TA3SH TA3 5SH Appendices...
Page 134: ...Warranty 2 Warranty Certificate...
Page 135: ......