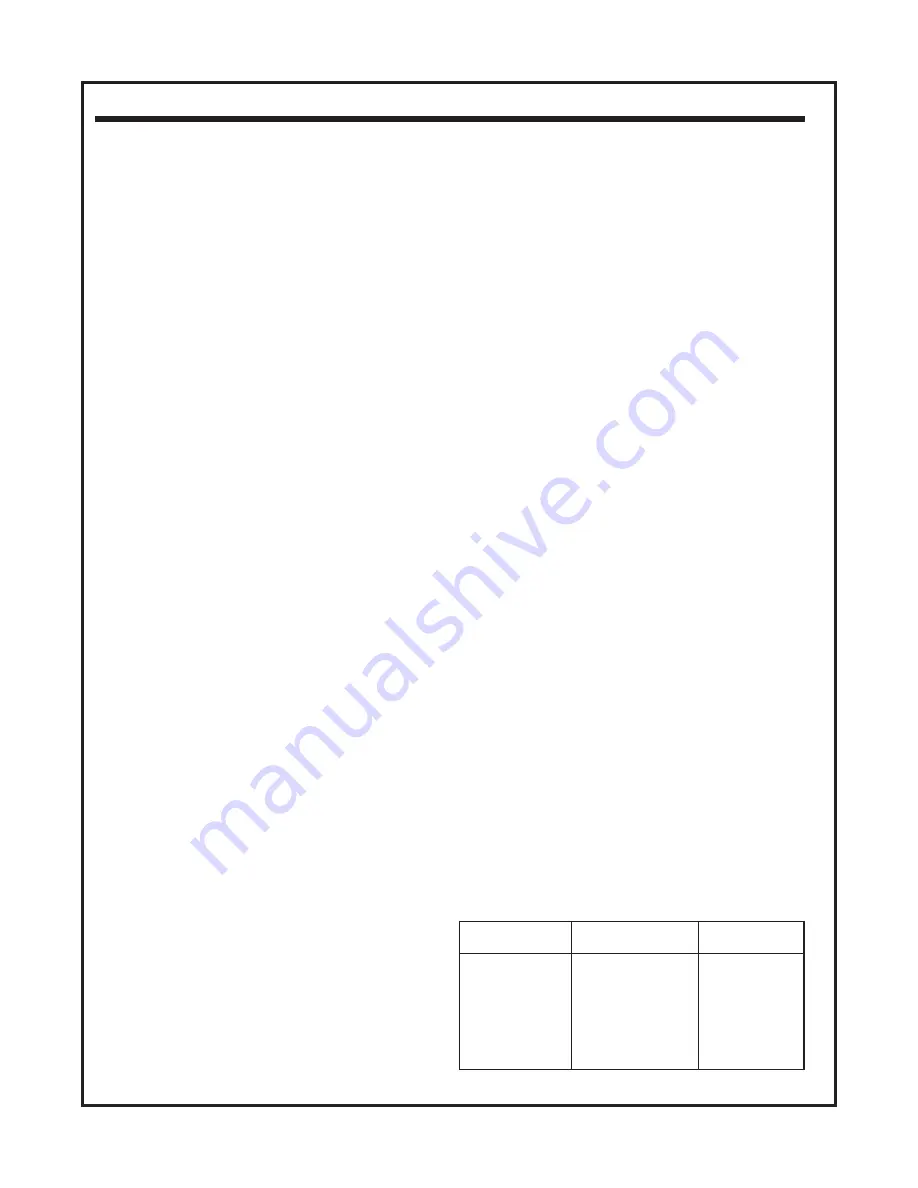
Before operating a blower under power for the first time,
recheck the unit and the installation thoroughly to reduce the
likelihood of avoidable troubles. Use the following procedure
check list as a guide, but consider any other special condi-
tions in the installation.
J
Be certain that no bolts, tools, rags, or debris have been
left in the blower air chamber or piping.
J
If an outdoor intake without filter is used, be sure the
opening is located so it cannot pick up dirt and is pro-
tected by a strong screen or grille. Use of the temporary
protective screen as described under INSTALLATION is
strongly recommended.
J
Recheck blower leveling, drive alignment and tightness
of all mounting bolts if installation is not recent. If belt
drive is used, adjust belt tension correctly.
J
Turn drive shaft by hand to make sure impellers still
rotate without bumping or rubbing at any point.
J
Ensure oil levels in the main oil sumps are correct.
J
Check lubrication of driver. If it is an electric motor, be
sure that power is available and that electrical overload
devices are installed and workable.
J
Open the manual unloading valve in the discharge air
line. If a valve is in the inlet piping, be sure it is open.
J
Bump blower a few revolutions with driver to check that
direction of rotation agrees with arrow near blower
shaft, and that both coast freely to a stop.
After the preceding points are cleared, blower is ready for
trial operation under “no-load” conditions. The following
procedure is suggested to cover this initial operation test
period.
a.
Start blower, let it accelerate to full speed, then shut off.
Listen for knocking sounds, both with power on and as
speed slows down.
b.
After blower comes to a complete stop, repeat above,
but let blower run 2 or 3 minutes. Check for noises,
such as knocking sounds.
c.
After blower comes to a complete stop, operate blower
for about 10 minutes unloaded. Check oil levels.
Observe cylinder and headplate surfaces for develop-
ment of hot spots such as burned paint, indicating
impeller rubs. Be aware of any noticeable increase in
vibration.
Assuming that all trials have been satisfactory, or that neces-
sary corrections have been made, the blower should now
have a final check run of at least one hour under normal
operating conditions. After blower is restarted, gradually
close the discharge unloading valve to apply working pres-
sure. At this point it is recommended that a pressure gauge
or manometer be connected into the discharge line if not
already provided, and that thermometers be in both inlet and
discharge lines. Readings from these instruments will show
whether pressure or temperature ratings of the blower are
being exceeded.
During the final run, check operating conditions frequently
and observe the oil levels at reasonable intervals. If excessive
noise or local heating develops, shut down immediately and
determine the cause. If either pressure rise or temperature
rise across the blower exceeds the limit specified in this
manual, shut down and investigate conditions in the piping
system. Refer to the TROUBLESHOOTING CHECKLIST for
suggestions on various problems that may appear.
The blower should now be ready for continuous duty opera-
tion at full load. During the first few days make periodic
checks to determine whether all conditions remain steady, or
at least acceptable. This may be particularly important if the
blower is supplying air to a process system where conditions
can vary. At the first opportunity, stop the blower and clean
the temporary inlet protective screen. If no appreciable
amount of debris has collected, the screen may be removed.
See comments under INSTALLATION. At this same time, ver-
ify leveling, coupling alignment or belt tension, and mounting
bolt tightness.
Should operating experience prove that blower capacity is a
little too high for the actual air requirements, a small excess
may be blown off continuously through the manual unload-
ing or vent valve. Never rely on the pressure relief valve as
an automatic vent. Such use may cause the discharge pres-
sure to become excessive, and can also result in failure of
the valve itself. If blower capacity appears to be too low, refer
to the TROUBLESHOOTING CHECKLIST.
Vibration Assessment Criteria
With measurements taken at the bearing locations on the
housings, see chart below for an appropriate assessment
guide for rotary lobe blowers rigidly mounted on stiff foun-
dations.
In general, blower vibration levels should be monitored on a
regular basis and the vibration trend observed for progres-
sive or sudden change in level. If such a change occurs, the
cause should be determined through spectral analysis.
As shown on the chart below, the level of all pass vibration
will determine the need to measure discrete frequency vibra-
tion levels and the action required.
Operation
All Pass Vibration Discrete Frequency
Action
(in/sec)
Vibration (in/sec)
0.45 or less
N/R
Acceptable
Greater than 0.45
0.45 or less @
Acceptable
but 1.0 or less
any frequency
Greater than 0.45 @
Investigate
any frequency
Greater than 1.0
Less than 1.0
Investigate
Greater than 1.0
Investigate
80
Summary of Contents for E850250
Page 2: ......
Page 6: ...6 Filtration 250 575 VACASSY352 012413 E 2 1 3 4 5 11 8 12 13 14 15 1 9 10 6 7...
Page 8: ...8 Enclosure Assembly 31HP VACASSY412 012513 E 1 2 3 6 4 5 7 8 9 10 11 12 14 13 9 15 16...
Page 10: ...10 Enclosure Assembly 31HP RC VACASSY413 012813 E 1 2 13 14 11 3 10 9 8 7 6 5 4 3 12...
Page 14: ...14 Blower Assembly VACASSY225 031213 E 31HP 1 2 3 7 6 5 4 8 17 9 10 11 12 13 14 15 11 16 18...
Page 16: ...Assembly of URAI DSL Blowers with Splash Lubricated Drive End 3 5 Gear Diameter 16...
Page 26: ...26 Electrical Control Bracket 012813 E VACASSY550 1 2 3 7 5 6 4 8...
Page 34: ...Hose Reel Assembly VACASSY762 083010 E 1 3 2 4 5 6 7 8 34...
Page 36: ...Hose Reel VACASSY761 072210 E Components 36...
Page 38: ...38 Hose Reel Assembly VACASSY763 081010 E 5 4 3 2 1...
Page 40: ...40 Hose Reel VACASSY764 081010 E Components...
Page 42: ...011711 E Trailer Assy 250 VACASSY901 12 13 6 6 11 11 1 2 3 4 5 6 7 10 9 8 42...
Page 44: ...1 2 3 4 5 6 7 9 8 Skid Assembly V250 113010 E VACASSY871 44...
Page 46: ...2 3 4 1 Tool Rack Assembly VACASSY757 090909 E STD I BEAM TRAILER 5 6 SKID UNIT 7 8 46...
Page 48: ...Antifreeze Assembly 060309 VACASSY943 1 2 3 4 48...
Page 50: ...HOSES 011711 E VACASSY938 1 2 3 50...
Page 52: ...Tools 3 Suction Tool 111210 E VACASSY712 4 1 2 3 52...
Page 56: ...3 2 1 Tools Wash Wand 042610 E VACASSY711 56...
Page 58: ...58 Tools 101512 E VACASSY713 Lawn Sweeper 3 4 1 2 2 3 3 9 8 5 6 7 10...
Page 60: ...60 Valve Box Cleanout Tool VACASSY714 101812 E 18 13 17 16 15 14 11 8 10 9 1 3 7 6 5 2 12 4...
Page 64: ...64 Tools 101912 E VACASSY716 Rotary Lance 3 2 1 4 5...
Page 66: ...StrongArm Assembly 010213 E VACASSY9501 1 2 3 4 5 6 7 8 9 10 13 14 12 15 11 16 17 18 V250 66...
Page 68: ...1 2 3 4 6 5 7 9 8 10 11 12 14 13 15 16 17 18 Arrow Board Option 111110 E VACASSY947 68...
Page 70: ...70 Arrow Board Option 073008 VACASSY947...
Page 71: ...Vacuum Diesel Engine Schematic 080108 71...
Page 72: ...Vacuum Diesel Engine Schematic 080108 72...
Page 73: ...Vacuum Diesel Engine Schematic 080108 73...
Page 74: ...Vacuum Diesel Engine Schematic 080108 74...
Page 75: ...Vacuum Diesel Engine Schematic 080108 75...
Page 76: ...PAGE LEFT BLANK 76...
Page 85: ...PAGE LEFT BLANK 85...
Page 88: ......