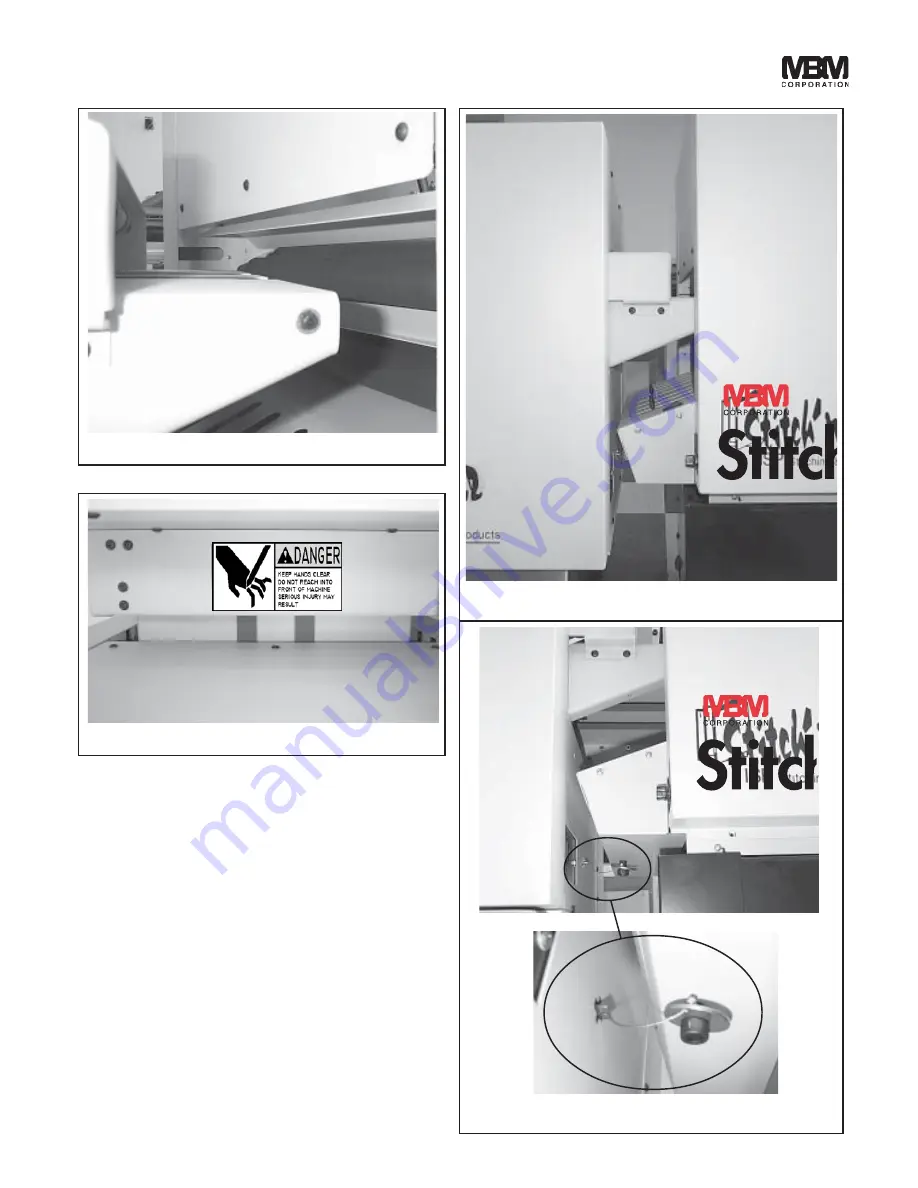
7
TRIMMER TO BOOKLETMAKER CONNEC-
TIONS:
1. Adjust the height of the trimmer so that the top
of the trimmer infeed table is about even with
the middle of the BookletMakers top discharge
roller (see fig 6).
2. Position the trimmer behind the BookletMaker
so that the trimmer's infeed table is centered
with the BookletMakers discharge, and slightly
away from the BookletMaker's top discharge
roller (see figs. 7&8).
3. Install the safety interlock key that is hanging
from the bottom of the back cover (see fig 9).
(Fig 6)
(Fig 7)
(Fig 8)
(Fig 9)
Summary of Contents for StitchFold
Page 2: ...Trimmer OPERATION MANUAL Trimmer ...
Page 22: ...21 NOTES ...