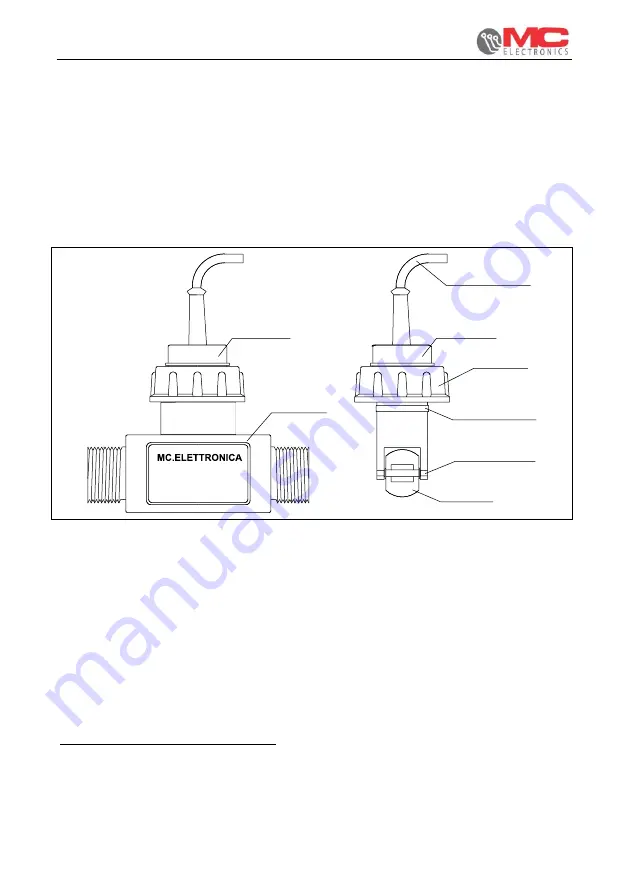
Installation and use
COMPUTER XP805
28
7.2.1 Maintenance of the flowmeter sensor
We recommend checking the cleanliness and state of wear of the flowmeter sensor
rotor periodically. Proceed as follows to carry out this operation:
1. Unscrew the sensor ring nut completely (Figure 9) and extract the sensor from
the main body (there will be some resistance from the O-ring);
2. Make sure that dirt is not found on the rotor or between the rotor and ceramic
axis;
3. Make sure there is no mechanical clearance on the rotor shaft
1
;
Figure 8
.
4. Reinsert the sensor, making sure that the fixing notches match
2
(Figure 10);
1
Excessive clearance means a range which is higher than 1 mm.
2
Before screwing the ring nut, it is necessary to remove the resistance of the O-ring
and check that the sensor does not turn inside its seat.
sensor
body
electric cable
sensor
ring nut
O-Ring
Rotor axis
in ceramic
rotor