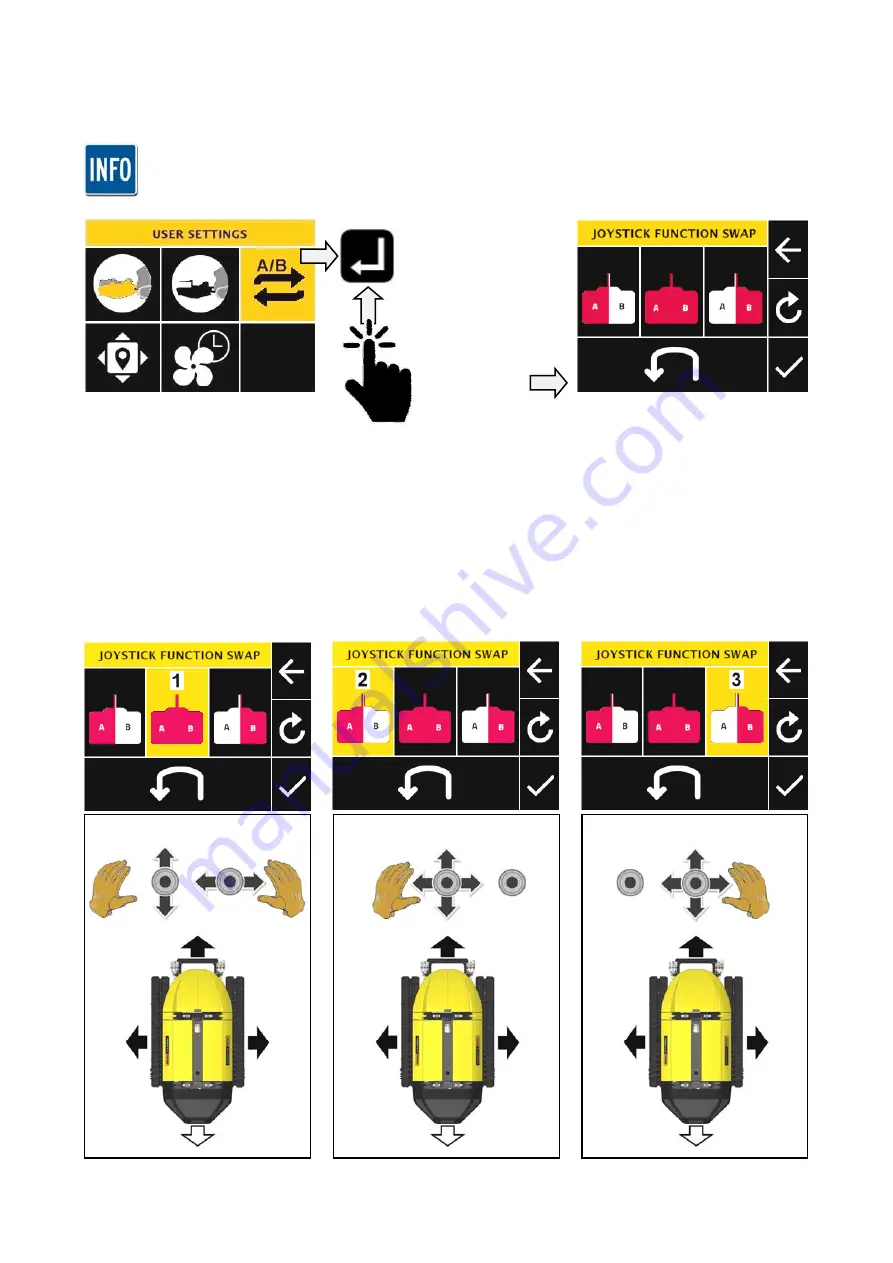
28
Joystick Function Swap & Travel Swap Settings
Allows users to customise the joystick functions and/or machine forward travel direction for
personal preference or to perform a specific task.
Changes to these settings are only retained in the systems memory for the duration of the operating
period - if the machine is switched off, all changes to the joystick and travel direction settings will
revert to default; this is to ensure that controls operate in a familiar manner for all users at start-up.
Highlight ‘Joystick
Swap Settings’ and
press ENTER’
button to access
sub-menu of the
joystick and travel
swap settings.
For joystick function swap refer to the settings below - if joystick function swap and travel direction swap is
required refer to settings on the following page.
Joystick Function Options for ‘Forward Drive’ Mode
1.
LH Joystick operates Travel / RH Joystick operates Steering (Default).
2.
LH Joystick operates Travel & Steering.
3.
RH Joystick operates Travel & Steering.
Joystick Function Swap Settings
Use navigation buttons to highlight the custom joystick setting.
Press ‘Enter’ to highlight ‘tick’, press ‘Enter’ again to confirm setting and exit to the ‘Home’ screen.
Default: LH for Travel
/
RH for Steer
LH Joystick operates Travel & Steer
RH Joystick operates Travel & Steer