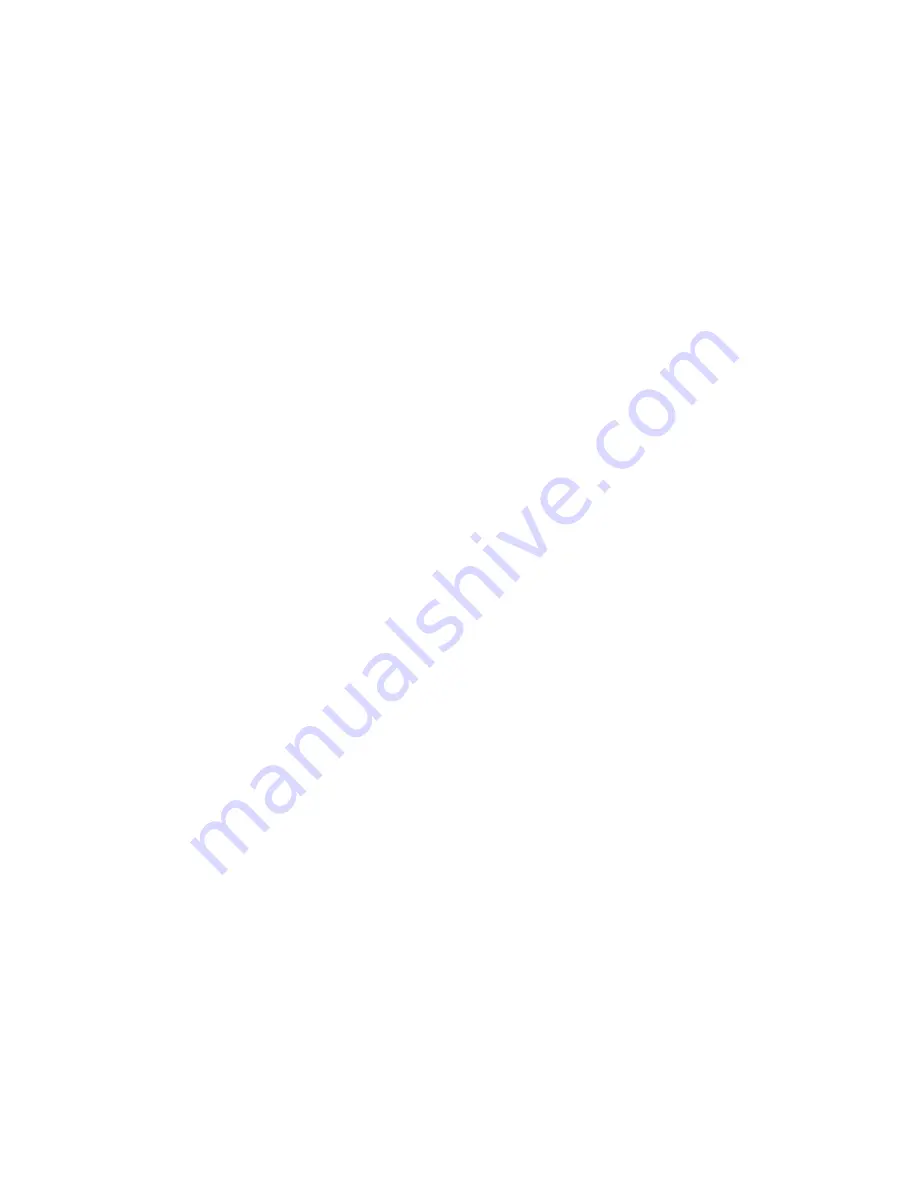
Page 8 of 24 / IM 439
2.
The system should be filled at the city water makeup
connection with all air vents open. After filling, vents should
be closed.
The contractor should start main circulator with pres-
sure reducing valve makeup open. Vents should be
checked in sequence to bleed off any trapped air to as-
sure circulation through all components of the system.
Power to the heat rejector unit should be off, and the
supplementary heat control set at 80
°
F (27
°
C).
While circulating water, the contractor should check
and repair any leaks in the piping. Drain at the lowest
point(s) in the system should be opened for initial flush
and blowdown, making sure city water fill valves are set
to make up water at the same rate. Check the pressure
gauge at pump suction and manually adjust the makeup
to hold the same positive steady pressure both before
and after opening the drain valves. Flush should con-
tinue for at least two hours, or longer if required, to see
clear, clean drain water.
3.
Supplemental heater and circulator pump should be shut
off. All drains and vents should be opened to completely
drain down the system. Short circuited supply and re-
turn runouts should now be connected to the conditioner
supply and return connections. Teflon tape is recom-
mended over pipe dope for pipe thread connections. Use
no sealers at the swivel flare connections of hoses.
4.
Trisodium phosphate was formerly recommended as a
cleaning agent during flushing. However, many states
and localities ban the introduction of phosphates into their
sewage systems. The current recommendation is to sim-
ply flush longer with warm 80
°
F (27
°
C) water.
5.
Refill the system with clean water. Test the litmus paper
for acidity, and treat as required to leave the water slightly
alkaline (pH 7.5 to 8.5). The specified percentage of anti-
freeze may also be added at this time. Use commercial
grade anti-freeze designed for HVAC systems only. Do
not use automotive grade anti-freeze.
6.
Set the system control and alarm panel heat add setpoint
to 70
°
F (21
°
C) and the heat rejection setpoint to 85
°
F
(29
°
C). Supply power to all motors and start the circulat-
ing pumps. After full flow has been established through
all components including the heat rejector (regardless of
season) and air vented and loop temperatures stabilized,
each of the conditioners will be ready for check, test and
start-up and for air and water balancing.
Start-up
1. Open all valves to full open position and turn on power to
the conditioner.
2. Set thermostat for
Fan Only
operation by selecting
Off
at
the system and
On
at the fan switch. If
Auto
fan operation
were selected, the fan would cycle with the compressor.
Check for proper air delivery.
3. All units have variable pitch motor sheaves. Reset for
correct airflow.
4. Set thermostat to
Cool
. If the thermostat is an automatic
changeover type, simply set the cooling temperature to
the coolest position. On manual changeover types addi-
tionally select
Cool
at the system switch.
Again, many conditioners have time delays which
protect the compressor against short cycling. After a few
minutes of operation, check the discharge grilles for cool
air delivery. Measure the temperature difference between
entering and leaving water. It should be approximately
1
1
⁄
2
times greater than the heating mode temperature
difference. For example, if the cooling temperature dif-
ference is 15
°
F (8
°
C), the heating temperature difference
should have been 10
°
F (5
°
C).
Without automatic flow control valves, a cooling tem-
perature difference of 10
°
F to 14
°
F (5
°
C to 8
°
C) is about
right. Adjust the combination shutoff/balancing valve in
the return line to a water flow rate which will result in the
10
°
F to 14
°
F (5
°
C to 8
°
C) degree difference in cooling.
5. Set thermostat to
Heat
. If thermostat is the automatic
changeover type, set system switch to the
Auto
position
and depress the heat setting to the warmest selection.
Some conditioners have built-in time delays which pre-
vent the compressor from immediately starting. With
most control schemes, the fan will start immediately.
After a few minutes of compressor operation, check for
warm air delivery at discharge grille. If this is a “cold
building” start-up, leave unit running until return air to the
unit is at least 65
°
F (18
°
C).
Measure the temperature difference between enter-
ing and leaving air and entering and leaving water. With
entering water of 60
°
F to 80
°
F (16
°
C to 27
°
C), leaving
water should be 6
°
F to 12
°
F (3.3
°
C to 6.6
°
C) cooler, and
the air temperature rise through the machine should not
exceed 35
°
F (19
°
C). If the air temperature exceeds 35
°
F
(19
°
C), the airflow rate is probably inadequate.
If the water temperature difference is less than 6
°
F
(3.3
°
C) degrees, the water flow rate is excessive. If the
water temperature difference exceeds 12
°
F (6.6
°
C), then
the water flow rate is inadequate.
6. Check the elevation and cleanliness of the condensate
line. If the air is too dry for sufficient dehumidification,
slowly pour enough water into the condensate pan to
ensure proper drainage.
7. If the conditioner does not operate, the following points
should be checked:
a. Is proper voltage being supplied to the machine?
b. Is the proper type of thermostat being used?
c. Is the wiring to the thermostat correct?
8. If the conditioner operates but stops after a brief period,
check for:
a. Is there proper airflow? Check for dirty filter, incorrect
fan rotation (3-phase fan motors only), or incorrect
ductwork.
b. Is there proper water flow rate within temperature limits?
Check water balancing; backflush unit if dirt-clogged.
9. Check the unit for vibrating refrigerant piping, fan wheels,
etc.
10. Do not lubricate the fan motor during the first year of
operation as it is prelubricated at the factory.
Cleaning and Flushing System
(Continued)