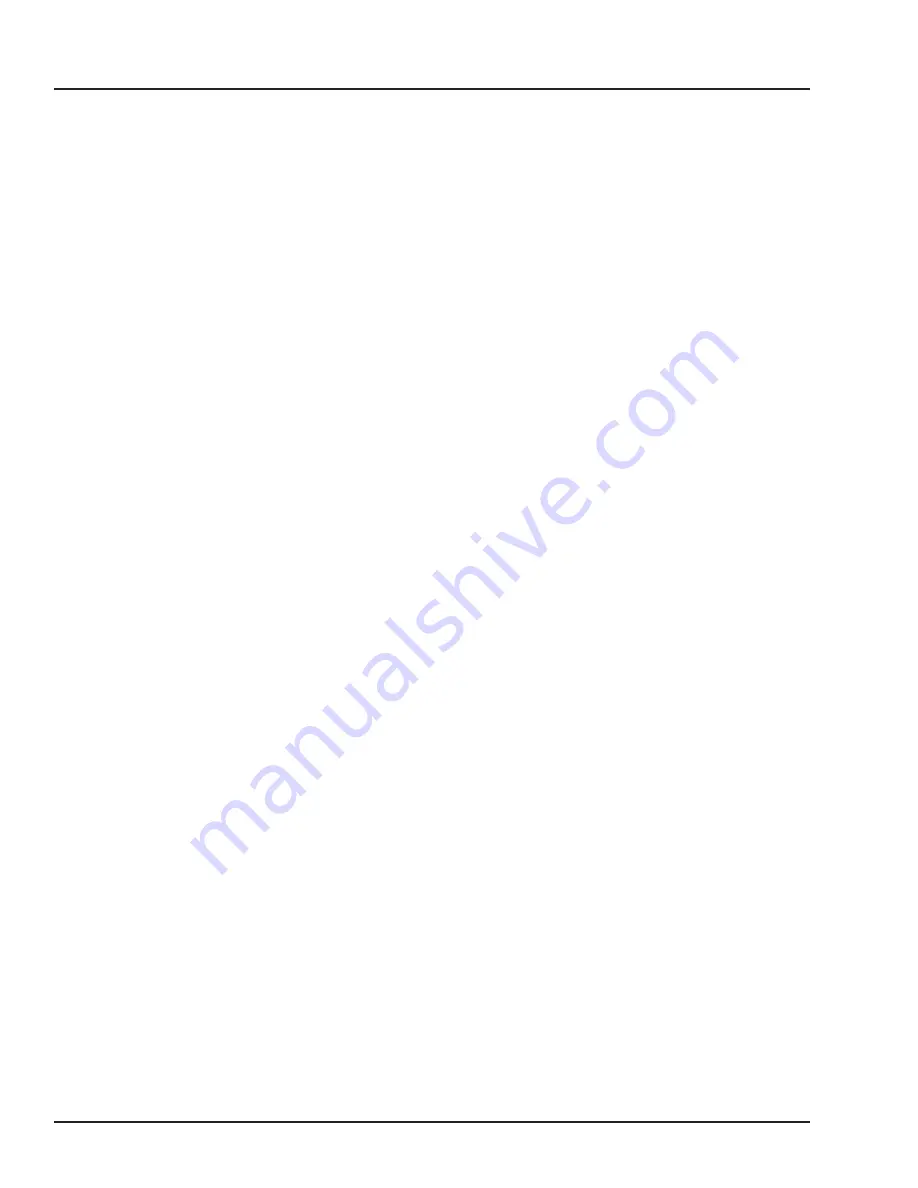
18
4111-0026 — Feb. 2019
© 2019 Systems, LLC
A ramp mount-weld on used with a formed angle
application is used when dock edge is damaged,
there is no dock steel securely anchored into the
concrete, and the dock height is too low and leveler
must be installed above this height to correct this
situation.
1. Remove all existing bumper material and
protruding objects from dock edge. Clean and
sweep dock edge free of debris and flammable
chemicals before installing unit.
2. Review and follow formed angle installation
instructions prior to leveler installation. See Page
20, Figure 10.
3. At chosen location for Edge of Dock leveler,
locate the center of space and mark a point half
of the base plate width to the left and right.
4. At the points marked to each side of center,
measure and mark points 7-3/4” below dock
level less height the unit is to be raised to locate
bottom of base plate. This will locate the top of
the base plate X” above dock level.
5. Using a proper lifting device, raise and position
the leveler base plate to marked position. While
holding base plate tight against dock face, tack
weld securely to dock steel on left hand end
of leveler. Check right hand end of base plate,
ensure that end is against dock steel and that
the bottom of the base plate is even with the
marks made previously. Tack right hand end
to dock steel. Support unit until final welding is
ready to complete.
6. Position bump blocks out approximately 5/8” out
from the edge of the inside flange of the bump
block to the end of the base plate. Position the
top of the tread cover plate on the bump blocks
to be flush with the top of the base plate. Tack
weld bump blocks to dock steel.
7. Place steel ramp plate in position, flush with top
backside of base plate. Mark along full length
of back edge of ramp plate. Slide ramp plate
forward over dock leveler the width of bushing
tool, approximately, 2”.
8. Place bushing tool on marked line at each end
of ramp to ensure proper alignment at both
ends. A Skil Roto Hammer #736 or similar tool is
recommended.
9. Using the back edge of the ramp plate as a
guide, groove concrete approximately 3/4” deep
by 2” wide, and should be the entire length of
ramp plate.
10. Slide ramp plate back into position with the top
of the ramp plate flush with the top of the base
plate. Tack weld each end and center of ramp
plate to base plate.
11. Using ramp plate as a guide drill (9) 5/8” dia.
by 5” deep holes. Install anchor bolts per
manufacturers specifications, and tighten
securely. Weld anchor bolt nuts to ramp plate
using a 1/4” fillet weld all the way around the
nut. Cut off any portion of the anchor bolt
exposed through the nut, and plug weld around
the top of the nut to the anchor bolt. Ensure
the top of the nuts are well rounded for smooth
rollover.
12. Complete bumper install:
a. Apply continuous weld across top of each
bumper. Skip welding is acceptable to
prevent warpage, but complete weld must be
completed.
b. Plug weld mounting holes to imbed.
13. Finish welding the base plate:
a. Weld the top of end base plate and first
hinge to imbed.
b. Weld top of each hinge tube to imbed
c. Weld vertically along each end of base plate
d. Fully plug weld all holes in base plate.
14. Installer must remove all welding slag, and
repaint welded areas.
15. Installer must adjust springs on all mechanical
Edge of Dock levelers to provide desired tension
for smooth operation. See page 30.
Ramp Mount - Weld On w/Formed Angle
INSTALLATION